YASKAWA ELECTRIC VS-626MT
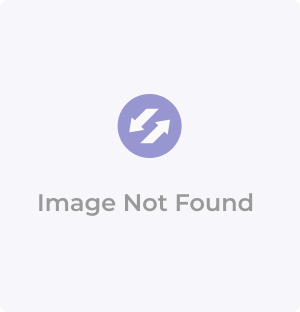
Description
Yaskawa VS-626MT AC Spindle Drive (Type CIMR-MT)
Part Number
VS-626MT
Price
Request Quote
Manufacturer
YASKAWA ELECTRIC
Lead Time
Request Quote
Category
AC Spindle Drive
Datasheet
Extracted Text
AC SPINDLE DRIVE VS-626MT ( TYPE CIMR-MT ) CONTENTS 1 . SPECIFICATION 2.,INTERFACE 3 . PROTECTIVE FUNCTION 4 . ORIENTATION UNIT 5 . DEMENSIONS DIAGRAMS 6 . CONNECTION DIAGRAMS ELEMEMTARY 7 . DIAGRAMS 8 . EXTERNAL TERMINAL LIST 9 . ADJUSTMENT 10 . LOCATIONS OF POTS AND CHECK POINTS 11 . BLOCK DIAGRAM AND WAVEFORMS AT CHECKS POINTS 12 . TROUBLE SHOOTING 1 . SPECIFICATIONS TYPE CIMR-MT7.5K CIMR-MT11K CIMR-MT15K Nominal Rating 7.5KW 11KW 15KW Applicable Continous 5 .5KW 7 .,5KW 11KW Motor 30 Minutes 7 .5KW 11KW 15KW Power Supply 3 Phase 50/60HZ 200/220V (±10%) 60 HZ 240V (+5%,-15%) Power Supply Capacity 12KVA 18KVA 22KVA Main Circuit 3-Phase full wave rectification Transistorized PI4M Inverter Maximum Output Voltage 160'1 Maximum Peak Output 55A 18011 100A Current 60 Sec . Rated Output Current 45A I65A 85A Speed Control Range 1 :100 Constant Output Range 1 :3 Rated Speed 4500 RPM or 6000 RPM Speed pad ±0 .5% 100% Load Fluctuation luctuation Fluctuatit-n ffset 0.1% at 10 to 100% Speed Acceleration 0.5 to 6 .5 sec . (every 0.5 sec) Deceleration Operating and Braking Reversing Operation and regenerative Methods Braking Cooling Method Fan Cooled Type Ambient -10 to 80% relative humidity) Temperature +45°C (Under 2 . INTERFACE 2 .1 INPUT INTERFACE Rated Speed Reference ±10V DC Input Resistance 15K Ohms Running Signal +12V Run OV Stop Torque Limit +12V Low Torque OV Nigh Torque 2 .2 OUTPUT INTERFACE Zero Speed Detection Contact closes when the motor speed drops to 1% or lower than the rated speed Speed Agreement when the motor Contact closes Detection speed is within ±15% of the commanded speed Excessive Deviation Contact closes when the motor Detection speed drops to 50% or less of the commanded speed . Trouble Detection Contact closes or opens when any trouble is detected . when the Overload Detection Contact closes current goes over the set current limit . Speed Detection Contact closes when the speed drops under the set speed Speed 1mA meter Meter Drive One way swing DC (Full scale Max . speed) at PROTECTIVE FUNCTIONS 3 . OC Checks the Main DC Current and protects the Power Transistors OL Checks the Main AC Current and protects the Moter and Power Transistors . OV DC Voltage and protects Checks the Main the Power Transistors . OS Checks Motor Speed and protects the the Motor and the Machine . FU (Fuse Detects if the Main fuse has blown Blown) UV (Under Checks the DC Power source for the Voltage) Control Circuits . 4 . ORIENTATION UNIT (Option for Machining Centers) 1) Positioning Accuracy- ±0.5mm or; less 2) Position Detector a . Sensor FS-200 (joint type) or FS-1378 (separate type) b . Magnet MG-1378 t E z In O 65 W 1 a: tr) N V V) V7 '- Z. W Q Q Z u dl Q E Z z O L W al 009 su t ~s at . ~+ 11 . 1 1 o °t N L O V W 7 f J unit) orientation (without Diagram Connection a) 43- a) a a, K N CO a)~- I +gym -V CO 6 NcL-2V'M N ~ d >S. d4 Z. C°= J C- C]11 CLG- qv A N r1 A A C O I C o .l, "r- +J a) 4-3 Ri (1) 4-3 .r- U C1 C +-+ C N E p °- M O 2 " U a o O a) c 0 o s.. a b to - . r +-3 a) a) s a) U- 4J - f.. "~-- > N C1 r U C ..- c 0 a) E Rs Q ",- of +J N tU C ~ L. J ~ N a C V a v- +> > 1] X C1 a) L Cr W cn oC Q to L -4-j O 'l7 a NH a C1 N L. S- to O C7 C9 Q G1 0 E O L. Rf 1 0 :. e d b c F- 1-1 i O ~ ~ ~ ~ o .- o V J4.1 - ~ + ;~ _7 r1 r V 0 U 4 T w o 19 " c o a _i..J a) 4J O E a = O Y o > U w N L" 0 C Q1 Q U i C +~ > 4J 0 N r-~ ~- C ~ d y"- CL .J N 1 "" ¢ al L_ X W +~ C) O N L. O L. d -_s v) 3 0 a N M M M M A s s >>s .JY l O . u r -79-1 '~ as ~ I " ' s- O C O U CI 01 E^ 1 ~ fY 1 D t-"+ 1 U t .4 4. 