WARNER ELECTRIC TCS-210
Specifications
Ambient Temperature
–20° to +113°F (–29° to +45°C)
Anti-Drift Input
Nullifies integrator portion of control for faster brake response. Important at startup and for mid-roll starts
Brake Off
Removes brake current and applies antiresidual current to eliminate brake drag. Useful when changing rolls
Brake On
Applies holding brake voltage
Dancer Potentiometer
Provides the feedback signal of dancer position and movement for input to the control
Input
48 VDC @ 1.6 Amps continuous, 48 VDC @ 6 Amps intermittent, 1.6% duty cycle, 30 sec. on time, 8–12 VDC @ 1.5 Amps
Mounting
available as panel mounted with exposed wiring, or wall/shelf mounted with conduit entrance
Output
0–270 mA/magnet (running); 270–500 mA/magnet (stopping)
Datasheet
Extracted Text
Tension Controls Dancer Control for Electric Brake Systems Specifications MCS-203 (P/N 6910-448-014) Input 24–28 VDC @ 3 Amps (from MCS-166, 1.5 amps for single (Shown with MCS-166; 3.0 amps from dual MCS-166’s) or other power Housing) source. Output Pulse width modulated 0–24 VDC for 24 volt Warner Electric tension brakes. Ambient Temperature –20° to +113°F (–29° to +45°C). External Inputs Dancer Potentiometer Provides the feedback signal of dancer position and movement for input to the control. Brake On Applies full current to tension brake. Brake Off Removes brake current and applies antiresidual current to eliminate brake drag. Useful when changing rolls. Antidrift Input Nullifies integrator portion of control for faster brake response. Important for splicing and mid-roll starting. The completely solid state MCS-203 Dancer Control Module is designed for Mounting Available for panel mounting with exposed wiring or wall/shelf automatic web tensioning through the mounting with conduit entrance. Must be ordered with either wall/shelf or panel enclosures. use of a dancer roll. The MCS-203 can control two 24 VDC tension brakes in Requires enclosure, see page 66. parallel. It works on the concept of a P-I-D controller and has internal P, I & D adjustments for optimum performance regardless of brake size. MCS-166 Power Supply, (page 65). Typical System Configuration The complete system consists of: The control unit maintains a current output to the tension brake based on an analog input 1. Tension brake or the manual setting of the control tension 2. Dancer tension control adjustment dials. Varying the current from 3. Control power supply the control creates more or less brake torque 4. Pivot point sensor for tension adjustability. 5. Dancer roll assembly (customer Sensor supplied) Brake Dancer Roll MCS–203 Control MCS–166 Power Supply Warner Electric 800-825-9050 61 Tension Controls Dancer Control for Electric Brake Systems TCS-210 Specifications (P/N 6910-448-026) Input TCS-210 – 48 VDC @ 1.6 Amps continuous, 48 VDC @ 6 Amps (Shown with intermittent, 1.6% duty cycle, 30 sec. on time, 8–12 VDC @ 1.5 Housing) Amps. TCS-167 – 120 VAC, 50/60 Hz or 240 VAC, 50/60 Hz (Switch selectable). Output TCS-210/TCS-167 – 0–270 mA/magnet (running); 270–500 mA/magnet (stopping). Ambient Temperature –20° to +113°F (–29° to +45°C). External Inputs Dancer Potentiometer Provides the feedback signal of dancer position and movement for input to the control. Brake On Applies holding brake voltage. This closed loop tension control system Anti-Drift Input Nullifies integrator portion of control for faster brake response. Important at startup and for mid-roll starts. automatically controls tension on Brake Off Removes brake current and applies antiresidual current to unwinding materials such as paper, eliminate brake drag. Useful when changing rolls. film, foil, cloth and wire. Mounting TCS-210 – available as panel mounted with exposed wiring, or TCS-167 Power Supply, (page 65). wall/shelf mounted with conduit entrance. Note: When used with other than MTB mag- TCS-167 – available with open frame or wall/shelf mounted nets, a 68 ohm, 25 watt resistor must be enclosure with conduit entrance. added. Consult factory for details. Requires enclosure, see page 66. Typical System Configuration The complete system consists of five increases braking torque to elevate the components: dancer to the desired position, while reduc- ing brake current lowers the dancer. 1. Tension brake The closed loop dancer control system is 2. Dancer tension control completely automatic, limiting the need for 3. Control power supply operator involvement and the potential for 4. Pivot point sensor inaccurate tension control. The system offers Sensor 5. Dancer roll assembly (customer exceedingly rapid response that, in effect, supplied) corrects tension errors before they reach the The weight of the dancer roll or loading on work area of the processing machine. Brake the dancer determines the tension on the Dancer Roll web and the remainder of the system oper- TCS–210 Control ates to hold the dancer roll as steady as TCS–167 possible. When the dancer position Power changes, the Warner Electric pivot point Supply sensor tracks the