ALLEN-BRADLEY 1785-PFBMGR
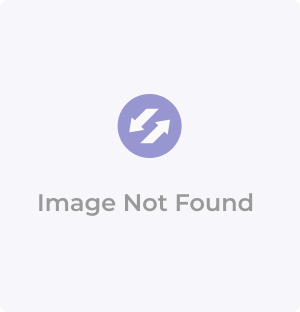
Description
Allen Bradley 1785-PFBMGR Software - PROFIBUS MANAGER SOFTWARE
Part Number
1785-PFBMGR
Price
Request Quote
Manufacturer
ALLEN-BRADLEY
Lead Time
Request Quote
Category
Software
Features
- and slave configuration/parameter.
- Communication Relationship List (CRL), Object Dictionary (OD), polling cycle timings
- Create FMS projects and create DP projects
- Import and export configurations
- Manage projects easily
- Monitor applications
- Set up communication parameters for your applications: Fieldbus Data Link (FDL),
Datasheet
Extracted Text
AllenBradley
SLC 500�
User
PROFIBUS DP
Slave/Adapter
Manual
Module
(Cat. No. 1747APB)
Important User Because of the variety of uses for the products described in this
publication, those responsible for the application and use of this
Information
control equipment must satisfy themselves that all necessary steps
have been taken to assure that each application and use meets all
performance and safety requirements, including any applicable laws,
regulations, codes, and standards.
The illustrations, charts, sample programs and layout examples
shown in this guide are intended solely for purposes of example.
Since there are many variables and requirements associated with any
particular installation, Allen-Bradley does not assume responsibility
or liability (to include intellectual property liability) for actual use
based on the examples shown in this publication.
Allen-Bradley publication SGI-1.1, Safety Guidelines for the
Application, Installation, and Maintenance of Solid-State Control
(available from your local Allen-Bradley office), describes some
important differences between solid-state equipment and
electromechanical devices that should be taken into consideration
when applying products such as those described in this publication.
Reproduction of the contents of this copyrighted publication, in
whole or in part, without written permission of Allen-Bradley
Company, Inc., is prohibited.
Throughout this manual, we use notes to make you aware of safety
considerations:
ATTENTION: Identifies information about practices
or circumstances that can lead to personal injury or
death, property damage, or economic loss.
!
Attention statements help you to:
• identify a hazard
• avoid the hazard
• recognize the consequences
Important: Identifies information that is critical for successful
application and understanding of the product.
SLC, SLC 500, IMC, PanelView, and PanelBuilder are trademarks of Allen-Bradley Company, Inc.
PLC-5 is a registered trademark of the Allen-Bradley Company, Inc.
Windows is a trademark, and Microsoft is a registered trademark of the Microsoft Corporation.
Shading is 25% black. Font is Helvetica Narrow 14 (or equivalent). Each tab is
2.0” long. The PROFIBUS DP Network tab should start 2.50” down from top of
page. Thus, the SLC System tab will be 2.50” up from bottom of page.
The tabs shown below illustrate how the finished tabs should look.
PROFIBUS DP Network Chapters 2, 3, and 4.
1747APB Module Chapters 5, 6, 7, 8, and 9.
Chapters 10 and 11.
SLC System
Table of Contents
Preface . . . . . . . . . . . . . . . . . . . . . . . . . . . . . . . . . . . P-1
Who Should Use this Manual . . . . . . . . . . . . . . . . . . . . . . . P-1
Purpose of this Manual . . . . . . . . . . . . . . . . . . . . . . . . . . . . P-1
Contents of this Manual . . . . . . . . . . . . . . . . . . . . . . . . . P-2
Related Documentation . . . . . . . . . . . . . . . . . . . . . . . . . P-3
Common Techniques Used in this Manual . . . . . . . . . . . . . . P-4
AllenBradley Support . . . . . . . . . . . . . . . . . . . . . . . . . . . . P-4
Local Product Support . . . . . . . . . . . . . . . . . . . . . . . . . . P-4
Technical Product Assistance . . . . . . . . . . . . . . . . . . . . . P-4
Quick Start for Experienced Users . . . . . . . . . . . . . . . 1-1
Required Tools and Equipment . . . . . . . . . . . . . . . . . . . . . . 1-1
Procedures . . . . . . . . . . . . . . . . . . . . . . . . . . . . . . . . . . . . 1-2
PROFIBUS DP Overview . . . . . . . . . . . . . . . . . . . . . . 2-1
Introduction to PROFIBUS DP . . . . . . . . . . . . . . . . . . . . . . . 2-1
Communication Between DP Masters and DP Slaves . . . . . . 2-1
How Data is Exchanged on the Network . . . . . . . . . . . . . . 2-2
Defining the DP Slave Data . . . . . . . . . . . . . . . . . . . . . . . 2-2
PROFIBUS DP Products Available from AllenBradley . . . . . . 2-3
For more information . . . . . . . . . . . . . . . . . . . . . . . . . . . 2-3
The 1785PFB/B Coprocessor . . . . . . . . . . . . . . . . . . . . 2-4
Local Station Manager Software . . . . . . . . . . . . . . . . . 2-4
PROFIBUS Manager Software . . . . . . . . . . . . . . . . . . 2-5
The 1747APB Module . . . . . . . . . . . . . . . . . . . . . . . . . . 2-5
The 1794APB Flex I/O Adapter . . . . . . . . . . . . . . . . . . . 2-6
PanelViewt Operator Terminal . . . . . . . . . . . . . . . . . . . . . 2-6
PanelBuildert Software . . . . . . . . . . . . . . . . . . . . . . . . 2-6
Connecting to the PROFIBUS DP Network . . . . . . . . . 3-1
Selecting the Line Type You Should Use . . . . . . . . . . . . . . . 3-1
Connecting to the Network Using Line Type A . . . . . . . . . . . . 3-2
Equipment Needed for Line Type A . . . . . . . . . . . . . . . . . 3-2
Cables . . . . . . . . . . . . . . . . . . . . . . . . . . . . . . . . . . . 3-2
Termination Blocks . . . . . . . . . . . . . . . . . . . . . . . . . . . 3-2
Connector . . . . . . . . . . . . . . . . . . . . . . . . . . . . . . . . . 3-2
Connecting Line Type A Cabling . . . . . . . . . . . . . . . . . . . 3-3
Connecting to the Network Using Line Type B . . . . . . . . . . . . 3-4
Equipment Needed for Line Type B . . . . . . . . . . . . . . . . . 3-4
Guidelines for Drop Cables . . . . . . . . . . . . . . . . . . . . . 3-5
Connecting Line Type B Cabling . . . . . . . . . . . . . . . . . . . 3-5
ii Table of Contents
Configuring the PROFIBUS DP Master . . . . . . . . . . . . 4-1
Entering Slave Data Using the Device Data Base . . . . . . . . . 4-1
Entering Configuration Data . . . . . . . . . . . . . . . . . . . . . . . . 4-2
Understanding Slot Numbering . . . . . . . . . . . . . . . . . . . . 4-2
Mapping Between Logical Modules and Physical Modules . 4-3
Creating the Configuration Data . . . . . . . . . . . . . . . . . . . . 4-3
Configuration Data Example . . . . . . . . . . . . . . . . . . . . 4-5
Entering Parameter Data . . . . . . . . . . . . . . . . . . . . . . . . . . 4-6
1747APB Module Overview . . . . . . . . . . . . . . . . . . . . 5-1
1747APB Module . . . . . . . . . . . . . . . . . . . . . . . . . . . . . . . 5-1
Compatible Modules . . . . . . . . . . . . . . . . . . . . . . . . . . . . . . 5-2
1747APB Module Features . . . . . . . . . . . . . . . . . . . . . . . . 5-3
Hardware Features . . . . . . . . . . . . . . . . . . . . . . . . . . . . 5-3
Diagnostic Display and LEDs . . . . . . . . . . . . . . . . . . . 5-4
DIP Switch . . . . . . . . . . . . . . . . . . . . . . . . . . . . . . . . . 5-4
PROFIBUS DP Station Address Switch . . . . . . . . . . . . 5-5
Labels . . . . . . . . . . . . . . . . . . . . . . . . . . . . . . . . . . . . 5-5
PROFIBUS DP Connector . . . . . . . . . . . . . . . . . . . . . 5-5
. . . . . . . . . . . . . . . . . . . . . . . . . . . .
