PACIFIC SCIENTIFIC 6435
Datasheet
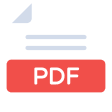
Pacific_Scientific_6435_Oscillator-Microstepping_Drive_Package_datasheet1-1924988474.pdf
201 KiB
Extracted Text
Pacific Scientific Model 6435 Oscillator/Microstepping Drive Package FEATURES � Economical Position/Speed Control � Accel and Decel Control � Two selectable run speeds � Separate (latched) Run/Stop Inputs for clutch brake applications � Internal and/or External Command � Off line 120/240 Vac 60/50 Hz � Patented 4-phase Bipolar Chopper Drive for superior current regulation and low ripple current � Output current adjustable from 0.625 A to5Arms with 3 position DIP switch � Microstepping for smooth operation and increased resolution � Wide Speed Range � Stable over operating temperature range (–1%) � Switch selectable Step Size and Current � Patented Digital Electronic Damping reduces instability at mid-speed ranges � Adjustable Idle Current Reduction � External Pulse Output � Drive Fault protection: - Line-to-line and line-to-neutral shorts � Power supply fault protection: PRODUCT DESCRIPTION - Over temperature The Pacific Scientific 6435 is an economical, high performance - Short circuit microstepping drive with an integral oscillator. The package - Under voltage includes the highly popular 6410 drive and thus incorporates its � Output for 2nd Axis many valuable features such as high resolution microstepping (200 to 51,200 steps per revolution) for smooth operation - 66 Vdc–3 volts available via three position through resonance regions, mid-range Digital Electronic plug-in connector (J6) to power additional axis (total Damping, single supply operation, output current adjustment, power available for internal and external axis = 300 W) and idle current reduction. � Small size - 6.25" x 2.25" x 12.50" The 6435 contains a stable, wide range voltage controlled � UL and CSA recognition pending oscillator (VCO) which provides step pulses to the drive card. � CE conformance pending There are two frequency ranges, customer selectable by a jumper. The final runspeed is controlled by the following: - Low/High speed select Input or APPLICATIONS - on-board multi-turn potentiometers or - external customer potentiometer or � Clutch Brake Replacement - customer supplied -10 Vdc to +10 Vdc analog voltage � Labeling Machines The relationship between the VCO pulse frequency and the � Packaging/Specialty Machinery motor shaft rpm is a function of the step size selected. � Smart Conveyor Systems Direction can be controlled by any of the following: � Semiconductor Wafer Polishing - Polarity of the Analog Input or � Constant Speed Applications - Plug-On jumpers or - Optically isolated discrete input 903-643501-00-Rev76435DataSheet1 SPECIFICATIONS Input Power Voltage 120 - 240 Vac 60-50 Hz (switch selectable) Line Current At full (300W) load 240 Vac, 3.7 A RMS 120 Vac, 4.7 A RMS Output motor phase current 5 A rms max. 5 A peak full step 7.1 A peak microstepping Adjustable from 0.625 to 5 A rms in 0.625 amp increments 66 Vdc Output for 2nd axis (J6) 66–3 volts. Total power (internal + external) = 300W –10% RUN SPEED Control (Analog Input) Analog Input Range–10 Vdc (Also controllable with internal or external pots) Analog Input Impedance 20 KW(differential amp) High Frequency Range RUN SPEED Control 0 KHz to 500 KHz (8 KHz to 500 KHz with MIN SPEED Enabled) LOW SPEED Control 0 KHz to 370 KHz (8 KHz to 370 KHz with MIN SPEED Enabled) Low Frequency Range RUN SPEED Control 0 KHz to 250 KHz (4 KHz to 250 KHz with MIN SPEED Enabled) LOW SPEED Control 0 KHz to 180 KHz (4 KHz to 180 KHz with MIN SPEED Enabled) RUN SPEED/LOW SPEED–1% of full scale (typical) Stability Over