ALLEN-BRADLEY 1333AAA
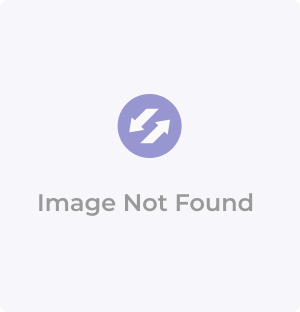
Description
Allen Bradley 1333AAA AC Drive. 230V | 1HP
Part Number
1333AAA
Price
Request Quote
Manufacturer
ALLEN-BRADLEY
Lead Time
Request Quote
Category
AC Drive
Datasheet
Extracted Text
Bulletin 1333 3/4-20 HP (.55-15 kW) Adjustable Frequency AC Drive (Series D) User Manual Important User Information Because of the variety of uses for this equipment and because of the differences between this solid-state equipment and electromechanical equipment, the user of and those responsible for applying this equipment must satisfy themselves as to the acceptability of each application and use of the equipment. In no event will Allen-Bradley Company be responsible or liable for indirect or consequential damages resulting from the use or application of this equipment. The illustrations shown in this manual are intended solely to illustrate the text of this manual. Because of the many variables and requirements associated with any particular installation, the Allen-Bradley Company cannot assume responsibility or liability for actual use based upon the illustrative uses and applications. No patent liability is assumed by Allen-Bradley Company with respect to use of information, circuits or equipment described in this text. Reproduction of the content of this manual, in whole or in part, without written permission of the Allen-Bradley Company is prohibited. The information in this manual is organized in numbered chapters. Read each chapter in sequence and perform procedures when you are instructed to do so. Do not proceed to the next chapter until you have completed all procedures. Throughout this manual we use notes to make you aware of safety considerations: ATTENTION: Identifies information about practices or circumstances that can lead to personal injury or death, property ! damage or economic loss. Attentions help you: • Identify a hazard. • Avoid the hazard. • Recognize the consequences. Important: Identifies information that is especially important for successful application and understanding of the product. Shock Hazard labels may be located on or inside the drive to alert people that dangerous voltage may be present. Summary of Changes Summary of Changes Summary of Manual Changes This release of the 1333-5.2 User Manual contains some new and corrected information. The new and corrected information is summarized in the table below. For further information, refer to the page numbers provided. Description of New or Corrected Information Page Type Drive Input Terminals 48 Correction Recommended Wire Size and Torque 415 Correction SW2 Factory Setting -- Figure 45 420 New Terms 6 & 3 Analog Meter Output Meter Load Impedance 422 Correction Terms 13 & 14 -- S1/4SP Terms 13 & 14 -- S2/4SP SW2 Factory Setting 424 New Parameter 02 -- Deceleration Time 1 From 00.011000 seconds . . . sets the decel time . . . 59 Correction From 10001600 seconds . . . sets the decel time . . . 59 Correction Local/Remote Control Enable If set to 0 . . . w Local Jog can be selected by . . . the Shift button. 514 Correction If set to 2. . . w Local Jog can be selected by . . . the Shift button. 515 Correction 1. SW2 Factory Setting 524 New As shown in Figure 45 in Chapter 4 If Parameter 19 = 0 When Control Board Switch SW2 is Set to . . . 525 Correction If Parameter 19 = 1 When Control Board Switch SW2 is Set to . . . 525 Correction If Parameter 19 = 2 When Control Board Switch SW2 is Set to . . . 525 Correction As shown in Figure 45 in Chapter 4 If Parameter 19 = 0 and Parameter 20 = 0 When Control Board Switch SW2 is Set to . . . 526 Correction If Parameter 19 = 1 and Parameter 20 = 0 When Control Board Switch SW2 is Set to . . . 526 Correction If Parameter 19 = 2 and Parameter 20 = 0 When Control Board Switch SW2 is Set to . . . 526 Correction As shown in Figure 45 in Chapter 4 If Parameter 19 = 0 and Parameter 20 = 1 When Control Board Switch SW2 is Set to . . . 527 Correction If Parameter 19 = 1 and Parameter 20 = 1 When Control Board Switch SW2 is Set to . . . 