SCHNEIDER ELECTRIC CP-8161-333
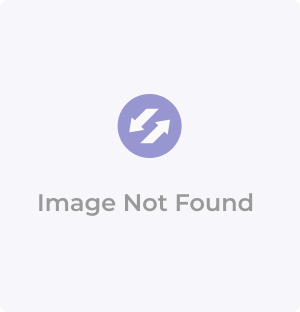
Description
Schneider Electric CP-8161-333 Electronic Programmable Controller Six Stage, Dual Setpoint
Part Number
CP-8161-333
Price
Request Quote
Manufacturer
SCHNEIDER ELECTRIC
Lead Time
Request Quote
Category
HVAC Controller
Datasheet
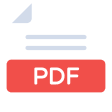
Schneider-Electric-CP-8161-333-HVAC-Programmable-Controller-datasheet1-2077118889.pdf
644 KiB
Extracted Text
CP-8161-333 CP-8161-433 Electronic Programmable Controller Six Stage, Dual Setpoint General Instructions APPLICATION Electronic six stage programmable controller with proportional output for heating, cooling and mixed air. The six stages can be programmed for heating, cooling and fan operation. SPECIFICATIONS Sequenced Control: Staged and/or proportional heating, proportional control of outside and return (mixed air) damper, staged and/or proportional cooling. Heating and cooling cannot operate simultaneously. Single Sensor Control: Heating, cooling and ventilation with individual heating and cooling setpoints. Unit Fan: May be programmed to cycle in the unoccupied mode. Relay Output: 6 relays can be programmed for heating, cooling or fan operation. Operational voltage level by dual-in-line switches. Mixed Air Sensor (optional): The controller can provide a separate mixed air control, or limit control in conjunction with proportional cooling output ramp. Cold Start: On power failure. Sensors: Any non-adjustable TS-8000, or TS-80000 Balco OPTIONS sensor. CP-8161-433 CP-8161-333 less controller board. Used as Control Output Voltage: See Table-2. slave in conjunction with CP-8161-333, Power Requirements: 24 Vac, 10 VA. CP-8261-333 or with TP-8121 or TP-8124. Power Supplies Available: 6.2 Vdc, 4 mA; 20 Vdc, 35 mA. ACCESSORIES These regulated and filtered power supplies must not be AD-8969-201 Offset resistor kit; 5, 10, 15, and 20 °F connected to +20, +6.2 or red lead of other supplies. AT-8122 Remote setpoint adjuster, dual scale 20 to Environment: 120°F (-6 to 49°C) Ambient Temperature Limits, AT-8155 Remote setpoint adjuster, dual scale 50 to Shipping and Storage, -40 to 160°F (-40 to 71°C). 250°F (10 to 120 °C) Operating, 0 to 140°F (-18 to 60°C). AT-8158 Remote setpoint adjuster, dual scale 55 to Humidity, 5 to 95% RH, non-condensing. 85°F (13 to 29 °C) Locations, NEMA Type 1 indoor only. AT-8258-101 Night setback scale for AT-8158 Connections: Coded screw terminals. TC-4111 Bulb thermostat Cover: Aluminum. THC-2 Enthalpy controller Mounting: Unit is provided with plastic track for panel TS-8101 Room sensor mounting. TS-8131 Room button-type sensor Dimensions: 3-7/8" high x 12" wide x 2-3/4" deep (98 mm x TS-8201 Duct/immersion sensor 305 mm x 70 mm). TS-8241 Diffuser sensor TS-8261 LIght fixture sensor TS-8405 5' (1.5 m) averaging sensor Table-1 RELAY CONTACT RATINGS. TS-8422 22' (6.7 m) averaging sensor Volts AC 50/60 Hz Contact VA Rating Inrush VA TS-8501 Outdoor sensor TS-8601 Selective ratio discharge sensor N.O. 125 1250 120/240 TS-810X1 Ser. Room temperature sensors N.C. 67 670 TSP-8101-103 Temperature transmitter N.O. 25 250 TOOL-201 Calibration kit for Schneider Electric System 24 N.C. 13 130 8000 Printed in U.S.A. 6-10 © Copyright 2010 Schneider Electric All Rights Reserved. F-18096-10 Table-2 SPECIFICATIONS. a Heating Cooling Mixed Air Relay (6) Outputs Part Mixed Pull-in Setpoint Throttling Output Setpoint Throttling Output Low Limit Minimum Output Number Air Start Voltage Differential b b c “SPA” “TRA” “IO1” “SPB” “TRB” “IO2” Setpoint Position “OP3” Point (Vdc) 2 to 15 3 to 6 Vdc Vdc 5.5 with 45 to 75 2 to 10 Factory 70 to 100 2 to 10 2 to 15 41 to 95 6.5 respect to °F °F set R.A. °F °F Vdc °F 0 to 100% 7 CP-8161-333 CLG 5 to 12 Vdc 0.5 Vdc (7 to 24 Factory Set Field (21 to 38 Factory Set D.A. (5 to 35 Factory 7.5 output D.A. only fixed b °C) 3°F change- °C) 3°F only °C) 10°F set 25% 8 (Output is able fixed T.R. 8.5 6 to 9 D.A. 9 Vdc) d d CP-8161-433 None None None None a Mixed air override is either accomplished from first or second stage cooling, or by outside enthalpy or temperature thermostats (purchased separately). b For 3 Vdc output change. c Can be used as separate mixed air controller or mixed air low limit in conjunction with cooling output ramp (then throttling range of mixed air would be the same as cooling ramp). d IO1 and IO2 become inputs on CP-8161-433. Figure-1 2 © Copyright 2010 Schneider Electric All Rights Reserved. F-18096-10 Figure-2 Figure-3 Pre- Installation INSTALLATION Visually inspect the package for damage. If damaged, notify Mount the device in an inside location near the controlled the appropriate carrier. Visually inspect the device for obvious equipment using the two slots in the track. Avoid locations defects. Return damaged or defective products. where excessive vibration, moisture, corrosive fumes or vapors are present, or where high radio frequency or Mounting screws are not provided. electromagnetic interference generating devices are near. NEMA Type 1 housings are intended for indoor use primarily to provide a degree of protection against contact with the enclosed equipment. F-18096-10 © Copyright 2010 Schneider Electric All Rights Reserved. 