Temp. /Range ACCEL RAMP (exponential) accel pot fully CW 0.4 sec (single time constant) accel pot fully CCW 0.4 msec (single time constant) DECEL RAMP (linear) decel pot fully CW 1.4 sec decel pot fully CCW 6.0 msec MIN SPEED 4 KHz Maximum (high frequency range) 2 KHz Maximum (low frequency range) Steps below this frequency are inhibited to insure no movement at end of decel ramp. This functionality can be disabled by inserting jumper E5. Note: Motor rpm = 0.3 * Freq. (Hz)/step size. For example: If frequency = 500,000 Hz and step size = 125, rpm = 1200. Signal Input Requirements Input Min. Input Current - Opto ON Max. Input Current Max. Reverse Voltage J4-19, J4-7 Low Speed 3.0 ma 4.5 ma 5 volts J4-22, J4-10 Direction 3.0 ma 4.5 ma 5 volts J4-23, J4-11 Enable 3.0 ma 4.5 ma 5 volts J4-20, J4-8 Run 3.0 ma 4.5 ma 5 volts J4-21, J4-9 Stop 3.0 ma 4.5 ma 5 volts 26435DataSheet903-643501-00-Rev7 Note: Factory default settings are in bold OSCILLATOR BOARD SETTINGS Oscillator Board SW1 JMPR 25 14 J4 Side View 6415 1 E6 E8 E7 E2 - Frequency Range E3 E1 6 U12 IN LOW FREQUENCY 1 1 OUT HIGH FREQUENCY U2 U9 E2 U1 U3 U16 E4 - RUN/STOP Control U10 U7 U8 IN SEPARATE INPUTS OUT SINGLE INPUT E4 E5 - MIN SPEED Frequency U15 U13 E5 IN DISABLED U14 OUT ENABLED Control Source E6 E7 E8 DIR Opto Analog In Rotation E1 E3 - Velocity Control Mode DIR+/DIR- OUT OUT OUT Driven -------- CCW Internal RUN SPEED 1-2 IN 1-2 IN OUT OUT OUT Not Driven ------- CW Potentiometer Jumpers IN IN OUT Driven ------- CCW External Potentiometer 3-4 IN N/A OUT OUT OUT Not Driven ------- CW Analog In IN OUT IN Driven Negative CCW External Analog Input 5-6 IN 1-2 IN IN OUT IN Not Driven Positive CW External Analog Input 1-2 IN 3-4 IN scaled by internal RUN SPEED potentiometer DRIVE BOARD SETTINGS Oscillator Board SW1 JMPR FACTORY DEFAULTS: 5.0 AMPS RMS Drive Board STEPSIZE 1/25 Side View IDLE CURRENT REDUCTION ENABLED (0.1 SEC) JUMPERS 3-4, & 7-8 DIGITAL ELECTRONIC INSTALLED AT FACTORY DAMPING CONTROL ENABLED DO NOT CHANGE DRIVER ENABLED UNLESS ENABLE OPTO DRIVEN OPEN PC CARD EDGE OPEN S1 SIDE VIEW FACTORY DEFAULT POSITIONS SHOWN 1 2 3 4 5 6 7 8 SW1 POSITION MOTOR SW1 POSITION STEP SIZE CURRENT DEC JMPR IN 67 8 AMPS RMS 12 3 5.0 CLOSED CLOSED CLOSED FULL CLOSED CLOSED CLOSED 4.375 CLOSED CLOSED OPEN CLOSED CLOSED OPEN HALF CLOSED OPEN CLOSED 3.750 CLOSED OPEN CLOSED 1/5 3.125 CLOSED OPEN OPEN CLOSED OPEN OPEN 1/10 OPEN CLOSED CLOSED 2.5 1.875 OPEN CLOSED CLOSED 1/25 OPEN CLOSED OPEN 1.25 OPEN OPEN CLOSED OPEN CLOSED OPEN 1/50 0.625 OPEN OPEN OPEN OPEN OPEN CLOSED 1/125 OPEN OPEN OPEN 1/250 SWI IDLE-T SW1 IDLE CURRENT POSITION 4 DIGITAL ELECTRONIC DAMPING JUMPER POSITION 5 REDUCTION IN CLOSED DISABLED CLOSED DISABLED IN OPEN 0.1 SEC DELAY OPEN ENABLED 903-643501-00-Rev76435DataSheet3 J6 S1 LED1 RUN SPEED ACCEL RAMP DECEL RAMP LOW SPEED 1 7 USER'S 6435 CONTROL STEPPER J4 I/O COMMAND AND ELECTRONICS DRIVE MONITOR SIGNALS 19 LOW_SPD +5 Vdc TLP 621 2.21K TTL RUN+/RUN-, STOP+/STOP- LOW_SPD 7 1K Separate Latched Inputs (E4 jumper installed - Default) RUN 20 With the E4 jumper installed, the TLP 2601 2.21K RUN/STOP (Clutch brake) mode of the TTL 1K RUN 8 6435 is controlled by two separate optically isolated inputs. When the RUN opto is driven momentarily, the RUN/STOP latch is placed in the RUN STOP 21 TLP 621 state and the oscillator frequency ramps 2.21K TTL to the selected speed at a rate controlled STOP 9 1K by the ACCEL potentiometer. When the STOP opto is driven momentarily, the RUN/STOP latch is placed in the STOP state and the oscillator frequency ramps DIR 22 TLP 621 to zero frequency at a rate controlled by 2.21K TTL 1K the DECEL potentiometer. DIR 10 The RUN/STOP