2 f S ~^ ai r1 ~ ~ 1 " + L i . ; f Y ~e~l l r` L ~ . w i "+ v 1 1 I 1 i, V J 1 ~ t't ~ -' . 1 a~i+ t i . eca-yl- > +~ . . Y Z A s A w f oc st ilt 1 u " au 9t 4J 1 v 11~ c '~Wh St e . W i -r -7 ab .-. i w 4 a~ E n tZ X i lIQ f, It V V r of c a r 61 r0 r e SI n N 1 LI 1 i s 91 l¢ f S1 f 1 fl t LI1 / el `1 °a to olu < LI . f~.pN . I .,I vv:vvWwvv .wlW:Lylvvvv of IT 6 B ~ Alttiitvt ." .; ..y"= . ".w. 134 :~w 1 + ~ hgw .ti ~r 9 ' t ~ s i 1 . 1 Ji" p l l r~-+6 1 ' -~ rt Z al li 4 W . s 4 ft Terminal List & External Terminal Description Name Symbol j R, S, T Main Power Input 3-phase 200/220 VAC ±10%, 50/60 Hz . Control r, s, t Power Input 3-phase, 200/220 VAC ±10%, 50/60 Hz U, V, W Motor Connection Connect U, V, and W to the corresponding motor v CC terminals . P, B Resistor Connection Connected before shipment . Open 23, 25 Spindle Condition Dete- Normal condition : ction Control 23, Abnorm of spindle control circuit abnormal 24 Spindle Detection condition : Detection Closed 33, 32 Speed Reference Input 32 is connected to OV, 33 is connected to speed reference (±1OV) 13, 14 Resolver Input 14 is connected to OV, 13 to resolver terminal C, and 14 to F . A connected to OV, 9 to resolver terminal A, 9, 10 ~esolver Phase Exci- `10 is ftation land 10 to 0 . U oC 11 Resolver Phase B Exci- ~11 to resolver terminal B tation 0 z 0 E and ground it . 12 ;Grounding Connect E to resolver terminal U 1OmA 6, 7, 8 t12V Output 7 is OV common,. 6 is ±12V, 8 is -12V . can be supplied . Usable for speed setting, etc . When +12V 50, torque limit is ineffe- 50 Torque Limit is applied to . ct interlock is not ineffect 37 Start Interlock When +12V is applied to 37 (CON-() External Terminal List Terminal Name Description Symbol 51, 52 Output for Tachometer I DC 1mA with 52 negative and 51 positive . 44, 45 Zero Speed Detection and 44 45 are closed, when speed is detected . 47, 48 Speed agreement Detec- are 47 and 48 closed, when speed agrees with tion command . 42, 43 Excessive Deviation When 42 and 43 are closed, excessive deviation Detection is detected . 49 Speed agreement for When 49 is OV, speed conforms . Orientation 46 Zero speed for Orien- When 46 is OV, zero speed is detected . tation Torque reference to Orientation U 16 Torque reference from U Orientation J 0 F- z Speed reference to o U Orientation Speed reference from Orientation FOR TYPO YS-626 A.C . SPINDLE DRIVE Instructions for Removal and Installation of the Spindle Drive Circuit Boards 1 . Shut off the Control and turn off Main the Power Switch 2 . Open the door to the Spindle Drive Cabinet 3 . Remove the clear plastic cover on Spindle the Drive . 4 . Make a list of all the wires onto the terminal strips on both the large and small boards on the spindle drive . These strips are located on the left side of both boards and also there are some small terminals on the bottom of the small board . 5 . Remove all wires from the board to be replaced *CAUTION : Insure that your wire list is complete and correct before removing any wi res 6 . Remove all ribbon connectors and if necessary remove the connector with the yellow wires at the top of the large board (it has 5 straight pins in a row) 7 . If the large board is to be removed : At the top of the board there are 2 pairs of Red and White wires (the wires are wound together as a twisted pair) Trace these back to their white connectors and pull the connectors apart . *NOTE : These plugs are labeled and I 2 . 