SelfLocking Tabs 5-5
Installing the 1747APB Module . . . . . . . . . . . . . . . . . 6-1
European Union Directive Compliance . . . . . . . . . . . . . . . . . 6-1
EMC Directive . . . . . . . . . . . . . . . . . . . . . . . . . . . . . . . . 6-1
Setting the DIP Switch . . . . . . . . . . . . . . . . . . . . . . . . . . . . 6-2
Switch Setting Summary . . . . . . . . . . . . . . . . . . . . . . . . . 6-2
Hold Last State . . . . . . . . . . . . . . . . . . . . . . . . . . . . . 6-3
I/O Module Keying . . . . . . . . . . . . . . . . . . . . . . . . . . . 6-4
Setting the Station Address Switch . . . . . . . . . . . . . . . . . . . 6-5
Station Address Setting Example . . . . . . . . . . . . . . . . . . . 6-6
Installing the 1747APB Module . . . . . . . . . . . . . . . . . . . . . . 6-6
Inserting the 1747APB Module . . . . . . . . . . . . . . . . . . . . 6-6
Removing the 1747APB Module . . . . . . . . . . . . . . . . . . . 6-7
StartUp and Operation . . . . . . . . . . . . . . . . . . . . . . . 7-1
System Setup . . . . . . . . . . . . . . . . . . . . . . . . . . . . . . . . . . 7-1
Powerup and Initialization Sequences . . . . . . . . . . . . . . . . . 7-1
Save Mode . . . . . . . . . . . . . . . . . . . . . . . . . . . . . . . . . . 7-2
Check Mode . . . . . . . . . . . . . . . . . . . . . . . . . . . . . . . . . 7-2
Normal Operation . . . . . . . . . . . . . . . . . . . . . . . . . . . . . . . . 7-2
Expansion Chassis Power Loss . . . . . . . . . . . . . . . . . . . . . 7-3
Table of Contents iii
Troubleshooting . . . . . . . . . . . . . . . . . . . . . . . . . . . . 8-1
Viewing Status and Fault Codes from the 1747APB
Module's Display . . . . . . . . . . . . . . . . . . . . . . . . . . . . . . 8-1
Status Codes . . . . . . . . . . . . . . . . . . . . . . . . . . . . . . . . . 8-2
Fault Codes . . . . . . . . . . . . . . . . . . . . . . . . . . . . . . . . . . 8-3
Primary Diagnostic Display . . . . . . . . . . . . . . . . . . . . . 8-3
Alternating Diagnostic Display . . . . . . . . . . . . . . . . . . . 8-4
Viewing Status and Fault Codes from the Master's
Monitoring Software . . . . . . . . . . . . . . . . . . . . . . . . . . . 8-6
Determining the Module's Condition . . . . . . . . . . . . . . . . . . . 8-6
Adapter and LED Status (Byte 9) . . . . . . . . . . . . . . . . . . . 8-6
Adapter Status Bits (0-1) . . . . . . . . . . . . . . . . . . . . . . 8-6
LED Status Bits (2-7) . . . . . . . . . . . . . . . . . . . . . . . . . 8-7
Primary and Alternating Displays (Bytes 10-15) . . . . . . . . 8-7
Hex Character Conversion Table . . . . . . . . . . . . . . . . . 8-7
Detecting Duplicate Station Addresses . . . . . . . . . . . . . . . . . 8-7
Contacting AllenBradley . . . . . . . . . . . . . . . . . . . . . . . . . . 8-7
Specifications . . . . . . . . . . . . . . . . . . . . . . . . . . . . . . 9-1
Adapter Operating Specifications . . . . . . . . . . . . . . . . . . . . . 9-1
Network Specifications . . . . . . . . . . . . . . . . . . . . . . . . . . . . 9-1
Station Delay Response Times (Tsdr) . . . . . . . . . . . . . . . 9-1
Supported DP Data Sizes . . . . . . . . . . . . . . . . . . . . . . . . 9-2
Supported DP Features . . . . . . . . . . . . . . . . . . . . . . . . . 9-2
Understanding Your SLC 500 Control System . . . . . . 10-1
Chassis Overview . . . . . . . . . . . . . . . . . . . . . . . . . . . . . . . 10-1
Selecting Your 1746 Control Power Supply . . . . . . . . . . . . . . 10-2
Power Supply Specifications . . . . . . . . . . . . . . . . . . . . . . 10-3
Example for Selecting a 1746 Power Supply . . . . . . . . . . . 10-4
The Adapter Chassis Contains: . . . . . . . . . . . . . . . . . . 10-4
SLC 500 System Installation Recommendations . . . . . . . . . . 10-7
Typical Installation . . . . . . . . . . . . . . . . . . . . . . . . . . . . . 10-7
Selecting an Enclosure . . . . . . . . . . . . . . . . . . . . . . . . . . 10-7
Spacing Considerations . . . . . . . . . . . . . . . . . . . . . . . . . 10-8
Preventing Excessive Heat . . . . . . . . . . . . . . . . . . . . . . . 10-9
Wiring Layout . . . . . . . . . . . . . . . . . . . . . . . . . . . . . . . . 10-9
Grounding Guidelines . . . . . . . . . . . . . . . . . . . . . . . . . . . 10-10
Master Control Relay . . . . . . . . . . . . . . . . . . . . . . . . . . . 10-12
EmergencyStop Switches . . . . . . . . . . . . . . . . . . . . . . . 10-13
Schematic (Using IEC Symbols) . . . . . . . . . . . . . . . . . 10-13
Schematic (Using ANSI/CSA Symbols) . . . . . . . . . . . . 10-14
Common Power Source . . . . . . . . . . . . . . . . . . . . . . . . . 10-14
Loss of Power Source . . . . . . . . . . . . . . . . . . . . . . . . . . 10-15
Input States on Power Down . . . . . . . . . . . . . . . . . . . . . . 10-15
iv Table of Contents
Other Types of Line Conditions . . . . . . . . . . . . . . . . . . . . 10-15
Power Conditioning Considerations . . . . . . . . . . . . . . . . . 10-16
Isolation . . . . . . . . . . . . . . . . . . . . . . . . . . . . . . . . . . 10-16
Suppression . . . . . . . . . . . . . . . . . . . . . . . . . . . . . . . 10-16
Special Considerations . . . . . . . . . . . . . . . . . . . . . . . . . . 10-17
Excessive Line Voltage Variations . . . . . . . . . . . . . . . . 10-17
Excessive Noise . . . . . . . . . . . . . . . . . . . . . . . . . . . . 10-17
Class I, Division 2 Applications (United States Only) . . . 10-19
Output Contact Protection . . . . . . . . . . . . . . . . . . . . . . . . 10-19
Mounting Your Control System . . . . . . . . . . . . . . . . . . . . . . 10-20
Mounting Modular Hardware Style Units . . . . . . . . . . . . . . 10-20
Leftside View (all chassis) . . . . . . . . . . . . . . . . . . . . . 10-20
1746A4 . . . . . . . . . . . . . . . . . . . . . . . . . . . . . . . . . . 10-20
1746A7 . . . . . . . . . . . . . . . . . . . . . . . . . . . . . . . . . . 10-21
1746A10 . . . . . . . . . . . . . . . . . . . . . . . . . . . . . . . . . 10-21
1746A13 . . . . . . . . . . . . . . . . . . . . . . . . . . . . . . . . . 10-22
Calculating Heat Dissipation for Your Control System . . . . . . 10-22
Module Heat Dissipation: Calculated Watts vs.