latch is designed to be in the STOP state after applying power 23 ENABLE to the 6435 to insure that motion does TLP 621 2.21K not occur unintentionally. TTL ENABLE 11 1K Single Input (E4 jumper removed) MOTION BEGINS If the E4 jumper is removed, the 50ms MIN WITHIN 50ms RUN/STOP mode of the drive is RUN- controlled directly from the RUN input. INPUT SETUP TIME When the RUN opto is driven, the 50ms MIN oscillator frequency ramps to the DIRECTION selected speed at a rate controlled by the INPUT ACCEL potentiometer. When the RUN opto is off, the oscillator frequency DIRECTION DATA MUST BE STABLE ramps to zero frequency at a rate OVER THIS INTERVAL controlled by the DECEL potentiometer. Figure 1 - 6435 Digital Interface Circuitry Enable The drive is enabled unless the Enable opto is driven. 6435 J4-2 +8V_REF_OUT External Step Pulse The step pulse output from the VCO is available on J4-12, J4-13, J4-24, and STEP J4-25. This can be connected to up to IN STEP OUT four additional 6410 drives. J4-12, 6410 13, 24, VCO 25 OTHER 6410s Figure 2 - External Step Pulse 46435DataSheet903-643501-00-Rev7 J4 6415 LOW_SPD+/LOW_SPD- 15 +8V_REF_OUT This optically isolated input selects the source of the analog speed command. 10K 3 With the LOW_SPD opto on (J4-7 USER'S EXTERNAL POT POT (Z > 1 MEG OHM) in Low), the analog speed command is derived from the LOW SPEED potentiometer. 16 GND With the LOW_SPD opto off (J4-7 High), the analog speed command is derived from one of the following Figure 3 - External potentiometer sources depending upon the E1 and E3 jumper configurations: J4 6415 16.2K � Internal RUN SPEED potentiometer (E1 1-2 and E3 1-2 installed - Default) 10K 10K 6 ANALOG_IN- 0.01UF � External potentiometer (E1 3-4 installed) USER'S SIGNAL � External analog input SOURCE (E1 5-6 and E3 1-2 installed) 10K 10K ANALOG_IN+ 18 � External analog input scaled (fine 16.2K 0.01UF tuned) by internal RUN SPEED potentiometer (E1 1-2 and E3 3-4 installed) Figure 4 - Analog Input The LOW_SPD input can changed at any time. The speed (oscillator frequency) will not change instantly, but will ramp to the newly selected speed at a rate controlled by the ACCEL or DECEL potentiometers depending upon DECEL RUN SPEED RAMP whether the speed (magnitude) is ACCEL RAMP LOW SPEED increasing or decreasing. MIN SPEED Figure 6 shows the velocity wave form 0 in a typical application where the high RUN speed is selected when the RUN input is pulsed and latched. Near the end of the 50 mSEC MIN motion profile, low speed is selected to 0 insure a short and precise stopping distance when the STOP input is pulsed. LOW_SPD LOW 0 ADJUSTMENT STOP POTENTIOMETERS 50 mSEC MIN 0 Figures 5 and 6 show the typical velocity Figure5-TypicalVelocityProfilewithSeparateRUN/STOP (pulse frequency) profile in response to a separate RUN/STOP or with a singleandRUN/LOWCommandSignals RUN/STOP and RUN/LOW commands. Adjustments for RUN SPEED, LOW SPEED, ACCEL RAMP, and DECEL RUN SPEED RAMP are made with 4 multi-turn ACCEL DECEL RAMP RAMP potentiometers. MIN SPEED LOW SPEED is typically set lower than 0 RUN SPEED to allow for accurate stopping. It can also be used as a STOP STOP second RUN SPEED. ACCEL RAMP is RUN typically set to minimize time to reach 0 RUN SPEED without allowing the motor to stall. The DECEL RAMP isFigure6-TypicalVelocityProfilewith a Single RUN/STOP Command Signal linear and stable, allowing a more precise, repeatable stopping position. 