3 . The small board is held down by plastic squeeze tabs . To remove the board, squezze the tabs together with a pair of needle-nose pliers while gently lifting the board . When the board is free, lift it gently away ,and set it aside . *CAUTION : When handling circuit boards ensure that they are set on a not wet surface . If possible set them on plastic of some sort . 9 . The large board is nonnally held down by 9 screws,8 of which are located on the outside edge of the board . The remaining screw is located in the very middle of the board . Remove the screws and gently lift the board free . 10 . To install the new boards simply reverse the above procedure . All of the Ribbon cables and all of the connectors are keyed fit only to in one direction in their appropriate sockets . Ensure that all of the wires on are the terminal strip in their proper location and that they are tightly screwed down . If you have any questions or problems please : call YASNAC Service Department Phone Number (312) 564-0806 Please return the bad boards to : YASNAC America Inc . Attn : Field Service Doe-partnent 305 Era Drive Northbrook, Illinois 6M$2 Q . ADJUSTMENT Adjustment of Reference 1 . Speed means are found on the JPAC-C026 (A part with a parenthesis (C means part a parenthesis are found on the JPAC-C051 with ADJUSTMENT SYMBOL FUNCTION 1RH(A) OFFSET adjustment Adjust CH4(A) within ±3mV when speed of speed reference reference is ,zero . W(A) maximum 2RH(A) LIMIT adjustment Adjust the of speed reference speed reference . ICCW Normally set full CW . Speed Reference 3RH(A) GAIN adjustment of Adjust the CH4(A) to +6.OOV at 100% forward reference forward speed reference . 4RH(A) GAIN adjustment Adjust the of CH4(A) to -6.OOV ±3% at reverse reference 100% reverse speed reference . 2 . Adjustment of Speed Feedback SYMBOL FUNCTION ADJUSTMENT 6RH(C) ZERO adjustment of Adjust CH3(C) within ±3mV when speed feedback is zero . 5RH(C) GAIN adjustment of Adjust CH3(C) to ±6 .OOV at rated speed feedback (- : forward, -F : reverse) 3 . Adjustment of Speed SYMBOL FUNCTION ADJUSTMENT NFB(C) Adjust Adjustment of Speed to rated speed at rated speed reference . there If is a difference between forward and reverse, adjust by 4RH(A) . 1RH(C) OFFSET adjustment If there a forward and is difference between of Speed reverse at low speed, adjust so they are equal . 4 . Adjustment of Exciting Current SYMBOL FUNCTION ADJUSTMENT 8RH(C) Adjustment of excitation current Adjust the CH6(C) and CH7(C) to ±3V peak . CH6 _+3V ONH7 -3V 90° el . 5RH(A) Adjustment of Adjust the excitation current at zero speed minimum excitation reference and zero torque reference . current 6RH(A) Inclination adjust- ment of excitation 100% current against speed 6RHI Im- 5RH --> Absolute Speed 7RH(A) Inclination adjust- ment of excitation current against - ---------%" 100.1 secondary current 7RH IM 55-RRHu ;" Absolute Secondary Current of Basic 5 . Adjustment Circuit SYMBOL FUNCTION ADJUSTMENT ±O-1V 2RH(C) Voltage Adjust so is +12.OOV adjustment of CHI(A) DC supply (+12V) ±O-1V 3RH(C) Voltage adjustment of Adjust so CH3(A) is -12.OOV DC supply (-12V) 7RH(C) Frequency adjustment Adjust so CH11(C) is 144KHZ ±1% of logic circuit 11RH(C) Balance adjustment of Adjust so that of -res . voltage is the resolver excitation same level as 13 -res . voltage . voltage f :9KHZ±l ;~ I 9 d-res . 0Ilk 10 0° lec . 11 H . /3 -res 12 19RH(C) Offset of Adjust remove the DC component from adjustment to phase oCcurrent amp the AC output current . 20RH(C) Offset adjustment of phase /3 current amp to the 16RH(C) Carrier frequency Adjust to 2KHZ-3KHZ according adjustment of PWM specification . not used . 17RH(C) Carrier frequency Usually this function is adjustment of PWM Set full CCW . 