3 See Figure-2 for mounting dimensions. WIRING Make all connections according to job wiring diagrams and in compliance with national and local codes. All circuits must be wired NEC Class 1 unless only one CP-8161 with all low voltage (under 30 Vac) connections is used in the enclosure. Two separate No. 18 twisted pair wires (six turns per foot), low voltage are suitable for up to 1000 feet for the sensor leads. When more than one programmable controller is used in the same enclosure, one Class 2 transformer with proper VA rating should be used to power all programmable controllers. Never run line voltage in the same conduit with unshielded sensing element leads. Shielded cable must be used when it is necessary to install the DC signal leads in the same conduit with power wiring, or when it is known that high RFI/EMI generating devices are near. Terminate the shield at the controller only on the COM (-) terminal. Caution: Never connect the shielding or common to earth ground. Refer to the wiring diagram (Figure-3) for typical connection to power, inputs and outputs required by the application. Figure-4 4 © Copyright 2010 Schneider Electric All Rights Reserved. F-18096-10 Mixed air override to minimum ventilation by cooling stage 1 OPERATIONAL DATA or 2 (J8 to Pin D or E) or by external outdoor air enthalpy or The general operational capability of the programmer is temperature (J8 to Pin H and black jumper on Pins F and C). explained on page 12 in Theory of Operation. Control Arrangements The instructions are provided for three applications of staged control arrangements plus input and output options, as follows: A staged 3 heat/3 cool/ mixed air application is shown in Figure-3. As an option, position 8 on the cooling DIP switch can be placed in the “off” position. This will provide a true mixed air controller, and the mixed air will be maintained at the temperature set on the mixed air low limit setpoint. Turn the mixed air start point adjustment full clockwise to disable. A staged 3 heat/2 cool/fan cycle/mixed air application is shown in Figure-8. A staged 2 heat/2 cool/humidification/dehumidification is shown in Figure-9. Optional Inputs and Outputs Figures-4 and 5 show the application of optional control inputs and outputs. Optional Inputs • Night depression (adjustable). • Remote setpoints of heating, cooling and mixed air temperature. • Ratio discharge control for heating. • Outside air temperature or enthalpy override of the mixed air damper control to minimum ventilation when the outside air cannot cool. • Separate heating and cooling setpoint adjusters at the sensing location. Optional Outputs • Heating Hydronic valve control. SCR electric heat control, single or 3 phase power. • Cooling with chilled water valves. • Mixed air damper control with additional actuators in parallel. • Slaving up to 5 additional programmable controllers for parallel operation. • Heating and cooling lockout. Jumper/Pin Programming Functions The programmable controller block diagram, sequence of operating voltage signals and jumper/pin programming instructions are shown in Figures-10 and 11. Jumper/pin programming provides the following functions: Relay selection: The Vdc pins designated the pull-in voltage (via Jumpers 1-6) that is measured at terminals IO1, IO2 and COM. Heating voltage signal ramp, i.e., reverse or direct-acting (J7 to Pin A or B). F-18096-10 © Copyright 2010 Schneider Electric All Rights Reserved. 