903-643501-00-Rev76435DataSheet5 CONNECTION DIAGRAM J4 J12 STEP_OUT 13 1 STEP_OUT 25 2 STEP_OUT 12 3 STEP_OUT 24 4 ENABLE- 11 5 NOT USED ENABLE+ 23 6 DIR- 10 7 DIR+ 22 8 6435 STOP- 9 9 STOP+ 21 OSCILLATOR RUN- 8 J6 DRIVE RUN+ 20 - LOW_SPD- 1 7 66 VDC OUT + LOW_SPD+ 19 2 ANALOG_INPUT- 6 3 ANALOG_INPUT+ 18 GNDA 5 J3 GNDA 17 Phase A GNDA 4 1 GNDA 16 Phase A 2 EXTERNAL_POT 3 Phase B +8V_REF_OUT 15 3 2Phase +8V_REF_OUT Stepper 2 Phase B 4 Motor +8V_REF_OUT 14 VCO_INPUT_MON Case GND 1 5 J1 1 120 - 240 Vac 60 /50 Hz 2 Power 3 Figure 7 - 6435 Connection Diagram 66435DataSheet903-643501-00-Rev7 User's Control Electronics LED1 RUN SPEED ACCEL RAMP DECEL RAMP LOW SPEED 230 115 1.12 MOUNTING DIAGRAM [28.45mm] J4 DISCRETE I/O 13 N/A 1 J6 66Vout LOW SPEED J3 MOTOR A DECEL A ACCEL B B RUN SPEED L1 J1 POWER L2 120 / 240 VAC 12.50 [317.50mm] 11.61 [294.89mm] POWER ON FAULT 10.75 [273.05mm] DIGITAL TM ELECTRONIC DAMPING 6435 0.50 0.30 6.25 [12.70mm] [7.62mm] [158.75mm] 1.24 [31.50mm] 2.25 [57.15mm] Figure 8 - 6435 Mounting Dimensions AC SWITCH SETTINGS Transformer The AC switch is preset at the factory in Remove screws the 240 Vac position. The AC switch is four places easily accessible by opening the cover. First, make certain the power connections have been removed. Rest the unit on its side as shown. Remove the four screws. Select appropriate Oscillator board setting. Replace cover and mounting screws. Do NOT over tighten mounting AC switch (SW1) screws. (5.0 in-lbs max) Note: Connecting 240 (230) Vac with switch in 120 (115) position will permanently damage the drive. Power board 903-643501-00-Rev76435DataSheet7 25 14 J4 1 E6 E8 E7 E3 E1 6 1 1 E2 E4 E5 66 VDC OUTPUT CONNECTOR J6 The 6435 package has an external 66 Vdc connector (J6) designed to power an 3 additional drive. The total power + 2 J2 6410 available for both the internal and - external drives is 66 Vdc @ 4.6 Amps or 1 approximately 300 Watts. If the two drives are running simultaneously and require more than 4.6 Amps, the voltage will begin to cut back. The power supply has a low voltage protection circuit that will fault the drive if the dc supply dips below 55 Vdc. 3 + A twisted pair plus ground cable 2 J2 6410 utilizing 16, 18, or 20 gauge wire is - - 1 recommended to connect the remote + connector to the external drive. A 470 J6 6435 mF 100 Vdc aluminum electrolytic capacitor, rated for 2A ripple current or greater, must be installed at the additional drive if the cable length is over 3 feet. GETTING STARTED Perform this initial power up with the motor shaft disconnected from the load. Improper wiring could result in undesired motion. 1. Connect the motor leads and power supply wires to the 6435 Oscillator Package connectors as shown. Note: J12 on the lower board is not used. 2. Wire the control signals for the independent RUN, STOP and DIRECTION control into connector J4 as shown in Figure 1. 3. Pull the RUN signal Low (J4-8) and the motor will ramp up to speed. Pull the STOP signal low (J4-9) and the motor decelerates to a stop. When the DIRECTION signal is pulled low (J4-10) the motor will run in the CCW direction, looking at the motor shaft. If the desired rotation for a low signal is CW, swap the connections of the motor leads on pins J3-1 and J3-2. Note: Remove power from the drive before swapping the leads. 4. If the motor emits a high frequency noise but the shaft is not rotating, stop the motor. Lower the RUN SPEED by turning the RUN SPEED potentiometer CCW. Increase the ACCEL RAMP by turning the ACCEL RAMP potentiometer CW. 5. After successfully establishing motion, the system can be powered down and connected to a load. 86435DataSheet903-643501-00-Rev7 TROUBLESHOOTING Power Board SYMPTOM POSSIBLE CAUSE ACTION Motor does not turn 120/240 Vac switch in 240 Turn power off, correct switch position. LEDs ON (green position, input from 120 Vac and/or red) AC Input line low Increase Input AC to spec. Dead