18RH(C) against speed minute T Adjust Ito 125% of the 30 LIMIT Level adjustment of (C) current limit rated current . SLIP Slip frequency FREQ(C) adjustment 4RH(C) Slip frequency i adjustment against speed Adjust to 105% of the 30 minute 12RH(C) Current level adjust- rated current . ment of OVERLOAD detection Cont . 5 . SYMBOL ADJUSTMENT FUNCTION 13RH(C) Adjust to 60-120 sec . according to Time adjustment of . detection specification OVERLOAD of rated IORH(C) Level adjustment of Adjust to 110% speed . Over Speed detection of rated voltage 15RH(C) Level adjustment of Adjust to 84% . Low Voltage detection 6 . ADJUSTMENT SYMBOL FUNCTION 9RH(A) Adjust within 1% of rated speed . Level adjustment of zero speed detection commanded speed AGREE(A) Adjust to x_15% of Level adjustment of speed agree detection commanded speed at low IORH(A) of Adjust to -.15% of Offset adjustment speed agree detection speed range . (-15%) commanded speed I1RH(A) adjustment of Adjust to 1-15% of the Offset . speed agree detection at low speed (+15%) Adjust to 50% of the commanded speed DEV-A(A) Level adjustment of detection deviation 7 . ADJUSTMENT SYMBOL FUNCTION TIME(A) of acc/dec Selection time limit 100% speed reference T is equal to the time set by the . DIP switch 44 T 7 . Cont . SYMBOL FUNCTION ADJUSTMENT 8RH(A) Level adjustment of Normally the current is not limited during current limit at deceleration . (8RH is set full CCW) to But if the load has a large and a deceleration inertia large current flow circuit through braking at deceleration, 8RH adjusted to should be reduce the current . 8 . FUNCTION ADJUSTMENT SYMBOL METER(A) Scale adjustment of Adjust the tachometer at rated speed . ammeter should be Tachometer A 1ma DC full scale used for the tachometer . Adjust rated . NDET(A) Level adjustment of to 10-30% of speed (0.6V-1 .8V at CH8(A) ) speed detection If the speed goes under the set level, . terminals 40 and 41(A) will be closed IDET(A) Level adjustment of Adjust to 0-200% of rated 300 ) current detection current . If current goes over set level, terminals 200 38 & 39(A) will close . 100 10 5 IDET adjustment of Can adjust 10-100% of rated current when ILIM(A) Level current limit 12V is applied at terminal 50(A), otherwise it is set by TLIM. 10 Locations of Pots and Check Points 1 . Control Board rrrm-~+no"ntnar rte~ttutru~ :u 1 t . ~~ " r SLIP FRE61 rrto CHI _ .1p .i tt TLIMIT Z ' 1 1 . . f"~1 _CH-3 8 CH4 . r IRH to 1 . CH 5 CH6 c i: ~ ~\ "ntttt" fi~:it ' '~C~tlsan a-RH ds :ILUtt~.~. ,1y tt ~RH '111 ~ t'uN t tt>~tum.~ttn~t 6H r7 ~7*..'ii _irrt R' moo olt 2H ,,I< - tttitt~ =stn r Hill gRH Solo LH12 unttuu CHt3 till r FOR CHI RH R J I I r IZRN t qtr r 1 r i .l Ijn'!t1 t . . t ;~+RH n~nt IS r 06RH ~"~utt~s1~11it ~sau*I :"C tttTi ~littll l RN Moll y ~wu 2ORH mui ,1 rl~" .. .. i~" f a as 1 _ I~III 2 . Auxiliary Board DET N L ; D=T .-: JPAC-CO=s 3 cow -" CTCOOSOIO I I II I . II I -!I IIi` -~Iloffl .0.9c CH I K T Idc o_SO23 iLCr HL 1! c its 1! CH .r Cr+ Lh" . s il, ~= ~Nc i .M_ ._." "" ~ i got 4.461 1141-4 . ~! lI CH ' " r ~ r. r :: ao ]:U ITV W .2-C [12 :IE02 Y "KC ~~ CD==0 49 so so Block Diagram -%nd waveforms at` necks points ; V ~+ u 1 yr ~v r- s ~ I o 1 , o[ a1 . w = I ~p 01 1 rl L 1 z 4 T I Z . TROUBLE SHOOTING Trouble Check Item IIS alarm 1 . Check the resolver wiring The figure at the right shows the wave form between terminals 13 and 14 (C) 2 . Check the speed reference from N/C (Terminal 33 (A)), output AMP (CH 3(A)) of speed (CH4(A)) and speed feed back alarm 2 . QL Check the if specifications of the drive load to see it exceeds the unit 2 . Check the starting and stopping operation frequency OV alarm 3 . 