Maximum Watts . . . . . . . . . . . . . . . . . . . . . . . . . . . . 10-22
Calculating the Power Supply Loading . . . . . . . . . . . . . . . 10-23
Determining the Power Supply Dissipation . . . . . . . . . . . . 10-25
Example Heat Dissipation Calculation . . . . . . . . . . . . . . . 10-26
Installing and Wiring I/O Modules . . . . . . . . . . . . . . . . 11-1
Installing Your I/O Modules . . . . . . . . . . . . . . . . . . . . . . . . . 11-1
Features of an SLC 500 I/O Module . . . . . . . . . . . . . . . . . 11-1
Definition of Sinking and Sourcing . . . . . . . . . . . . . . . . . . 11-2
Contact Output Circuits - AC or DC . . . . . . . . . . . . . . . 11-2
Solid State DC I/O Circuits . . . . . . . . . . . . . . . . . . . . . 11-2
Sourcing Device with Sinking Input Module Circuit . . . . . 11-3
Sinking Device with Sourcing Input Module Circuit . . . . . 11-3
Sinking Device with Sourcing Output Module Circuit . . . 11-3
Sourcing Device with Sinking Output Module Circuit . . . 11-4
Inserting I/O Modules . . . . . . . . . . . . . . . . . . . . . . . . . . . 11-4
Removing I/O Modules . . . . . . . . . . . . . . . . . . . . . . . . . . 11-5
Wiring the I/O Modules . . . . . . . . . . . . . . . . . . . . . . . . . . . . 11-6
Using Removable Terminal Blocks . . . . . . . . . . . . . . . . . . 11-7
Removing the RTB . . . . . . . . . . . . . . . . . . . . . . . . . . . 11-7
Installing the RTB . . . . . . . . . . . . . . . . . . . . . . . . . . . . 11-8
Octal Label Kit Installation (For DP Master's that Use
Octal Bit Addresses Only) . . . . . . . . . . . . . . . . . . . . . 11-9
Applying the Octal Filter Label . . . . . . . . . . . . . . . . . . . 11-9
Applying the Octal Door Label . . . . . . . . . . . . . . . . . . . 11-9
Octal Kit and I/O Module Information . . . . . . . . . . . . . . 11-10
Table of Contents v
Throughput . . . . . . . . . . . . . . . . . . . . . . . . . . . . . . . . A-1
Calculating PROFIBUS System Throughput . . . . . . . . . . . . A-1
1747APB Module Backplane Time (Tbp) . . . . . . . . . . . . . A-1
Device Data Base File . . . . . . . . . . . . . . . . . . . . . . . . B-1
Glossary . . . . . . . . . . . . . . . . . . . . . . . . . . . . . . . . . . G-1
Preface
Preface
Read this preface to familiarize yourself with the rest of the manual.
This preface covers the following topics:
• who should use this manual
• the purpose of this manual
• conventions used in this manual
• Allen-Bradley support
Who Should Use Use this manual if you are responsible for designing, installing,
programming, or troubleshooting control systems that use
this Manual
programmable controllers on a PROFIBUS DP system.
You should have a basic understanding of programmable controller
products. You should also have some knowledge of the PROFIBUS
DP Standards ( DIN 19245 Part 1, Issue 1991, and Draft DIN 19245
Part 3, Issue 1993). If you do not, contact your local Allen-Bradley
representative for information on available training courses before
using this product.
Purpose of this Manual This manual is a learning and reference guide for the 1747-APB
adapter module. It describes the procedures you use to install and
operate the 1747-APB module, and provides the configuration
information you need for your DP master.
Publication 17476.14 - March 1996
P–2 Preface
Contents of this Manual
Tab Chapter Title Contents
Describes the purpose, background, and
scope of this manual. Also specifies the
Preface
audience for whom this manual is
intended.
Serves as a fast installation and startup
Quick Start for
1 guide for users who are familiar with
Experienced Users
PROFIBUS DP network operation.
Gives an overview of PROFIBUS DP
2 Profibus DP Overview
operation, and lists other PROFIBUS
products offered by AllenBradley.
Connecting to the
PROFIBUS
3 Contains network wiring information.
DP Network
PROFIBUS DP Network
Provides the configuration and
Configuring the
4 parameter data needed for the
PROFIBUS DP Master
PROFIBUS DP master.
Provides an overview of the 1747APB
1747APB Module module, and covers the compatible
5
Overview devices for the SLC chassis and the
features of the 1747APB module.
Explains setting the DIP switch and
Installing the 1747APB station number switch, and provides
6
Module installation procedures and wiring
guidelines.
1747APB
Mdl Module
Explains powerup and initialization
7 StartUp and Operation sequences, normal operation, and
remote expansion chassis power loss.
Shows how to interpret and correct
8 Troubleshooting
problems with your 1747APB module.
Gives 1747APB module and
9 Specifications
PROFIBUS DP network specifications.
Provides a chassis overview, power
Understanding Your
supply specifications, and
10 SLC 500 Control
recommendations for safely installing
System
SLC System
and mounting the control system.
Installing and Wiring I/O Explains installation procedures and
11
Modules wiring guidelines for I/O modules.
Shows how to calculate the contribution
Appendix A Throughput the 1747APB module adds to the
PROFIBUS system throughput.
Provides an example Device Data Base
Appendix B Device Data Base File
file for the 1747APB module.
Contains definitions for terms and
Glossary
abbreviations that are specific to this
product.
Publication 17476.14 - March 1996
Preface P–3
Related Documentation
The following documents contain additional information concerning
Allen-Bradley SLC� products. To obtain a copy, contact your local
Allen-Bradley office or distributor.
Document
For Read this Document
Number
An overview of the SLC 500 family of
SLC 500 System Overview 17472.30
products
Information regarding the use of analog SLC 500 Analog I/O Modules
17466.4
modules with the SLC 500 system User Manual
A detailed overview of AllenBradley AllenBradley PROFIBUS
17852.39
PROFIBUS products System Overview
Information on how to install and use the PLC5 PROFIBUS
17856.5.15
PLC5� PROFIBUS Coprocessor Coprocessor User Manual
Instructions on installing and using the PROFIBUS Manager
17856.5.20
PROFIBUS Manager software Software User Manual
Instructions on installing and using the PROFIBUS Local Station
PROFIBUS Local Station Manager Manager Software User 17856.5.21
software Manual
1794APB Flex I/O
Information on how to install and use the
PROFIBUS Adapter User 17946.5.6
PROFIBUS Flex I/O adapter
Manual
Indepth information on grounding and AllenBradley Programmable
wiring AllenBradley programmable Controller Grounding and 17704.1
controllers Wiring Guidelines
A description of important differences
between solidstate programmable Application Considerations
SGI1.1
controller products and hardwired for SolidState Controls
electromechanical devices
A complete listing of current
AllenBradley documentation, including
AllenBradley Publication
ordering instructions. Also indicates SD499
Index
whether the documents are available on
CDROM or in multilanguages.
A glossary of industrial automation terms AllenBradley Industrial
AG7.1
and abbreviations Automation Glossary
Publication 17476.14 - March 1996
P–4 Preface
Common Techniques Used The following conventions are used throughout this manual:
in this Manual
• Bulleted lists such as this one provide information, not procedural
steps.
• Numbered lists provide sequential steps or hierarchical
information.
• Italic type is used for emphasis.
We also use this convention to call attention to helpful information.
�
AllenBradley Support Allen-Bradley offers support services worldwide, with over 75
Sales/Support Offices, 512 authorized Distributors and 260
authorized Systems Integrators located throughout the United States
alone, plus Allen-Bradley representatives in every major country in
the world.
Local Product Support
Contact your local Allen-Bradley representative for:
• sales and order support
• product technical training
• warranty support
• support service agreements
Technical Product Assistance
If you need to contact Allen-Bradley for technical assistance, please
review the information in the Troubleshooting chapter first. Then
call your local Allen-Bradley representative.
Publication 17476.14 - March 1996
Chapter 1
Quick Start
for Experienced Users
This chapter helps you to get started using the 1747-APB module; a
DP slave (adapter) that can be used with any PROFIBUS DP master.
We base the procedures here on the assumption that you understand
the PROFIBUS network and DP protocol. You also must have a
basic understanding of programmable controller products.
Because it is a start-up guide for experienced users, this chapter does
not contain detailed explanations about the procedures listed. It
does, however, reference other chapters in this book where you can
get more information.
If you have any questions, or are unfamiliar with the terms used or
concepts presented in the procedural steps, always read the
referenced chapters before trying to apply the information.
This chapter:
• tells you what tools and equipment you need
• lists preliminary considerations
• describes how to configure the 1747-APB module
• explains how to install and wire the 1747-APB and I/O modules
• describes connection of the PROFIBUS DP network
• lists the information needed for configuring the DP master for
communication with the 1747-APB module
• discusses system power-up procedures
Required Tools and
You must supply the following equipment to connect your
Equipment 1747-APB module to a PROFIBUS DP network (see chapter 3 for
more information):
• a 9 pin D-sub connector
• network connection equipment
For Line Type A (baud rates up to 1.5M bit/s): shielded twisted
pair cable (We recommend Belden PROFIBUS cable, 3079A.)