direction and speed of the change and sends an electric signal to the closed loop control, which, in turn, relays a corrective signal to the Electro Disc tension brake. Increasing current to the Electro Disc Warner Electric 800-825-9050 62 Tension Controls Dancer Control for Pneumatic Brake Systems MCS-207 Specifications (P/N 6910-448-066) Input 24–28 VDC, 0.5 amps maximum (from MCS-166 or other power (Shown with source) Housing) Output Switch selectable current or voltage Voltage: 0–10 VDC Current: 1–5 mA, 4–20mA, 10–50mA Will operate most electric to pneumatic transducers available. Ambient Temperature +32° to +120°F (0° to +49°C). Control Input Pivot point sensor, MCS-605-1 or TCS-605-5 External Inputs Brake On Applies maximum output signal (voltage or current) to the transducer Brake Off Removes output from the transducer and applies minimum level The dancer control, MCS-207 is Anti-Drift Provides integrator reset function for mid-roll starting designed for automatic web tensioning Adjustments through the use of a dancer roll.The Front Panel Dancer Position: sets dancer operating position MCS-207 can control either a voltage to Gain: Controls overall system response based on change of pneumatic or current to pneumatic dancer input signal transducer with an air operated clutch Mounting Available as panel mounted with exposed wiring, or wall/shelf or brake. It works on the concept of a mounted with conduit entrance. Note: Must be ordered with P-I-D controller and has internal adjust- wall/shelf enclosure or with panel mount enclosure. ments of the P-I-D loops for optimum Requires enclosure, see page 66. performance regardless of the brake size. MCS-166 Power Supply, (page 65). Note: When used with other than MTB mag- nets, a 68 ohm, 25 watt resistor must be added. Consult factory for details. Typical System Configuration The complete system consists of: The control unit maintains an output to the tension brake based on an analog input or 1. Pneumatic tension brake the manual setting of the control tension 2. Dancer tension control adjustment dials. Varying the signal from 3. Control power supply the control creates more or less brake 4. Pivot point sensor torque for tension adjustability. 5. E to P transducer Sensor 6. Dancer roll assembly (customer supplied) Brake Transducer MCS-166 MCS-207 Power Control Supply Warner Electric 800-825-9050 63 Tension Controls Dancer Splicer Control for Electric Brake Systems Specifications TCS-310 (P/N 6910-448-042) Input TCS-310 – 48 VDC @ 3.2 Amps continuous, 48 VDC @ 12 Amps intermittent, 1.6% duty cycle, 30 sec. on time, 8–12 VDC @ 3.0 Amps. TCS-168 – 120 VAC, 50/60 Hz or 240 VAC, 50/60 Hz (Switch selectable). Output TCS-310/TCS-168 – 0–270 mA/magnet (running); 270–500 mA/magnet (stopping) on controlled output channel 0 to 90 mA holding channel. Ambient Temperature –20° to +113°F (–29° to +45°C). External Inputs Dancer Potentiometer Provides the feedback signal of dancer position and movement for input to the control. Brake On Applies holding brake voltage. Anti-Drift Input Nullifies integrator portion of control for faster brake response. This closed loop tension control system Important for start-ups. automatically controls tension on Brake Off Removes brake current and applies antiresidual current to unwinding materials such as paper, eliminate brake drag. Useful when changing rolls. film, foil, cloth and wire. Mounting TCS-310 – available as open frame or as NEMA 4 enclosure with TCS-168 Power Supply, (page 65). remote control station. TCS-168 – available with open frame or wall/shelf mounted enclo- Note: When used with other than MTB sure with conduit entrance. magnets, a 68 ohm, 25 watt resistor must be added. Consult factory for details. Typical System Configuration The complete system consists of five increases braking torque to elevate the components: dancer to the desired position, while reduc- ing brake current lowers the dancer. 1. Two tension brakes The closed loop dancer control system is 2. Dancer splicer control completely automatic, limiting the need for 3. Control power supply operator involvement and the potential for 4. Pivot point sensor inaccurate tension control. The system offers 5. Dancer roll assembly (customer Brake exceedingly rapid response that, in effect, supplied) corrects tension errors before they reach the The weight of the dancer roll or loading on work area of the processing machine. the dancer determines the tension on the web and the remainder of the system oper- Sensor ates to hold the dancer roll as steady as possible. When the dancer position Brake changes, the Warner Electric pivot point sensor tracks the direction and speed of the Dancer Roll change and sends an electric signal to the TCS–310 closed loop control, which, in turn, relays a Control TCS–168 corrective signal to the Electro Disc tension Power brake. Increasing current to the Electro Disc Supply Warner Electric 800-825-9050 64
Frequently asked questions
How does Industrial Trading differ from its competitors?