1 . Adjust 8RH(A) if it occures during deceleration 2 . Check the AC Supply Main Voltage 3 . Check the Power Transistors and wiring of the braking circuit When the power turned on immediately after it has been turned is off . There is a chance that the OV alarm will appear so wait three or four minutes before turning on again 4 . QC alarm 1 . Check the six Main Power Transistors for shorts or 2 . Check the output circuit (including the motor) excessive impedance to ground 5 . FU alarm See Item 4 6 . Motor does not indicated refer to there are any alarms Check the alarm Leds if start items 1 through 5 2 . from N/C (Terminal 33(A)), the output Check the speed reference (A)) of AMP (CH4 (A)) and the speed feed back (CH3 speed (A) should be 12V) 3 . Check the start interlock signal (Terminal 37 4 . Check the wiring of resolver and motor 1 . Check the resolver wiring 7 . "Z-SPD" doesn't 2 . -Adjust 1RH(A) and / or,6RH(C) come at zero speed 8 . Adjust 1RH(A) and / or 6RH(C) "Agree" doesn'-t 1 . come when speed is correct circuit Check the Power Transistor in the braking 9 . The thermal relay ' 1 . in the braking 8RH (A) circuit trips 2 . Adjust ring deceleratio ORIENTATION UNIT (TYPE JPAC-C050) Specifiction 1 . Item Specification Terminal Supply Single-phase (-15A-+10%) . . . Power 200/220V 200V . R1-T 50/60Hz 220V . . . . R2-T DC Power Supply DC 12V ±10% 50mA (For Type FS-200) -12V(Black) . . .4 For Magnetic Sensor OV(Red) . . . . 16 --------------------------------------------------------------------------- DC 15V ±10% 50mA (For Type FSD-1378) OV(C) . . . . . . 16 -15V(B) . . . . . 15 Connect 4 to 15 Command 1 Orientation On at orientation start Gear Position On 2 when in Low Gear Off when in High Gear Speed Reference ±6V/±100% speed 17 Reference -3V/+100% Torque 8 Zero Speed Detection On at zero speed 7 ;peed Agree Detection "L" at speed agree 6 'osition Detection 6V p-p-16V p-p 13(+) 14(-) )ri entation Speed :eference 12 rientation Torque 11 eference rientation Conculsio Contact closes when orientation is finished 9 10 Lion Speed 0-2.2% of rated speed in H gear Range 0-8.8% of rated speed in L gear circumference 120mm,0' )sitioning Accuracy ±0 .5mm or less on the Connection Diagram 2. Box (V~-626 xc MT) 1 1 peed 1 i 'eference A i i 1 f Orientation Unit i 1 i 1 NRer i t JPDC-C050 i 1 Orientation 11 i rRt~2 t Command I .Gear Selection ? TRS 1 $ 7~ / `17' i i I t5 F24") " Zero Speed t 1 I Orientation I 1 Conclusion 1 1 i tr 1 t t 10 Black B~ 14 (- trv) . Connect 15 to 4 when Blocl Base 6 c-isv) using FS-1378 iZEjff" EMI I ll E w 14 t-t MagnetSensor FS Whit 8 -200 MagnericSensor ~z FS- FS-1378 IFAC-Cado ZOO 150 Green A White p 14 (D ,s (- IV~) WW I Red c I&cor) Power Supply (/0) ~,4 sc=/loxz ~4 Co`rinect 15 to k ftK ~ ~i "tl !C ti 00 O v o W W d. W F- 0 37l W O V o ,'4 f V J C O 4 .r H Z N w V W E "r m o a v Z 'Z N Z ~ ~ ~ W V1 F- Q V > Z w far ... w = J 1' 5 Adjustable Pots Check Pins Terminals Holes for MTG Screw Dimension Diagram of Orientation Unit ADJUSTMENT 4 .- Adjustment symbol b Function LEVEL Move the motor in the forward direction slowly and chech the waveform at CHK4 . If the isn't 20Vp-p voltage ±0.5V, adjust Level to correct it . Level adjustment of posi- Ifthe waveform is like (b) : terminals 13, should be 14 switched tion detection ±0.5V 20V i (a) Correct Waveform Waveform ORIENT. SP Motor speed (not spindle speed) should be set over 30rpm in orientation mode . Orientation Seed Setting Example Speed adjustment in orien- NH Max . rated speed in H gear)= 4500rpm tation mode N REF (Max . rated speed reference )= 6V N OR (orientation speed)=50rpm . NOR Orientation Speed= NREF * 20V * Reference (CHK1) 50 