For Line Type B (baud rates up to 500k bit/s): drop cables,
T-junction connectors, and bus segment cables (We recommend
Sprecher + Schuh equipment.)
• termination blocks, if the devices on the end of the network do
not have built-in terminating resistors (We recommend Sprecher
+ Schuh, Catalog Number PCE-0, Part Number 87.890.284-01.)
Publication 17476.14 - March 1996
O 1 2 3 456 7 8
N
1–2 Quick Start for Experienced Users
Important: We assume you are familiar with the connection
equipment of the PROFIBUS network. Refer to the
installation instructions shipped with this equipment for
installation and precautionary information.
Procedures
Reference
1. Check the contents of shipping box.
Unpack the shipping box making sure that the contents include:
• SLC 500 PROFIBUS adapter module (Catalog Number 1747APB)
• user manual (Publication 17476.14)
-
• Device Database File diskette (GSD file)
If the contents are incomplete, call your local AllenBradley/Sprecher+Schuh representative for
assistance.
2. Ensure your chassis supports placement of the 1747APB module. Reference
Check to see that your 1746 chassis supports placement of the adapter module by: Chapter 9
(Specifications)
• reviewing the power requirements of your system (The adapter consumes 0.6A @ 5 Volts.)
• calculating the total load on the 1746 system power supply using the worksheet provided on
Chapter 10
(Understanding
page 10-6.
Your SLC 500
Control System)
Reference
3. Configure the module using the DIP switch.
Set the DIP switch (located on the printed circuit board) to the desired setting. Chapter 6
(Installing the
1747APB
Module)
1. Hold Last State
Hold Last State
I/O Module Keying
ON = Hold Last State
Unused
ON
Unused
Unused
OFF
OFF = Do Not Hold Last State (default)
Unused
Unused
Unused
2. I/O Module Keying
ON = Save Mode (default)
OFF = Check Mode
Switches 3-8 are not used and should remain
in their default positions (OFF) to ensure
proper operation of the module.
Publication 17476.14 - March 1996
Quick Start for Experienced Users 1–3
4. Set the station address switch. Reference
To change the station address to a new setting, use a screwdriver to turn each of the selector Chapter 6
(Installing the
switches. Allowable settings range from 01 to 99. The switches can be turned either clockwise or
1747APB
counterclockwise.
Module)
Important: The PROFIBUS DP protocol mechanisms do not provide the ability to detect and report
a duplicate station address between a DP master and a DP slave device, or between
two DP slaves (only between two DP masters).
ADAPTER–PB
Tens Digit Selector
PROFI STAT
DIAGNOSTIC
In this example, the
TENS
DIGIT station address
ONES
DIGIT
switch is set at 01.
STATION
ADDRESS
PROFIBUS DP
Station Address
Switch
DANGER
Do not connect or
Ones Digit Selector
disconnect the Profibus
cable while the circuit is
live unless the area is
known to be
nonhazardous.
1747APB
5. Install the 1747APB and I/O modules in the 1746 chassis. Reference
Chapter 6
(Installing the
ATTENTION: Never insert, remove, or wire modules
1747APB
with power applied to the chassis or devices wired to
!
Module)
the module.
Follow the steps below: Chapter 11
(Installing and
1. Make sure system power is off; then insert the modules into the 1746 chassis.
Wiring I/O
Modules)
Important: The 1747APB module must be inserted into the left slot (slot 0), as shown below.
Do not install the 1747APB module in a 1746 expansion chassis.
1746 Chassis
Module Release
Card Guide
Publication 17476.14 - March 1996
1–4 Quick Start for Experienced Users
2. Cover any unused slots with card slot fillers (Catalog Number 1746N2) to keep the chassis free
from debris and dust.
3. Write the appropriate slot, chassis, and module type on the removable terminal block labels
supplied with the 1746 I/O modules.
4. Wire the I/O devices.
Reference
6. Attach the octal labels, if applicable.
Important: This step only applies if the DP master uses octal bit addressing. Chapter 11
(Installing and
A list of I/O modules that include an octal label kit can be found on page 11-10.
Wiring I/O
Modules)
Adhere the octal labels over the existing decimal labels, as shown below.
Decimal Filter Label Octal Filter Label
INPUT
OCTAL
Octal Door Label
1746-XXXX 1746-XXXX (OCTAL)
Decimal Door Label
Reference
7. Connect all devices on the PROFIBUS DP network.
Ensure that you: Chapter 3
(Connecting to the
• Select the appropriate line type (A or B) for your requirements.
PROFIBUS DP
• For line type A (up to 1.5M bit/s): Daisy chain each network device.
Network)
For line type B (up to 500k bit/s): Use drop cables, Tjunctions, and bus segments to connect the
PROFIBUS media.
• Connect the appropriate termination resistors or blocks on each end of the network.
• Attach the bus connector to the socket 9 pin Dsub connector on the front of the 1747APB
module for connection to the network.
Publication 17476.14 - March 1996
Quick Start for Experienced Users 1–5
8. Configure the DP master for communication with the adapter module. Reference
Use your DP master's configuration software to define the configuration and parameter data in the Chapter 4
(Configuring the
PROFIBUS DP master.
PROFIBUS DP
In addition, bus parameters and the location of I/O data within the DP master data tables must be Master)
defined. See your DP master's user manual for details.
your DP master's
user manual
Reference
9. Go through the system startup procedure.
Chapter 7
ATTENTION: Never insert, remove, or wire modules (StartUp and
Operation)
with power applied to the chassis or devices wired to
!
the module.
Follow the steps below:
1. Cycle power in save mode (I/O Keying DIP switch ON).
2. Remove power from the system.
3. Remove the 1747APB module and put it in check mode (I/O Keying DIP switch OFF).
4. Replace the 1747APB module in slot 0.
5. Apply power to your system.
Reference
10. Check that the module is operating correctly.
During normal operation, when not connected to a PROFIBUS line or not yet initialized, the 1747APB Chapter 7
(StartUp and
module appears as shown below:
Operation)
ADAPTER–PB
Chapter 8
PROFI LED is off or red. STAT LED is green.
PROFI STAT
(Troubleshooting)
Diagnostic display indicates
a noc or abf condition. DIAGNOSTIC
Reference
11. Initialize master/slave communication.
Once communication is established with the master, the 1747APB module appears as shown below: your DP master's
user manual
ADAPTER–PB
PROFI LED is green. STAT LED is green.
PROFI STAT
Diagnostic display indicates
a run condition. DIAGNOSTIC
Publication 17476.14 - March 1996
Chapter 2
PROFIBUS DP Overview
Read this chapter for an overview of PROFIBUS DP. Topics
include:
• introduction to PROFIBUS DP
• communication between DP masters and DP slaves
• PROFIBUS DP products available from Allen-Bradley
Introduction to PROFIBUS DP is the performance-optimized version of
PROFIBUS DP PROFIBUS. It is a remote I/O protocol designed for high-speed data
transmission between automation systems and distributed
peripherals, such as remote I/O chassis or operator interface panels.
PROFIBUS DP is most useful for time-critical communication.
There are two main devices on the PROFIBUS DP network: the DP
master(s) and DP slave(s). The DP master acts as a requester of data
from the DP slaves. A DP master of controller type (Class 1) may
also act as a responder to requests made from a DP master of
management type (Class 2).
The DP slaves act only as responders to a DP master, implementing a
defined set of functions. These functions are:
• data exchange
• check configuration
• set parameters
• read diagnostics
• get configuration
�
• global control
• read output
• read input
`
• set slave address
�
Only Clear Data is supported by the 1747APB module.
`
Not supported by the 1747APB module.
Communication Between The PROFIBUS DP network uses the polling principle for
DP Masters and DP Slaves communication, in which the DP master sends and requests
information, and the DP slave sends back a response. This is a
cyclic exchange of information that occurs independently from the
actual update of the database by the DP master and DP slave
application.
Publication 17476.14 - March 1996
2–2 PROFIBUS DP Overview
Before data exchange begins, each device on the network must have
a unique station number assigned to it. (See chapter 6 for
information on setting the 1747-APB module’s station number.)