5 Figure-5 6 © Copyright 2010 Schneider Electric All Rights Reserved. F-18096-10 When the space temperature approaches the cooling setpoint Heating and Cooling DIP Switches (SPB typically 78°), the mixed air dampers are proportioned to The programming instructions for the heating and cooling DIP provide maximum cooling from the outside air. The dampers switches are shown in Figure-11. The DIP switches program are proportioned to the minimum ventilation position if the the relays for heat, cool or fan operation and select the mixed mixed air temperature approaches the low limit setting. air operating cycle. When the outside air cannot provide enough cooling, the controller provides 3 cooling stages (or will proportion chilled Jumper/Pin and DIP Switch Programming water valves) to maintain the SPB setting. The jumper/pin and DIP switch programming makes it The mixed air is returned to the minimum damper position possible to provide: when the first stage of cooling is energized. See programming An economizer mixed air cycle in conjunction with - instructions for other options. For applications requiring other combinations of heat and cool stages, simply select the – Up to 6 stages of heat or cool. staging relays by using the programming instructions for the – Any combination of heat and cool stages. heating/cooling DIP switches and jumpers. – Any combination of heat and cool stages plus a unit fan stage. Examples: – Proportional output signals for control of heating valves, cooling valves and SCR electric heat control. For a 4 stage heat/2 stage cooling application use factory settings but set switch 4 of the heating DIP to “on” and set Multiple cycles, such as 2 heat and 2 cool stages with switch 4 of the cooling DIP to “off”. Relays #1-4 will then be humidification and dehumidification stages. heating relays. The throttling range of heating remains 3°F A mixed air cycle with adjustable minimum ventilation which unless changed by adjusting TRA or TRB. Place Jumper J4 operates independently of the heating and cooling program. on Pin 8. The mixed air temperature may be set in the range of 41 to For a 6 stage cooling application, set switches 1 through 6 of 95°F by the mixed air low limit adjuster. the heating DIP to “off” and set switches 1 through 6 of the cooling DIP to “on”. The throttling range remains 3°F unless Deadband changed by adjusting TRB. Place Jumper J4 on pin 8, J5 on The deadband between heating and cooling is the difference Pin 8.5, and j6 on Pin 9. SPA can still be the setpoint for in the SPB and SPA settings. For example, the deadband is proportional heating. 13°F when SPB is set at 78°F and SPA is seat at 65°F. For 6 stage heating application, set switches 1 through 6 of the heating DIP to “on” and set switches 1 through 6 of the cooling Mixed Air Start Point DIP to “off”. The throttling range remains 3°F unless changed by adjusting the TRA. Place Jumper J4 on pin 8, J5 on Pin 8.5, The point at which the mixed air cycle starts to operate in the and J6 on Pin 9. Set SPA at 65°F, for example. The cooling heat and cool program is adjustable by using the mixed air ramp has control of the mixed air. Cooling switch 8 must be on. start point (MASP). Turn the MASP adjuster clockwise to To start to open the mixed air for cooling, set SPB at 70°F. increase the deadband between free cooling and operation of When TRB is set at 5°F, the mixed air cycle will start at 65°F the cooling equipment. (at 0% Min.). The Mixed Air Cycle will start at a temperature of The mixed air operating throttling range is the setting of TRB the SPB setting minus the TRB setting. when controlled from the cooling ramp signal. When an air supply fan stage is used (Figure 8), the fan is off When the mixed air temperature is 5° above the mixed air low in the program deadband. On a call for staged or proportional limit setting, the mixed air damper is positioned directly by the heating of cooling, the fan starts first. When the fan stage is mixed air ramp signal. The mixed air low limit control has a used, the fan must always be running while electric heat or 10°F fixed throttling range. direct expansion cooling is energized. If the mixed air temperature approaches the low limit setting, For heat pump applications, Relay 1 controls the unit the low limit proportions the outside air damper fully closed (or changeover valve. See the heat pump note in Figure-3. minimum ventilation position) 5°F below the setpoint, and For systems without a mixed air cycle, and with multiple cycle allows full opening of the outside air damper 5°F above the operation (Figure-9), the room temperature is maintained setpoint. without a mixed air cycle. The relative humidity is typically The adjustment and programming locations are shown in maintained in the range of 40-55% Rh. Humidity control is Figure-13. maintained by relays 5 and 6 which are controlled by the mixed air controller section and humidity sensor. OPERATION Blank charts are provided inside the cover to record the The CP-8161-333 is factory set to provide 3 stage heat/3 application jumper/pin and DIP switch programs for reference stage cool/mixed air cycle program. Refer to Figure-3. in future service work. When the space temperature drops below its heating setpoint (SPA typically 65°F), the controller provides up to 3 stages of heat (or will proportion an SCR electric heat control) to maintain the SPA setting. The mixed air is in the minimum damper position setting for ventilation. F-18096-10 © Copyright 2010 Schneider Electric All Rights Reserved. 