x2011 .33 6 * 4500 . EH GAIN Adjust the gain, so there is no hunting when the spindle it stops L . GAIN orientation position . Adjust H . Gain in H gear Gain,adjustment of servo Adjsut L . Gain in L gear loop adjust so the spindle position coincides BIAS Select L gear range, orientation position . Fine djustment of with the proper orien- tation position spindle position coincides with FRICTION Select H gear range, adjust so . Fine adjustment of orien- the proper orientation position tation position in H Gear C O .r_ C C1 O r,~ _CO L a v {-' fv vi 3 c. C ~ tl W 4-- a u Si Q t a) "r C t/) O CC SL O O C ..) frlo ve .r u .t u u Ir z of s1 vw oQ N cc 0 ac LI !1 O f0 V) Q N tY sl - r tl fCj C tl N N tl N i C) 11 N 2 01 T.J I I I ~ 1 I ,~ I V V r L m d wa s .J-. a O t V L a 'a C N f_ O aJ 0 a d) "r L O h u L L ftt C'3 N a) K a O d Q ILI t h d N w (L O C C~ v N O fY d V O a O L 4 a U :_ O a 1 fn n
Frequently asked questions
How does Industrial Trading differ from its competitors?

Is there a warranty for the VS-626MT?

Which carrier will Industrial Trading use to ship my parts?

Can I buy parts from Industrial Trading if I am outside the USA?

Which payment methods does Industrial Trading accept?

What they say about us
FANTASTIC RESOURCE
One of our top priorities is maintaining our business with precision, and we are constantly looking for affiliates that can help us achieve our goal. With the aid of GID Industrial, our obsolete product management has never been more efficient. They have been a great resource to our company, and have quickly become a go-to supplier on our list!
Bucher Emhart Glass
EXCELLENT SERVICE
With our strict fundamentals and high expectations, we were surprised when we came across GID Industrial and their competitive pricing. When we approached them with our issue, they were incredibly confident in being able to provide us with a seamless solution at the best price for us. GID Industrial quickly understood our needs and provided us with excellent service, as well as fully tested product to ensure what we received would be the right fit for our company.
Fuji
HARD TO FIND A BETTER PROVIDER
Our company provides services to aid in the manufacture of technological products, such as semiconductors and flat panel displays, and often searching for distributors of obsolete product we require can waste time and money. Finding GID Industrial proved to be a great asset to our company, with cost effective solutions and superior knowledge on all of their materials, it’d be hard to find a better provider of obsolete or hard to find products.
Applied Materials
CONSISTENTLY DELIVERS QUALITY SOLUTIONS
Over the years, the equipment used in our company becomes discontinued, but they’re still of great use to us and our customers. Once these products are no longer available through the manufacturer, finding a reliable, quick supplier is a necessity, and luckily for us, GID Industrial has provided the most trustworthy, quality solutions to our obsolete component needs.
Nidec Vamco
TERRIFIC RESOURCE
This company has been a terrific help to us (I work for Trican Well Service) in sourcing the Micron Ram Memory we needed for our Siemens computers. Great service! And great pricing! I know when the product is shipping and when it will arrive, all the way through the ordering process.
Trican Well Service
GO TO SOURCE
When I can't find an obsolete part, I first call GID and they'll come up with my parts every time. Great customer service and follow up as well. Scott emails me from time to time to touch base and see if we're having trouble finding something.....which is often with our 25 yr old equipment.
ConAgra Foods