How Data is Exchanged on the Network
To exchange I/O data with the DP slaves on the network, the DP
master must have sets of parameter and configuration data for each
DP slave. This data contains all the information necessary to define
the DP slave. In addition, the DP master’s parameter data includes
bus parameters and an address assignment table.
Data is exchanged over predefined Source and Destination Service
Access Points (SSAPs and DSAPs). The maximum size of data that
can be exchanged is 244 bytes.
Defining the DP Slave Data
The structure of the DP slave configuration data can be divided into
a maximum of 64 logical modules, (however, the 1747-APB module
supports 30 due to physical slot limitations), each with as many as 16
words of input and or output data. The configuration also specifies
whether the data is sent in bytes or words.
When communication begins, the DP master sends the DP slave
parameter data and information on what it expects is the DP slave’s
configuration data. Upon receipt, the DP slave compares this
information to its actual configuration. If the master’s information
does not exactly match the slave’s actual configuration, a fault
occurs. (See chapter 4 for specific information on defining data for
the 1747-APB module.)
Publication 17476.14 - March 1996
PROFIBUS DP Overview 2–3
PROFIBUS DP Products The illustration below shows the Allen-Bradley PROFIBUS DP
products and how they fit into an example network configuration.
Available from
AllenBradley
1785PFB/B
�
1747APB Adapter/Slave
Coprocessor
Bus Termination
Adapter Expansion
Chassis Chassis
DP
Flex I/O Adapter
RS232
Personal Computer
with Local Station
Manager and
PanelView
PROFIBUS Manager
Personal Computer
with PanelBuilder
�
The 1785PFB/B Coprocessor also
Bus Termination
supports PROFIBUS FMS networks.
For more information
Descriptions of each of these products can be found on the pages that
follow. If you need more information, contact your local
Allen-Bradley integrator or sales office for assistance.
Publication 17476.14 - March 1996
2–4 PROFIBUS DP Overview
The 1785PFB/B Coprocessor
The coprocessor is a communication module that enables a PLC-5
processor to connect and operate as a master/scanner in the
PROFIBUS DP (and FMS) network. Through the coprocessor, the
PLC-5 processor communicates and controls adapter/slave devices
contained in the network.
Module Status LED
Port 1 (FMS)
Port 2 (DP) Status LED
Status LED
FMS Port
DP Port
Processor
Interface
RS232 Port
20581-M
Local Station Manager Software
The Local Station Manager is a PC program that runs under
Microsoft� Windows version 3.1, and transfers data between your
personal computer and the coprocessor over an RS-232 interface.
This software provides management features that enable you to:
• debug and maintain the network
Local Station Manager Software
• monitor the network (WHO)
• monitor events
• reset the coprocessor
• change master/slave modes
• monitor diagnostics
• set-up basic communication parameters (i.e., address, maximum
address, baud rate)
• download into the coprocessor configuration data defined using
the PROFIBUS Manager software
Detailed requirements, installation procedure, management features
for troubleshooting and user instructions are explained in the Local
Station Manager Software User Manual (publication number
1785-6.5.21) that ships with the 1785-PFB/B coprocessor.
Publication 17476.14 - March 1996
1 2 3 456 7 8
SW3
PROFIBUS DP Overview 2–5
PROFIBUS Manager Software
The PROFIBUS Manager is also an Allen-Bradley PC program that
runs under Microsoft Windows version 3.1. The software contains
all of the functionalities of the Local Station Manager. In addition,
this program allows you to create, download and monitor network
configurations on your personal computer through an RS-232
PROFIBUS Manager Software interface to your coprocessor.
Catalog Number 1785PFBMGR
Use the PROFIBUS Manager to:
• manage projects
• create FMS projects
• create DP projects
• monitor applications
• import and export configurations
• set up communication parameters for your applications:
– Fieldbus Data Link (FDL)
– Communication Relationship List (CRL)
– Object Dictionary (OD)
– polling cycle timings
– slave configuration/parameter database
To purchase the PROFIBUS Manager (cat. no. 1785-PFBMGR),
contact your local Allen-Bradley representative.
The 1747APB Module
BiColor
BiColor The 1747-APB module is an SLC 500 single-slot module that
ADAPTER–PB
Communication
Health
PROFISTAT
LED interacts with the SLC 500 backplane and any DP master/scanner
LED
controller on a PROFIBUS DP network. It occupies the first slot
Labels
DIAGNOSTIC
(slot 0) of a 1746 chassis.
Seven Segment
Diagnostic
This module acts as a DP adapter/slave device to the DP
Display
RES/HLS
SAV/CHK
master/scanner controller, and acts as the master of the 1746 chassis
NO FUNC
NO FUNC
NO FUNC
TENS
in which it is installed. (The module also supports up to two optional
DIGIT NO FUNC
NO FUNC
ONES
DIGIT NO FUNC
expansion chassis.) See chapter 5, 1747-APB Module Overview, for
STATION
ADDRESS
PROFIBUS DP
more information.
Station Number
Switch
PROFIBUS DP
Connector
DANGER
Do not connect or
disconnect the Profibus
cable while the circuit is
live unless the area is
known to be
nonhazardous.
1747APB
Publication 17476.14 - March 1996
2–6 PROFIBUS DP Overview
The 1794APB Flex I/O Adapter
The 1794-APB is a Flex I/O adapter that interacts with the Flex I/O
backplane and any PROFIBUS DP master/scanner controller on a
Mod/Net
Status
PROFIBUS DP network.
Indicator
(red/green)
The 1794-APB module acts as an adapter, or slave device, to the DP
I/O Status master/scanner, and acts as the master controller of the Flex I/O
Indicator
system it is installed in.
(red/green)
The I/O data exchange occurs as follows: Output data is sent from
PROFIBUS
Connector Network
the DP master/scanner controller across the PROFIBUS DP network
Field power
Address
Connection
to the 1794-APB adapter. The adapter then automatically transfers
Switches
Terminals
the data across the Flex I/O backplane to the output modules. Inputs
from the input modules are collected by the Flex I/O adapter via the
backplane and sent across the PROFIBUS DP network to the DP
master/scanner controller.
PanelView� Operator Terminal
The PanelView Operator Terminal serves as an operator interface to
either the PROFIBUS DP master or an SLC 500 adapter. PanelView
offers Keypad or Combination Keypad and Touch Screen terminals
for operator input.
Front Panel Rear Panel
Á
ÁÁÁÁÁÁÁÁÁÁÁÁÁÁÁÁÁÁÁ
ÁÁÁÁÁÁÁÁÁÁÁÁÁÁÁÁÁÁÁÁÁÁÁÁÁÁÁÁÁÁÁÁÁÁÁÁÁÁÁÁÁÁÁÁÁÁÁÁÁÁÁÁÁÁÁÁÁÁÁÁÁÁÁÁÁÁÁÁÁÁÁÁÁÁÁÁÁÁÁÁÁÁÁÁÁÁÁÁÁÁÁÁÁÁÁÁÁÁÁÁÁÁÁÁ
Cursor Keys
Terminal
PROFIBUS
Display
Function Keys
Numeric Entry
Connector
Keys
PanelBuilder� Software
PanelBuilder is a Microsoft Windows graphic interface that you
install on a personal computer. PanelBuilder allows you to create,
archive, upload, and download application files to the PanelView
terminal.
PanelBuilder Software
Catalog Number 2711ND2
Publication 17476.14 - March 1996
Chapter 3
Connecting to the
PROFIBUS DP Network
This chapter presents:
• selecting the line type you should use
• connecting to the network using line type A
• connecting to the network using line type B
Selecting the Line Type The PROFIBUS network media is a balanced transmission line
corresponding to the standard EIA RS-485, terminated at both ends.
You Should Use
For PROFIBUS DP, you can use line type A and/or line type B,
depending on your system requirements. (See the table that follows.)
We recommend using line type A since it is capable of better
�
performance at greater distances, and it supports a baud rate of
1.5M bits/s.