Is there a warranty for the TCS-210?

Which carrier will Industrial Trading use to ship my parts?

Can I buy parts from Industrial Trading if I am outside the USA?

Which payment methods does Industrial Trading accept?

Why buy from GID?
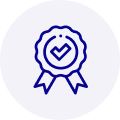
Quality
We are industry veterans who take pride in our work
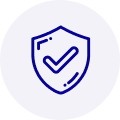
Protection
Avoid the dangers of risky trading in the gray market
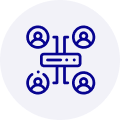
Access
Our network of suppliers is ready and at your disposal
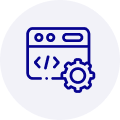
Savings
Maintain legacy systems to prevent costly downtime
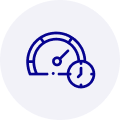
Speed
Time is of the essence, and we are respectful of yours
What they say about us
FANTASTIC RESOURCE
One of our top priorities is maintaining our business with precision, and we are constantly looking for affiliates that can help us achieve our goal. With the aid of GID Industrial, our obsolete product management has never been more efficient. They have been a great resource to our company, and have quickly become a go-to supplier on our list!
Bucher Emhart Glass
EXCELLENT SERVICE
With our strict fundamentals and high expectations, we were surprised when we came across GID Industrial and their competitive pricing. When we approached them with our issue, they were incredibly confident in being able to provide us with a seamless solution at the best price for us. GID Industrial quickly understood our needs and provided us with excellent service, as well as fully tested product to ensure what we received would be the right fit for our company.
Fuji
HARD TO FIND A BETTER PROVIDER
Our company provides services to aid in the manufacture of technological products, such as semiconductors and flat panel displays, and often searching for distributors of obsolete product we require can waste time and money. Finding GID Industrial proved to be a great asset to our company, with cost effective solutions and superior knowledge on all of their materials, it’d be hard to find a better provider of obsolete or hard to find products.
Applied Materials
CONSISTENTLY DELIVERS QUALITY SOLUTIONS
Over the years, the equipment used in our company becomes discontinued, but they’re still of great use to us and our customers. Once these products are no longer available through the manufacturer, finding a reliable, quick supplier is a necessity, and luckily for us, GID Industrial has provided the most trustworthy, quality solutions to our obsolete component needs.
Nidec Vamco
TERRIFIC RESOURCE
This company has been a terrific help to us (I work for Trican Well Service) in sourcing the Micron Ram Memory we needed for our Siemens computers. Great service! And great pricing! I know when the product is shipping and when it will arrive, all the way through the ordering process.
Trican Well Service
GO TO SOURCE
When I can't find an obsolete part, I first call GID and they'll come up with my parts every time. Great customer service and follow up as well. Scott emails me from time to time to touch base and see if we're having trouble finding something.....which is often with our 25 yr old equipment.
ConAgra Foods