7 HEATING, COOLING LOCKOUT Lockout stages of heating or cooling are accomplished by Step 5. Verify the relay contact action. The common relay braking the lead from the relay common terminal to the contact (C) must be made to the normally open contact (NO) controlled device with a relay or switch. See Figure-6. when the coil is energized (red light on). Replace CP-8161-333 if the relays are defective. Step 6. Verify the jumper/pin positions and DIP switch settings (Figure 11) for the required CP-8161-333 program. Reposition the jumpers or DIP switch settings. If they are defective, replace CP-8161-333. Step 7. Adjust the mixed air cycle start point. Step 8. Verify the calibration using the calibration procedure. Place the CP-8161-333 (or see Field Repair, Page 15) if calibration cannot be made. Figure-6 Step 9. Verify the minimum ventilation position setting. The position is adjustable from 0 to 100%. To lockout proportional heating or cooling valves, use a relay or switch. See Figure-7. CALIBRATION Use a 20,000 ohm per volt VOM. Step 1. Remove the sensor lead connections from terminals ISA to 6.2 and replace with a 1000 ohm +.1% resistor (Tool-203). Step 2. Turn SPA until the voltage at terminals IO1 to COM is 6 Vdc. Hold the SPA knob in position and rotate the metal indicator counterclockwise until over 70°F on the dial scale. Step 3. Turn SPB until the voltage at terminal IO2 to COM is 6 Vdc. Hold the SPB knob in position and rotate the metal indicator counterclockwise until over 70°F on the dial scale. Step 4. The controller is calibrated. Remove the 1000 ohm test resistor and reconnect the sensor leads. Figure-7 CHECKOUT PROCEURE (For tracing a controller malfunction) Use a 20,000 ohm per volt VOM for test readings. Step 1. Provide 24 Vac, 10 VA, 50/60 Hz supply power to terminals 24 and 24G Step 2. Verify the voltage at terminals +20 to COM and +6.2 to COM. If these voltages are not present, replace CP-8161-333. Step 3. Verify the sensors. Test the sensor leads to terminals ISA to +6.2 and ISB to +6.2 for approximately 1000 ohms resistance. Replace defective sensors or correct the wiring. Step 4. Verify voltage outputs 15 to 2 Vdc at terminal IO1 and COM, and 2 to 15 Vdc at terminals IO2 and COM. Verify 5 to 12 Vdc at terminals OP3 to COM. If these voltages are not present, replace CP-8161-333. 8 © Copyright 2010 Schneider Electric All Rights Reserved. F-18096-10 Figure-8 F-18096-10 © Copyright 2010 Schneider Electric All Rights Reserved. 9 Figure-9 10 © Copyright 2010 Schneider Electric All Rights Reserved. F-18096-10 Figure-10 F-18096-10 © Copyright 2010 Schneider Electric All Rights Reserved. 11 Figure-11 Figure-12 Note: Programming aid for selection of jumper/pin locations and DIP switch settings for application programs are not shown in these general instructions. Mark the jumper/pin locations and DIP switch settings in the boxes above and inside the CP-8161-333 cover. 12 © Copyright 2010 Schneider Electric All Rights Reserved. F-18096-10 THEORY OF OPERATION The mixed air controller accepts the mixed air sensor The CP-8161-333 Programmable Controller can be resistance signal and will override the zone cooling ramp to operationally described by dividing the controller into basic provide a proportional mixed air low limit. functional blocks. Refer to the controller block diagram (Figure 10). The mixed air controller has a fixed throttling range of 5.5°C (10°F). Auxiliary pins are provided for other throttling range Zone Thermostats (TS-8000 Series) The zone thermostat selections. The mixed air controller setpoint 41 to 95°F (5 to employs a 1000 ohm 21°C (70°F) resistance type (Balco wire) 35°C) establishes a minimum mixed air temperature control temperature sensor. Any non-adjustable TS-8000 Series point. When the mixed air low limit is reached, the mixed air sensor can be used. This sensor increases in resistance with actuator is proportionally controlled in order to maintain this an increase in temperature (3.96 