Line Type A Line Type B
Characteristic
Requirements Requirements
Impedance 135-165 � (3-20 MHz) 100-130 � (f�100 kHz)
Capacity �30 pF/m �60 pF/m
Resistance �110 �/km -
Wire Gauge �0.64 mm �0.53 mm
2 2
Conductor Area �0.34 mm �0.22 mm
�93.75k bit/s 1200 m 1200 m
Maximum Maximum
�
187.5k bit/s 1000 m 600 m
Length Length
500k bit/s 400 m 200 m
with a Baud with a Baud
Rate of:
1.5M bit/s 200 m NA
NA = Not Applicable
�
This is the sum of all bus segment and drop cable lengths. If using a combination of both line
types, divide the lengths shown by two.
Publication 17476.14 - March 1996
3–2 Connecting to the PROFIBUS DP Network
Connecting to the Network For line type A connections, daisy chain each of the network devices
together and terminate the line at both ends. (Drop cables are also
Using Line Type A
allowed for line type A; however, we do not recommend using that
cabling scheme.) The maximum number of stations on the same
network segment is 32 (126 with repeaters).
1747APB Adapter/Slave
Bus Termination PROFIBUS DP
Master/Scanner
Adapter Expansion
Controller
Chassis Chassis
Other DP
Adapter/Slave
Other DP
Personal Computer
Adapter/Slave
with Configuration
Software
Bus Termination
Important: For detailed information on the topology and cabling
for line type A, see the PROFIBUS DP Standard (Draft
DIN 19245 Part 3, Issue 1993).
Equipment Needed for Line Type A
Cables
You must use a shielded twisted pair cable for your connections.
Off-the-shelf cables can be used to connect your adapter to a
PROFIBUS DP network; however, we recommend using Belden
PROFIBUS cable, 3079A (for baud rates up to1.5M bits/s).
Termination Blocks
Termination blocks are only needed if the devices or connectors on
the end of the network do not have built-in terminating resistors.
Connector
Connect your adapter to the PROFIBUS DP network by attaching a
bus connector to the socket 9 pin D-Sub connector on the front of the
module. We recommend using any of the following Siemens
connectors: Catalog Numbers 6ES7 972-0BA00-0XA0,
6ES5 762-2AA12, or 6ES7 193-9AA00-0XA0.
Publication 17476.14 - March 1996
Connecting to the PROFIBUS DP Network 3–3
Connecting Line Type A Cabling
Connect your cabling as shown in the following figure.
9 5
PROFIBUS DP ADAPTER
. .
. .
6 1
CABLE
Pin #1
Shield
0.01μF
Receive/ Transmit Data
1 MΩ
Signal + Pin #3
Positive Signal
Receive/ Transmit Data
Signal – Pin #8
Negative Signal
Data GND Pin#5
+ 5 V Pin #6
l
ll
(Connected via contact of
metal shrouds of connectors.)
1. Connect the cable shield to the metal shroud of the pin type
connector. The shield is connected to the 1746 I/O chassis
ground.
2. Connect data signal pins on both ends (Signal+, Pin #3 and
Signal–, Pin #8).
3. Terminate the PROFIBUS cable at both ends of the network. If
your adapter is located at one of the ends, you must terminate at
the PROFIBUS DP connector. Connectors are available that have
built-in terminating resistors (such as the Siemens connectors
mentioned on page 3–2). If you are not using a connector with
built-in resistors, terminate the cable as shown in the following
figure.
PROFIBUS DP ADAPTER
9 5
. .
. .
6 1
+ 5 V 6
CABLE
390 Ω (2%, � 1/4 W)
Signal +
3l
220 Ω (2%, � 1/4 W)
Signal - 8l
390 Ω (2%, � 1/4 W)
Data GND 5
Publication 17476.14 - March 1996
3–4 Connecting to the PROFIBUS DP Network
Connecting to the Network When using line type B, T-junctions are used to disconnect or replace
a station without breaking the network. The maximum number of
Using Line Type B
stations on the same network segment is 32 (126 with repeaters).
= Drop Cable
Personal Computer
with Configuration
= Bus Segment
Software
PROFIBUS DP
Other DP
= Termination Block
Master/Scanner
Adapter/Slave
Controller
= T-junction
PROFIBUS Media
(trunk cable)
1747APB Adapter/Slave
Other DP
Adapter/Slave
Adapter
Expansion
Chassis
Chassis
Important: For detailed information on the topology and cabling
for line type B, see the PROFIBUS Standard (DIN
19245 Part 1, Issue 1991).
Equipment Needed for Line Type B
You can use off-the-shelf drop-cables, T-junctions, bus segments,
and termination blocks to connect your adapter to a PROFIBUS DP
network. However, we recommend the following Sprecher + Schuh
equipment:
Sprecher + Schuh Equipment Catalog Number Part Number
PTL02 87.890.28002
�
PTL04 87.890.28004
Drop cable
PDC10 87.890.28210
PTS0 87.890.27601
Tjunction connector
Bus segment cable none 299.257.001
PCE0 87.890.28401
Termination Block
�
We strongly recommend using shorter drop cables (i.e., PTL02 or PTL04).
If you use other equipment, make sure that the bus segment cable
contains at least one:
• shielded twisted pair of wires for the data lines
• cable braid shield (to connect drain wire to pin 1 and metal
shroud of connector)
• wire for data ground (optional)
Publication 17476.14 - March 1996
Connecting to the PROFIBUS DP Network 3–5
Guidelines for Drop Cables
Per the standard, the recommended drop cable length is 0.3 m (1 ft).
the total capacitance of all and the total length
At a baud rate of:
drop cables is: (cable type B) is:
�19.2k bit/s 15 nanofarads 250 meters
93.75k bit/s 3 nanofarads 50 meters
187.5k bit/s 1 nanofarads 16.6 meters
500k bit/s 0.6 nanofarads 10 meters
Connecting Line Type B Cabling
Connect your cabling as shown in the figure below. The maximum
number of stations on the same network segment is 32 (126 with
repeaters).
9 5
. .
. .
PROFIBUS DP ADAPTER
6 1
(Connected via contact of
metal shrouds of connectors.)
CABLE
l
Shield Pin #1l
0.01μF
1 MΩ Receive/ Transmit Data
Pin #3
Signal +
Positive Signal
Receive/ Transmit Data
Signal – Pin #8
Negative Signal
Data GND Pin #5
+ 5 V Pin #6
1. Connect the cable shield to pin 1 on both sides. The shield pin
(Pin 1 of the PROFIBUS DP connector) is connected by an R/C
filter to 1746 I/O chassis ground.
2. Connect data signal pins on both ends (Signal+, Pin #3 and
Signal–, Pin #8).
3. Connect data ground pins on both sides. The data ground pin
(Pin 5 of the PROFIBUS DP connector) is also connected by an
R/C filter to 1746 I/O chassis ground.
Publication 17476.14 - March 1996
3–6 Connecting to the PROFIBUS DP Network
4. The cable connector hood is connected to chassis ground directly
through the adapter cover. For compliance with the European
Electromagnetic Compatibility (EMC) directives, also connect
the cable shield to metal shroud of connectors on both sides: this
will connect the cable shield directly to local chassis ground at all
points on the PROFIBUS DP network, thus bypassing the adapter
R/C filter.
Important: For improved noise immunity in networks
featuring long distances, an alternate wiring may
be preferred to avoid dc and low frequency
ground loops. In such cases, connect the cable
shield directly to local chassis ground (via the
cable connector hood) at only one point on the
PROFIBUS DP network.
5. Terminate the PROFIBUS cable at both ends of the network. If
your adapter is located at one of the ends, you must terminate at
the PROFIBUS DP connector or T-junction. If you are not using
Sprecher+Schuh termination blocks, terminate the cable as shown
in the following figure.
PROFIBUS DP ADAPTER
9 5
. .
. .
6 1
CABLE
+ 5 V 6
390 Ω (2%, � 1/4 W)
Signal +
3l
150 Ω (2%, � 1/4 W
Signal - 8l
390 Ω (2%, � 1/4 W)
Data GND 5
Publication 17476.14 - March 1996
Chapter 4
Configuring the
PROFIBUS DP Master
Configuration and parameter information is sent by the master to the
1747-APB module when communication with the module begins.
This chapter explains the information required. The following topics
are presented:
• entering DP slave data using the device data base
• entering configuration data
• entering parameter data
For information on defining the bus parameters and the location of
�
I/O data within the DP master data tables, see your DP master’s user
manual.