short or overload across Remove short or reduce load. external 66 Vdc output connector (J6). Over temperature Check ambient temperature or internal fan malfunction/blockage. Bad load connection Check load connection. Check J6 Vdc output with a voltmeter and ensure output voltage is 66V –3V. 1. If output voltage > 70 Vdc and < 78 Vdc add a load and ensure Vdc is » 66Vdc. 2. If output voltage > 78 Vdc, return 6430 to factory for service. Drive board fault See table on following page. Internal failure. Return to factory for service. Motor does not turn, Check AC input Use proper input. LEDs OFF 240 Vac applied and switch in Return to factory for service. 120 Vac position. Motor runs for a Over temperature. Reduce load. while and stops, both Check for excessive ambient temperature. LEDs come on Check for internal fan malfunction/blockage. Motor turns on and 120 Vac applied and switch in Correct switch position. off on its own and 240 Vac position red LED keeps Over load. Reduce load. flashing AC input line low. Check input AC line voltage for low line. OR Drive Board Fault. See table below on following page. Motor stops after Internal failure. Return to factory for service. running once. Note: If the power supply is on the verge of an under-voltage fault, you will notice the following during normal operation. Red LED Flashing, but NO FAULT SYMPTOM POSSIBLE CAUSE Motor runs fine, red Load is too high, LED flashes AND/OR Accel/Decel are too high, AND/OR Run Speed is too high Although no action is required, the symptom above may be eliminated by reducing the load, accel/decel and/or run speed. 903-643501-00-Rev76435DataSheet9 Drive Board SYMPTOM CORRECTIVE ACTION Motor produces no torque, Disconnect AC power then disconnect the motor cable and cycle the J1 power supply Meter at J12-4 and J12-9 reads Off and On. If the meter reads low, check motor cable and motor for shorts across high. the windings or between the windings and the motor case. Motor produces no torque, Verify that DIP Switch S1 position 6, 7, and 8 (current select) are set correctly. Meter at J12-4 and J12-9 reads low. Re-check that the motor cable is wired correctly and properly plugged into the drive. Motor produces torque but Make sure that the STEP input is switching and meets specified electrical and timing does not turn. requirements. Motor rotates in the wrong Check polarity of the DIRECTION input. Also, check that the DIRECTION input direction satisfies the specified electrical and timing requirements. Reverse the A and A motor phases. Motor does not reach expected Check that the step size setting of the drive is the same as the step size setting of the position indexer. Verify that the motor does not stall. If it does: 1. Re-check sizing calculations. Be sure that the power supply voltage is high enough for the required torque vs. speed curve. 2. Use a finer step size to avoid low-speed resonance problems. 3. Enable Digital Electronic Damping control. (S1 position 4 OFF). Check that the STEP and DIRECTION Inputs satisfy all electrical and timing requirements. 106435DataSheet903-643501-00-Rev7 Oscillator Board SYMPTOM CORRECTIVE ACTION Motor produces no torque Disconnect the AC power. Disconnect motor cable and cycle the J1 power supply Off and On. Check the step output and VCO input monitor point. Also, check motor cable and motor for shorts across the windings or between the windings and the motor case. Verify that DIP Switch S1 position 6, 7, and 8 (current select) are set correctly. Re-check that the motor cable is wired correctly and properly plugged into the drive. Motor produces torque but Make sure that the STEP output is switching. does not turn. Motor rotates in the wrong Check polarity of the DIRECTION input. Also, verify that the direction selection jumpers direction. (E6, E7, E8) are set correctly. Reverse the A and A motor phases. Motor does not reach Check that the step size setting of the drive and speed potentiometer are set correctly. expected position. Verify that the motor does not stall. If it does: 1. Re-check sizing calculations. Be sure that the power supply voltage is high enough for the required torque vs. speed curve. 