527 Correction If Parameter 19 = 2 and Parameter 20 = 1 When Control Board Switch SW2 is Set to . . . 527 Correction Preset Frequency Settings Auxiliary Accel and Decel Settings 534 Correction Table of Contents PreInstallation Care . . . . . . . . . . . . . . . . . . . . . . . . . . . . . 11 Before installing and operating your 1333 Series D drive, carefully read this manual and observe all precautions. The catalog number of your drive as explained in Chapter 2 � Drive Identification lists the drive rating, type of enclosure, nominal line voltage, phase and frequency. Specifications for all drives including standard controls, adjustment range, diagnostics and environmental qualifications are listed in Chapter 3 � Specifications. . . . . . . . . . . . . . . . . . . . . . . . . . . 1�1 Carefully unpack the drive, taking care to save the shipping carton and any packing material should return be necessary. Verify that the items on the packing list or bill of lading agree with your order. . . . . . . . . . . . . . . . . . . . . . . . . . . . . . . . . . . . . . . 1�1 Factory and Field Parameter Settings . . . . . . . . . . . . . . . . C1 Preface Manual Objective This manual defines the installation, operation, startup and fault codes for the Allen-Bradley 1333 Series D Adjustable Frequency AC Drive. It is intended for use by personnel familiar with the functions of solid-state drive equipment. Also provided are interconnection drawings for 1333 options in Appendix A, and Bulletin 1333 Series D application data in Appendix D. The 1333 Series D User Manual is designed to be read and used like an ordinary textbook. Read the manual once from the beginning in the order presented to gain basic knowledge about your drive. Each chapter builds upon information presented in the previous chapter. The majority of the information presented is arranged and written by drive function. Individual parameters in Chapter 5 are grouped under functional sub-headings (such as Accel and Decel Settings or Volts-per-Hertz Curve Settings), as is the statup procedure in Chapter 6. Appendix C provides paired parameter tables which are also grouped by function to graphically show parameter interaction. To assure successful installation and operation, the material presented in each chapter must be thoroughly read and understood before proceeding to the next chapter. Particular attention should be directed to the Attention and Important statements contained within. Become familiar with tasks that must be performed in a sequence for safety and successful completion. P-1 Preface Important Information about this Manual This manual has been prepared primarily to support this product in a single application. It is a standard document that is intended to help the user understand the individual operating characteristics and limitations of this equipment including hazards associated with installation and setup procedures. Note the following points: • This equipment has been designed to meet the requirements of a component in an integrated system. • It must be noted that special considerations are to be given to characteristics of other peripheral solid-state control equipment and the cumulative impact on safety. • Manufacturers and engineering groups responsible for specification or design of electrical control equipment must refer to applicable industry standards and codes for specific safety guidelines and interface requirements. • In the actual factory environment, the user is responsible to assure compliance with applicable machine and operator safety codes or regulations which are beyond the scope and purpose of this document. General Precautions In addition to the precautions listed throughout this manual, the following statements which are general to the system must be read and understood. ATTENTION: Only personnel familiar with the 1333 AC Drive and associated machinery should plan or implement the ! installation, start-up and