Entering Slave Data Using For ease of configuring your master, a disk containing an electronic
the Device Data Base device data base is shipped with each 1747-APB module. If your
PROFIBUS master’s configuration software has the capability to
read this *.gsd file (DP standard Device Data Base file), the
software will automatically extract from this file all the configuration
and parameter bytes needed to configure your master for the
1747-APB module. Otherwise you will probably need to manually
enter this information into the software. (See your configuration
software’s user manual for more information.) See appendix B for
an example Device Data Base file.
Publication 1747�6.14 - March 1996
4–2 Configuring the PROFIBUS DP Master
Entering Configuration Upon communication startup, the master’s I/O configuration data is
sent to the 1747-APB module, for the module to compare with its
Data
own I/O configuration data. It contains the range of input and output
areas as well as information on data consistency.
On a PROFIBUS DP network, the I/O data exchanged between the
PROFIBUS DP master and a DP slave is encapsulated into logical
modules. One logical module can contain up to 16 words maximum
of inputs, outputs, or combined inputs/outputs. The total I/O data
exchanged between a PROFIBUS DP master and a DP slave device
comprises a set of logical modules, described in configuration data.
For the 1747-APB module, each slot of the adapter chassis or
expansion chassis corresponds to one logical module. An
understanding of the physical layout of the chassis will help you
define the logical modules.
Understanding Slot Numbering
The 1747-APB module is capable of controlling 1 to 30 physical I/O
modules (within the restraints of the PROFIBUS data limits), each of
which resides in a chassis slot. When expansion chassis are used, the
1747-APB module treats all of the I/O modules as if they are
installed in a single chassis. (For more information on adapter
chassis and expansion chassis, see chapter 10.)
The adapter chassis and expansion chassis slots are numbered from
0–30. Slots numbered 31 and above cannot be used. The 1747-APB
module must reside in slot 0, as shown below.
Important: Installing modules in slots 31 and above causes a
1747-APB module error.
Adapter Chassis Expansion Chassis Expansion Chassis
not not
0 1 2 3 45 67 89 10 11 12 13 14 15 16 17 18 19
20 21 22 23 24 25 26 27 28 29 30
used used
1747APB
Slot Only
Publication 1747�6.14 - March 1996
Configuring the PROFIBUS DP Master 4–3
Mapping Between Logical Modules and Physical Modules
The figure below illustrates the mapping process.
Configuration Data
Logical Module 1 of the
Configuration Data corresponds
Logical Module 1
to physical module 1.
1747�APB Adapter Slave
.
Logical Module 2
.
Logical Module 3
.
Logical Module 4
.
Logical Module 5
.
Logical Module 6
Slot 0 1 2 3 4 5 6 7 8 9
.
Logical Module 7
.
Logical Module 8
Logical Module 9 of the
Logical Module 9
Configuration Data corresponds
to physical module 9.
Important: With the 1747-APB, you cannot assign more than one
physical module to a logical module, and vice versa. If
attempted, a 1747-APB configuration error occurs.
Creating the Configuration Data
Important: The configuration data in the master must exactly match
the physical configuration of the adapter chassis;
otherwise the initialization process of the adapter
module will fault, and no I/O communication will
occur.
Each logical module is described with a DP identifier byte,
containing information on the type and point size of the physical
module residing in a slot.
Important: If a slot is empty, a corresponding logical module must
still be included as part of the configuration data. (See
page 4–5 for an example.)
The following table lists the physical modules that the 1747-APB
module supports, along with the corresponding DP identifier bytes
that describe the logical modules. The table also provides the I/O
type, number of words, and data consistency for each module in case
your master’s configuration software requires you to manually enter
this information.
Publication 1747�6.14 - March 1996
��� &RQILJXULQJ WKH 352),%86 ’3 0DVWHU
,WV’3
DQG’DWD
1XPEHURI
,IWKH6ORW&RQWDLQV� ,GHQWLILHU ,�27\SHLV� &RQVLVWHQF\
:RUGVLV�
LV�
%\WHLV�
QRWKLQJ�WKDWLV�WKHVORWLVHPSW\� �� 1$ 1$ 1$
�����%$6 %$6,&/DQJXDJH0RGXOH�XVHGLQ6/&����PRGHRQO\� �� ,QSXW�2XWSXW �ZRUGV ZRUG
���+LJK�6SHHG$QDORJ,QSXWV�6HOHFWDEOH�&XUUHQWRU9ROWDJH����$QDORJ&XUUHQW
�����),2�, �� ,QSXW�2XWSXW �ZRUGV ZRUG
2XWSXWV
���+LJK�6SHHG$QDORJ,QSXWV�6HOHFWDEOH�&XUUHQWRU9ROWDJH����$QDORJ9ROWDJH
�����),2�9 �� ,QSXW�2XWSXW �ZRUGV ZRUG
2XWSXWV
�����+6 ,0&Z���6HUYR3RVLWLRQLQJ0RGXOH �� ,QSXW�2XWSXW �ZRUGV ZRUG
�����+673� 6WHSSHU&RQWUROOHU0RGXOH �� ,QSXW�2XWSXW �ZRUGV ZRUG
�����,$� $&,QSXW0RGXOH���,QSXWV‡�������9DF �� ,QSXW �ZRUG ZRUG
�����,$� $&,QSXW0RGXOH���,QSXWV‡�������9DF �� ,QSXW �ZRUG ZRUG
�����,$�� $&,QSXW0RGXOH����,QSXWV‡�������9DF �� ,QSXW �ZRUG ZRUG
�����,%� ’&,QSXW0RGXOH���,QSXWV‡6LQN��9GF �� ,QSXW �ZRUG ZRUG
�����,%�� ’&,QSXW0RGXOH����,QSXWV‡6LQN��9GF �� ,QSXW �ZRUG ZRUG
�����,%�� ’&,QSXW0RGXOH����,QSXWV‡6LQN��9GF �� ,QSXW �ZRUGV ZRUG
�����,&�� ’&,QSXW0RGXOH����,QSXWV‡6LQN��9GF �� ,QSXW �ZRUG ZRUG
�����,*�� 77/,QSXW0RGXOH����,QSXWV‡�9GF �� ,QSXW �ZRUG ZRUG
�����,+�� ’&,QSXW0RGXOH����,QSXWV‡���9GF �� ,QSXW �ZRUG ZRUG
�����,0� $&,QSXW0RGXOH���,QSXWV‡�������9DF �� ,QSXW �ZRUG ZRUG
�����,0� $&,QSXW0RGXOH���,QSXWV‡�������9DF �� ,QSXW �ZRUG ZRUG
�����,0�� $&,QSXW0RGXOH����,QSXWV‡�������9DF �� ,QSXW �ZRUG ZRUG
�����,1�� ,QSXW0RGXOH����,QSXWV‡��9DF�GF �� ,QSXW �ZRUG ZRUG
�����,2� &RPELQDWLRQ0RGXOH���,QSXWV‡�������9DF����2XWSXWVUHOD\ �� ,QSXW �ZRUG ZRUG
�����,2� &RPELQDWLRQ0RGXOH���,QSXWV‡�������9DF����2XWSXWVUHOD\ �� ,QSXW �ZRUG ZRUG
�����,2�� &RPELQDWLRQ0RGXOH���,QSXWV‡�������9DF����2XWSXWVUHOD\ �� ,QSXW �ZRUG ZRUG
�����,7%�� )DVW’&,QSXW0RGXOH����,QSXWV‡6LQN ��9GF �� ,QSXW �ZRUG ZRUG
�����,79�� )DVW’&,QSXW0RGXOH����,QSXWV‡6RXUFH��9GF �� ,QSXW �ZRUG ZRUG