ohms per °C or 2.2 ohms per low limit temperature. °F). This change is detected by the heating controller and cooling controller in the CP-8161-333. As an option, position 8 on the cooling DIP switch can be placed in the “off” position. This will provide a true mixed air Heating Controller Section The heating controller input controller and the mixed air will be maintained at the accepts the zone thermostat resistance signal. The input temperature set on the mixed air low limit setpoint. Turn the converts this resistance signal change into a DC millivolt M.A.S.P. full clockwise to disable it. signal change. The DC millivolt signal is then amplified, producing a 2 to 15 Vdc output at terminals IO1 and COM. The operating position, with respect to the cooling control Selection for direct-acting or reverse-acting operation is made outputs, is adjustable by setting the mixed air start point by positioning Jumper J7 to Pin A (reverse-acting) or B potentiometer. (direct-acting). The heating controller output signal is used Mixed Air Override An option that provides a method of internally to operate the heating relays or to position an limiting the volume of outside air taken in when the outside air external proportional heating controlled device. Adjustments is unacceptable for free cooling. The input signal is derived are available for setpoint 7.22 to 23.9°C (45 to 75°F) and from either: system throttling range 1.1 to 5.5°C (2 to 10°F). Outside enthalpy or temperature override thermostats: When Cooling Controller System The cooling controller input also Pin F is jumpered to Pin C, the override condition is created by accepts the zone thermostat resistance signal. The input an open circuit between COM and TIE; override is prevented converts this resistance signal change into a DC millivolt by a closed circuit between COM and TIE, or signal change. This DC millivolt signal is then amplified, producing a 2 to 15 Vdc output at terminals IO2 and COM. Signal from stage 1 cooling (J8 jumper connected to Pin D) This output is used to operate the cooling relays as well as and no connections to TIE, or sequence the mixed air dampers if the cooling DIP switch Signal from stage 2 cooling (J8 jumper connected to pin E) position 8 is “on”. This output is also available to operate and no connections to TIE. external proportional cooling controlled devices. Adjustments are available for setpoint 21 to 37.8°C (70 to 100°F) and Minimum Position Section The minimum position section system throttling range 1.1 to 5.5°C (2 to 10°F). establishes the minimum DC voltage level to which the output of the mixed air controller is allowed to fall. This DC voltage Mixed Air Thermostat (TS-8000 Series) The mixed air output between OP3 and COM provides the operating signal thermostat functions identically to the zone thermostat for the mixed air actuator. described above. The resistance change of the mixed air thermostat is detected by the mixed air controller section of Heating/Cooling Sections The six relays incorporated in the the programmable controller. CP-8161-333 Programmable Controller can be programmed to operate in either the heating or cooling mode. These relays Mixed Air Controller Section The output at OP3 is factory are programmed by positioning the heating and cooling DIP set to follow the zone cooling controller ramp (by having switches in the “on” position. Note: Heating and cooling DIP cooling DIP switch #8 “on”) to provide a 6 to 9 Vdc signal to switches cannot both be in the “on” position; The operating the mixed air damper actuator as the zone cooling controller reference for the pull-in voltage of the relays can be output changes from 3 to i6 Vdc. programmed by placing the respective J1 through J6 jumper on the proper operate reference pin. As the voltage from the heating or cooling controller increases through the respective Table-3 Mixed Air Controller Auxiliary Throttling Range. heating or cooling selector DIP switch, the relays will operate a Add between Aux. T.R. Pins a For Total T.R. °F of: when the voltage matches the operate reference selected. Resistor of Value: There is an interstage time delay on unit start-up. 11 10 MEG As an option, relay 1 can be programmed to operate from both 12 5.1 MEG the heating and cooling controller for fan operation in the 13 3.3 MEG unoccupied mode. 14 2.4 MEG 15 2 MEG LEDs (light emitting diodes) are provided for each relay stage to indicate the operating status. These LEDs will be “on” when 16 1.6 MEG the relay is energized. 