subsequent maintenance of the system. Failure to comply may result in personal injury and/or equipment damage. ATTENTION: This assembly may contain parts and sub-assemblies that are sensitive to electrostatic discharge. Static ! control precautions are required when testing, servicing or repairing this assembly. Component damage may result if you ignore electrostatic discharge control procedures. If you are not familiar with static control procedures, reference Allen-Bradley Publication 8000-4.5.2, Guarding Against Electrostatic Damage or any other applicable ESD protection handbook. ATTENTION: An incorrectly applied or installed system can result in component damage or reduction in product life. Wiring or ! application errors, such as undersizing the motor, incorrect or inadequate AC supply, or excessive ambient temperatures may result in malfunction of the system. P-2 Repair/Exchange Repair or Repair/Exchange Procedure For your convenience, the Allen-Bradley Standard Drives Division, and the Allen-Bradley Support Division, provide an efficient and convenient method of returning equipment eligible for repair or repair/exchange. A product service report number is required to return any equipment for repair. This may be obtained from your local Allen-Bradley Distributor or Area Sales/Support Office. Return any equipment to be repaired to the Area Sales/Support Center nearest you. Be sure to reference the product service report number on the carton and packing slip. Include your company name and address, your repair purchase order number and a brief description of the problem. This will facilitate quick return of your equipment. A complete listing of Area Sales/Support Centers is available from your local Allen-Bradley Distributor or Sales Office. R-1 Chapter 1 PreInstallation Care Before installing and operating your 1333 Series D drive, carefully read this manual and observe all precautions. The catalog number of your drive as explained in Chapter 2 — Drive Identification lists the drive rating, type of enclosure, nominal line voltage, phase and frequency. Specifications for all drives including standard controls, adjustment range, diagnostics and environmental qualifications are listed in Chapter 3 — Specifications. Receiving Once you have received your drive, careful inspection for shipping damage must be made. Damage to the shipping carton is usually a good indication that it has received improper handling. Any and all damage should be immediately reported to the freight carrier and your nearest Allen-Bradley Area Sales/Support Center. Carefully unpack the drive, taking care to save the shipping carton and any packing material should return be necessary. Verify that the items on the packing list or bill of lading agree with your order. Storage If the drive will not immediately be installed, it should be stored in a clean, dry area where the ambient temperature is not less than -25°C nor more than +65°C. The drive must not be stored in a corrosive environment nor subject to conditions in excess of the storage environment parameters stated in Chapter 3 — Specifications. Shipping The carton and materials that came with your drive have been designed and tested to provide reasonable protection against damage during transit. Should the drive be shipped to another location, it is recommended that the original shipping carton and packing material be used to protect the drive from damage in transit. 1-1 Chapter 1 Pre-Installation Care ATTENTION: This assembly contains parts and sub-assemblies that are sensitive to electrostatic discharge. Static control ! precautions are required when servicing this assembly. Component damage may result if you ignore electrostatic discharge control procedures. If you are not familiar with static control procedures, reference Allen-Bradley Publication 8000-4.5.2, Guarding Against Electrostatic Damage, or any other applicable ESD protection handbook. Electrostatic Discharge Electrostatic discharge generated by static electricity can damage the Precautions complimentary metallic oxide semiconductor devices on various drive boards. It is recommended that you perform these procedures to guard against this type of damage when circuit boards are removed or installed: • Wear a wrist type grounding strap that is grounded to the drive chassis. • Attach the wrist strap before removing the new circuit board from the conductive packet. • Remove boards from the drive and immediately insert them into their conductive packets. 