2. Use a finer step size to avoid low-speed resonance problems. 3. Enable Digital Electronic Damping (S1 position 4 OFF). Drive is disabled. 1. Turn the bus power off. 2. Disconnect the motor winding from the drive. 3. Turn the bus power back to on. Check that the +8V reference output (+8V_REF_OUT) is within specifications. 4. Remove any external connections to the enable input opto (ENABLE). 5. Reapply the power. If still disabled, Drive has an internal short. Motor produces torque, but 1. No Step pulses out - Check that there is a final speed command voltage at the VCO does not run. monitor test point (VCO_INPUT_MON) and the step pulses output (STEP_OUT) is switching. Also verify that E1 and E3 jumpers are set correctly. 2. Loss of phase current in one winding. Check phase current in both phases by placing an ammeter in series with each winding. If not present, check for open circuit in motor phase winding by measuring resistance. 3. One motor phase not wired correctly at stepping motor. Check stepping motor wiring. 4. Step pulses output (STEP_OUT) is too high. Lower step pulses output by adjusting Run Speed and Accel/Decel Potentiometers. Also check to make sure that the step size and frequency range jumper (E2) are set correctly. Motor misses steps. Incorrect run speed or low speed. Adjust run speed potentiometer or low speed potentiometer. Incorrect accel ramp time or decel time. Adjust accel potentiometer or decel potentiometer. 903-643501-00-Rev76435DataSheet11 PERFORMANCE - 6400 SERIES CONTROLS Motorswillperformasshownwithoutthewindingtemperatureexceedingariseof90C.Whenthemotorisoperatedunmounted (withoutheatsink)inanambienttemperatureofupto40C.Thecurvesdonotreflectsystemsresonancepoints,whichwillvarywith motorcouplingandsystemsparameters. Inadditiontothoseshownbelow,PacificScientificoffersawiderangeofothermotorwindingstomeetspecificperformance requirements. Torque/Speed Curves - Recommended Motors for 5.0 A operation (3"MOTOR-TWO ROTOR STACK) (3"MOTOR-THREE ROTOR STACKS) (3"MOTOR-ONE ROTOR STACK) E32NX-HTLNN-NS50 E33NX-HTLNK-NS50 E31NX-HTLNN-NS50 E32NX-HPLNN-NS50 E33NX-HPLNK-NS50 5.0A/65V PER PHASE 5.0A/65V PER PHASE 5.0A/65V PER PHASE SPEED (RPM) SPEED (RPM) SPEED (RPM) 0 600 1200 1800 2400 3000 300 2.12 0 600 1200 1800 2400 3000 0 600 1200 1800 2400 3000 600 4.24 900 6.36 T 250 1.77 T 750 5.30 500 3.53 T 200 1.41 400 2.82 600 4.24 150 1.06 450 3.18 300 2.12 P 100 0.71 300 2.12 200 1.41 P 50 0.35 100 0.71 150 1.06 0 0.00 0 0.00 0 0.00 0 2000 4000 6000 8000 10000 0 2000 4000 6000 8000 10000 0 2000 4000 6000 8000 10000 SPEED (FULL STEP/SEC) SPEED (FULL STEP/SEC) SPEED (FULL STEP/SEC) (3"MOTOR-FOUR ROTOR STACKS) (4" MOTOR-ONE ROTOR STACK) E34HX-HTLNK-NS50 E41HX-HTLNK-NS50 E32HX-HPLNK-NS50 5.0A/65V PER PHASE 5.0A/65V PER PHASE SPEED (RPM) SPEED (RPM) 0 300 600 900 1200 1500 1800 0 300 600 900 1200 1500 1800 1200 8.47 1200 8.47 1000 7.06 T 1000 7.06 T 800 5.65 800 5.65 600 4.24 600 4.24 400 2.82 400 2.82 P 200 1.41 200 1.41 0 0.00 0 0.00 0 1000 2000 3000 4000 5000 6000 0 1000 2000 3000 4000 5000 6000 SPEED (FULL STEP/SEC) SPEED (FULL STEP/SEC) Torque/Speed Curves - Recommended Motors for 5.0 A operation (3"MOTOR-TWO ROTOR