17 1.5 MEG 18 1.2 MEG 19 1.1 MEG 20 1 MEG a No additional pin or jumper setting required. F-18096-10 © Copyright 2010 Schneider Electric All Rights Reserved. 13 Figure-13 Pin and Jumper Location. 14 © Copyright 2010 Schneider Electric All Rights Reserved. F-18096-10 Figure-14 TSP-8101-103 Temperature Transmitter for Temperature Control Plus Temperature Indication Used with CP-8X61-333 Programmable Controller. F-18096-10 © Copyright 2010 Schneider Electric All Rights Reserved. 15 MAINTENANCE Regular maintenance of the total system is recommended to assure sustained optimum performance. FIELD REPAIR Replace the plug-in circuit board containing the Heating and Cooling Controllers (BDZD-961-1) with their respective setpoint and throttling range adjusters (see Figure-13): 1. Remove 24 Vac power to CP-8161-333. 2. Pull circuit board straight out of the CP-8161-333. 3. Replace circuit board with functioning unit (BDZD-961-1). 4. Restore 24 Vac power to CP-8161-333. 5. Verify the calibration using the calibration procedure shown on page 8. Caution: Plug-in board (BDZD-961-1) cannot be used in TP-8124/TP-8125 dual room controllers. On October 1st, 2009, TAC became the Buildings business of its parent company Schneider Electric. This document reflects the visual identity of Schneider Electric, however there remains references to TAC as a corporate brand in the body copy. As each document is updated, the body copy will be changed to reflect appropriate corporate brand changes. Copyright 2010, Schneider Electric Schneider Electric All brand names, trademarks and registered 1354 Clifford Avenue trademarks are the property of their respective P.O. Box 2940 owners. Information contained within this Loves Park, IL 61132-2940 document is subject to change without notice. www.schneider-electric.com/buildings F-18096-10
Frequently asked questions
How does Industrial Trading differ from its competitors?

Is there a warranty for the CP-8161-333?

Which carrier will Industrial Trading use to ship my parts?

Can I buy parts from Industrial Trading if I am outside the USA?

Which payment methods does Industrial Trading accept?

What they say about us
FANTASTIC RESOURCE
One of our top priorities is maintaining our business with precision, and we are constantly looking for affiliates that can help us achieve our goal. With the aid of GID Industrial, our obsolete product management has never been more efficient. They have been a great resource to our company, and have quickly become a go-to supplier on our list!
Bucher Emhart Glass
EXCELLENT SERVICE
With our strict fundamentals and high expectations, we were surprised when we came across GID Industrial and their competitive pricing. When we approached them with our issue, they were incredibly confident in being able to provide us with a seamless solution at the best price for us. GID Industrial quickly understood our needs and provided us with excellent service, as well as fully tested product to ensure what we received would be the right fit for our company.
Fuji
HARD TO FIND A BETTER PROVIDER
Our company provides services to aid in the manufacture of technological products, such as semiconductors and flat panel displays, and often searching for distributors of obsolete product we require can waste time and money. Finding GID Industrial proved to be a great asset to our company, with cost effective solutions and superior knowledge on all of their materials, it’d be hard to find a better provider of obsolete or hard to find products.
Applied Materials
CONSISTENTLY DELIVERS QUALITY SOLUTIONS
Over the years, the equipment used in our company becomes discontinued, but they’re still of great use to us and our customers. Once these products are no longer available through the manufacturer, finding a reliable, quick supplier is a necessity, and luckily for us, GID Industrial has provided the most trustworthy, quality solutions to our obsolete component needs.
Nidec Vamco
TERRIFIC RESOURCE
This company has been a terrific help to us (I work for Trican Well Service) in sourcing the Micron Ram Memory we needed for our Siemens computers. Great service! And great pricing! I know when the product is shipping and when it will arrive, all the way through the ordering process.
Trican Well Service
GO TO SOURCE
When I can't find an obsolete part, I first call GID and they'll come up with my parts every time. Great customer service and follow up as well. Scott emails me from time to time to touch base and see if we're having trouble finding something.....which is often with our 25 yr old equipment.
ConAgra Foods