�����,9� ’&,QSXW0RGXOH���,QSXWV‡6RXUFH��9GF �� ,QSXW �ZRUG ZRUG
�����,9�� ’&,QSXW0RGXOH����,QSXWV‡6RXUFH��9GF �� ,QSXW �ZRUG ZRUG
�����,9�� ’&,QSXW0RGXOH����,QSXWV‡6RXUFH��9GF �� ,QSXW �ZRUGV ZRUG
���+LJK5HVROXWLRQ$QDORJ,QSXWV�(DFK6HOHFWDEOHWR$FFHSW(LWKHU&XUUHQWRU
�����1,� �� ,QSXW �ZRUGV ZRUG
9ROWDJH
���+LJK5HVROXWLRQ$QDORJ,QSXWV�6HOHFWDEOH�&XUUHQWRU9ROWDJH����$QDORJ
�����1,2�, �� ,QSXW�2XWSXW �ZRUGV ZRUG
&XUUHQW2XWSXWV
���+LJK5HVROXWLRQ$QDORJ,QSXWV�6HOHFWDEOH�&XUUHQWRU9ROWDJH����$QDORJ
�����1,2�9 �� ,QSXW�2XWSXW �ZRUGV ZRUG
9ROWDJH2XWSXWV
�����12�, $QDORJ0RGXOH���&XUUHQW2XWSXWV‡�WR��P$ �� 2XWSXW �ZRUGV ZRUG
�����12�9 $QDORJ0RGXOH���9ROWDJH2XWSXWV‡��9GFWR���9DF �� 2XWSXW �ZRUGV ZRUG
�����15� 57’�5HVLVWDQFH,QSXW0RGXOH �� ,QSXW�2XWSXW �ZRUGV ZRUG
�����17� 7KHUPRFRXSOH�P90RGXOH �� ,QSXW�2XWSXW �ZRUGV ZRUG
�����2$� $&2XWSXW0RGXOH���7ULDF‡�������9DF �� 2XWSXW �ZRUG ZRUG
�����2$�� $&2XWSXW0RGXOH����7ULDF‡�������9DF �� 2XWSXW �ZRUG ZRUG
�����2$3�� $&2XWSXW0RGXOH����7ULDF‡�������9DF �� 2XWSXW �ZRUG ZRUG
�����2%� ’&2XWSXWPRGXOH���7UDQVLVWRU6RXUFH‡�����9GF �� 2XWSXW �ZRUG ZRUG
�����2%�� ’&2XWSXWPRGXOH����7UDQVLVWRU6RXUFH‡�����9GF �� 2XWSXW �ZRUG ZRUG
1$�1RW$SSOLFDEOH�
&RQWLQXHG RQ WKH QH[W SDJH�
3XEOLFDWLRQ����������0DUFK����
&RQILJXULQJ WKH 352),%86 ’3 0DVWHU ���
,WV’3
DQG’DWD
1XPEHURI
,IWKH6ORW&RQWDLQV� ,GHQWLILHU ,�27\SHLV� &RQVLVWHQF\
:RUGVLV�
LV�
%\WHLV�
�����2%�� ’&2XWSXWPRGXOH����7UDQVLVWRU6RXUFH‡�����9GF �� 2XWSXW �ZRUGV ZRUG
�����2%3� +LJK&XUUHQW’&2XWSXW0RGXOH��� &XUUHQW6RXUFH‡��9GF �� 2XWSXW �ZRUG ZRUG
�����2%3�� +LJK&XUUHQW’&2XWSXW0RGXOH���� &XUUHQW6RXUFH‡��9GF �� 2XWSXW �ZRUG ZRUG
�����2*�� 77/2XWSXW0RGXOH����2XWSXWV‡�9GF �� 2XWSXW �ZRUG ZRUG
�����29� ’&2XWSXW0RGXOH���7UDQVLVWRU6LQN‡�����9GF �� 2XWSXW �ZRUG ZRUG
�����29�� ’&2XWSXW0RGXOH����7UDQVLVWRU6LQN‡�����9GF �� 2XWSXW �ZRUG ZRUG
�����29�� ’&2XWSXW0RGXOH����7UDQVLVWRU6LQN‡����9GF �� 2XWSXW �ZRUGV ZRUG
�����293�� +LJK&XUUHQW’&2XWSXW0RGXOH����� &XUUHQW6LQN‡��9GF �� 2XWSXW �ZRUG ZRUG
�����2:� 5HOD\2XWSXW0RGXOH���2XWSXWV‡������9DF�������9GF �� 2XWSXW �ZRUG ZRUG
�����2:� 5HOD\2XWSXW0RGXOH���2XWSXWV‡������9DF�������9GF �� 2XWSXW �ZRUG ZRUG
�����2:�� 5HOD\2XWSXW0RGXOH����2XWSXWV‡������9DF�������9GF �� 2XWSXW �ZRUG ZRUG
�����2;� ,VRODWHG5HOD\2XWSXW��3RLQW�0RGXOH �� 2XWSXW �ZRUG ZRUG
�����.( ’+�����56����&,QWHUIDFH0RGXOH �� ,QSXW�2XWSXW �ZRUGV ZRUG
&RQILJXUDWLRQ’DWD([DPSOH
)RU WKLV H[DPSOH� DVVXPH D ��VORW FKDVVLV LV FRQILJXUHG�
6ORW � � � � � � �
7KHQWKHFRQILJXUDWLRQGDWD
,IWKHFKDVVLVFRQWDLQVWKHVHPRGXOHV�
WKDWVKRXOGEHHQWHUHGLV�
6ORW &DWDORJ /RJLFDO
3K\VLFDO0RGXOH ’3,GHQWLILHU%\WH
1XPEHU 1XPEHU 0RGXOH
� 352),%86’3$GDSWHU �����$3% 1$ 1$
� ,QSXW0RGXOH �����,$�� � ��
� ,QSXW0RGXOH �����,$�� � ��
� ��SW�2XWSXW0RGXOH �����2%�� � ��
� (PSW\6ORW 1$ � ��
� ��SW�2XWSXW0RGXOH �����2%�� � ��
� ��SW�&RPELQDWLRQ0RGXOH �����,2�� � ��
1$�1RW$SSOLFDEOH�
3XEOLFDWLRQ����������0DUFK����
��� &RQILJXULQJ WKH 352),%86 ’3 0DVWHU
(QWHULQJ3DUDPHWHU’DWD 8SRQ FRPPXQLFDWLRQ VWDUWXS� SDUDPHWHU GDWD LV GHOLYHUHG IURP WKH
’3 PDVWHU WR WKH �����$3% PRGXOH� 7KH PRGXOH GRHV QRW UHTXLUH
DQ\ VSHFLILF XVHU SDUDPHWHU GDWD EHVLGHV JHQHULF VWDQGDUG SDUDPHWHU
GDWD�
Frequently asked questions
How does Industrial Trading differ from its competitors?

Is there a warranty for the 1785-PFBMGR?

Which carrier will Industrial Trading use to ship my parts?

Can I buy parts from Industrial Trading if I am outside the USA?

Which payment methods does Industrial Trading accept?

What they say about us
FANTASTIC RESOURCE
One of our top priorities is maintaining our business with precision, and we are constantly looking for affiliates that can help us achieve our goal. With the aid of GID Industrial, our obsolete product management has never been more efficient. They have been a great resource to our company, and have quickly become a go-to supplier on our list!
Bucher Emhart Glass
EXCELLENT SERVICE
With our strict fundamentals and high expectations, we were surprised when we came across GID Industrial and their competitive pricing. When we approached them with our issue, they were incredibly confident in being able to provide us with a seamless solution at the best price for us. GID Industrial quickly understood our needs and provided us with excellent service, as well as fully tested product to ensure what we received would be the right fit for our company.
Fuji
HARD TO FIND A BETTER PROVIDER
Our company provides services to aid in the manufacture of technological products, such as semiconductors and flat panel displays, and often searching for distributors of obsolete product we require can waste time and money. Finding GID Industrial proved to be a great asset to our company, with cost effective solutions and superior knowledge on all of their materials, it’d be hard to find a better provider of obsolete or hard to find products.
Applied Materials
CONSISTENTLY DELIVERS QUALITY SOLUTIONS
Over the years, the equipment used in our company becomes discontinued, but they’re still of great use to us and our customers. Once these products are no longer available through the manufacturer, finding a reliable, quick supplier is a necessity, and luckily for us, GID Industrial has provided the most trustworthy, quality solutions to our obsolete component needs.
Nidec Vamco
TERRIFIC RESOURCE
This company has been a terrific help to us (I work for Trican Well Service) in sourcing the Micron Ram Memory we needed for our Siemens computers. Great service! And great pricing! I know when the product is shipping and when it will arrive, all the way through the ordering process.
Trican Well Service
GO TO SOURCE
When I can't find an obsolete part, I first call GID and they'll come up with my parts every time. Great customer service and follow up as well. Scott emails me from time to time to touch base and see if we're having trouble finding something.....which is often with our 25 yr old equipment.
ConAgra Foods