STACK) (3"MOTOR-ONE ROTOR STACK) (2"MOTOR-TWO ROTOR STACKS) E31NX-LTLNN-NS50 E32NX-LTLNN-NS50 E22NX-LTLNN-NS50 E32NX-LPLNN-NS50 E31NX-LPLNN-NS50 E22NX-LPLNN-NS50 2.5A/65V PER PHASE 2.5A/65V PER PHASE 2.5A/65V PER PHASE SPEED (RPM) SPEED (RPM) 0 600 1200 1800 2400 3000 SPEED (RPM) 0 600 1200 1800 2400 3000 300 2.12 600 4.24 0 600 1200 1800 2400 3000 T 200 1.41 T T 250 1.77 500 3.53 160 1.13 200 1.41 400 2.83 120 0.85 P 150 1.06 300 2.12 P P 80 0.56 100 0.71 200 1.41 40 0.28 50 0.35 100 0.71 0 0.00 0 2000 4000 6000 8000 10000 0 0.00 0 0.00 0 2000 4000 6000 8000 10000 0 2000 4000 6000 8000 10000 SPEED (FULL STEP/SEC) SPEED (FULL STEP/SEC) SPEED (FULL STEP/SEC) 126435DataSheet903-643501-00-Rev7 TORQUE (OZ-IN) TORQUE (OZ-IN) TORQUE (OZ-IN) TORQUE (N-m) TORQUE (N-m) TORQUE (OZ-IN) TORQUE (OZ-IN) TORQUE (N-m) TORQUE (OZ-IN) TORQUE (N-m) TORQUE (N-m) TORQUE (OZ-IN) TORQUE (OZ-IN) TORQUE (N-m) TORQUE (N-m) TORQUE (N-m)
Frequently asked questions
How does Industrial Trading differ from its competitors?

Is there a warranty for the 6435?

Which carrier will Industrial Trading use to ship my parts?

Can I buy parts from Industrial Trading if I am outside the USA?

Which payment methods does Industrial Trading accept?

What they say about us
FANTASTIC RESOURCE
One of our top priorities is maintaining our business with precision, and we are constantly looking for affiliates that can help us achieve our goal. With the aid of GID Industrial, our obsolete product management has never been more efficient. They have been a great resource to our company, and have quickly become a go-to supplier on our list!
Bucher Emhart Glass
EXCELLENT SERVICE
With our strict fundamentals and high expectations, we were surprised when we came across GID Industrial and their competitive pricing. When we approached them with our issue, they were incredibly confident in being able to provide us with a seamless solution at the best price for us. GID Industrial quickly understood our needs and provided us with excellent service, as well as fully tested product to ensure what we received would be the right fit for our company.
Fuji
HARD TO FIND A BETTER PROVIDER
Our company provides services to aid in the manufacture of technological products, such as semiconductors and flat panel displays, and often searching for distributors of obsolete product we require can waste time and money. Finding GID Industrial proved to be a great asset to our company, with cost effective solutions and superior knowledge on all of their materials, it’d be hard to find a better provider of obsolete or hard to find products.
Applied Materials
CONSISTENTLY DELIVERS QUALITY SOLUTIONS
Over the years, the equipment used in our company becomes discontinued, but they’re still of great use to us and our customers. Once these products are no longer available through the manufacturer, finding a reliable, quick supplier is a necessity, and luckily for us, GID Industrial has provided the most trustworthy, quality solutions to our obsolete component needs.
Nidec Vamco
TERRIFIC RESOURCE
This company has been a terrific help to us (I work for Trican Well Service) in sourcing the Micron Ram Memory we needed for our Siemens computers. Great service! And great pricing! I know when the product is shipping and when it will arrive, all the way through the ordering process.
Trican Well Service
GO TO SOURCE
When I can't find an obsolete part, I first call GID and they'll come up with my parts every time. Great customer service and follow up as well. Scott emails me from time to time to touch base and see if we're having trouble finding something.....which is often with our 25 yr old equipment.
ConAgra Foods