1-2 I N 6 D L 6 5 C O Chapter 2 Drive Identification The following is an explanation of the catalog numbering system and information provided on the Bulletin 1333 Series D shipping carton label and drive nameplate. The 1333 Shipping Carton Label PART NO. 151014 SER. NO. A00224 � BULLETIN — 1333 INPUT 230/208/200V, 50/60Hz ADJUSTABLE OUTPUT KVA 2.0 FREQUENCY ˇ ENCL. IP 40 PHASE 3 AC DRIVE ˛ ˝ MADE IN JAPAN � CAT SER 1333-AAA D ˚¸ ˚¸— The 1333 Drive Nameplate BULLETIN 1333 ADJUSTABLE FREQUENCY AC DRIVE THE STANDARD UNIT DOES NOT PROVIDE MOTOR OVERLOAD PROTECTION IN ACCORDANCE WITH S/N CAT 1333- AAA SER D A00224 THE NEC OR CEC, PART 1. AC INPUT 3PH MADE IN JAPAN U 230/208/200 50/60 KVA 2.6 VOLTS HZ AMPS 6.5 L 3PH AC OUTPUT KVA 2.0 VOLTS 230/208/200 HZ 60 AMPS 5 ˛ˇˇ 2-1 D N E T T S E I L Q Chapter 2 Drive Identification ¶ Drive Catalog Numbers 1333 Z A A Bulletin Drive Enclosure Input Number Rating Type Voltage The first letter indicates the drive rating. 200/208/230V AC, 3-Phase, 50/60 Hertz Input Voltage Rating Nominal Code HP kW ZAA 3/4 .55 AAA 1 .75 YAA 2 1.5 BAA 3 2.2 CAA 5 4 DAA 7 1/2 5.5 EAA 10 7.5 FAA 15 11 GAA 20 15 380/415/460V AC, 3-Phase, 50/60 Hertz Input Voltage Rating Nominal Code HP kW AAB 1 .75 YAB 2 1.5 BAB 3 2.2 CAB 5 4 The second letter indicates the type of enclosure as initially shipped from the factory. A –– NEMA Type 1 (IP20). The third letter indicates drive input voltage. Drives with the code ”A” are suitable for operating from any one of the following voltage inputs: 200/208/230V AC, 50/60 Hz, 3-phase Nominal Voltage. 200/208/230V AC, 50/60 Hz, 1-phase Derated Voltage. Drives with the code ”B” are suitable for operating from any one of these voltage inputs: 380/415/460V AC, 50/60 Hz, 3-phase. • Drive Series Number Series D. ‚ Drive Input/Output Power 3-Phase. „ Drive Enclosure Rating NEMA Type 1 (IP 20). ” Drive Output kVA Listed in Chapter 3, pg. 3-2. » Drive Input Voltage Rating Explained above. … Drive Serial Number Internal factory code. ‰ Drive Part Number Internal factory code. 2-2 Chapter 3 Specifications Operating Environment Temperature: –10 to + 50°C (+14 to +122°F). Relative Humidity: 5 to 95% non-condensing. Altitude: 3,300 feet (1,000 meters) maximum without derating. Vibration: Below 0.5G, 0.8 mm peak-to-peak amplitude, x-y-z direction. Shock: 16G peak for 11ms duration. Storage Environment Temperature: –25 to +65°C (–13 to +149°F) Relative Humidity: 5 to 95% non-condensing. Enclosure NEMA Type 1 (IP20). Indicated by catalog number. Input Power Specifications Drive Rating ZAA-GAA AAB-CAB Voltage: 200-230V AC, ± 10% 380-460V AC, ± 10% Frequency: 50/60 Hz, ± 5% 50/60 Hz, ± 5% Phase: 1 or 3-phase 3-phase Bus Overvoltage Trip: 430V DC 820V DC Bus Undervoltage Trip: 160V DC 310V DC Bus Overcurrent Trip: 200% IET Power Ride-Thru: 15 ms or longer depending on the load. Control Ride-Thru: 100 ms or longer depending on the load. Control Logic Noise Showering arc transients from 350 to 2,000 Immunity: volts. 3-1 Chapter 3 Specifications 200/208/230V AC, 3Phase, 50/60 Hertz Input Voltage Standard ThreePhase Data 200VAC 208VAC 230VAC 200VAC 208VAC 230VAC Total Heat Input Current, Output Current Rating Nominal Input Input Input Input Output Output Output Output Dissipated and kVA Code HP kW Amps kVA kVA kVA Amps kVA kVA kVA Watts (BTU/hr) ZAA 3/4 .55 4.1 1.4 1.5 1.6 3.2 1.1 1.2 1.3 80 273 AAA 1 .75 6.5 2.3 2.4 2.6 5.0 1.7 1.8 2.0 100 341 YAA 2 1.5 9.0 3.1 3.2 3.6 8.0 2.8 2.9 3.2 170 580 BAA 3 2.2 14.0 4.8 5.0 5.6 11.0 3.8 4.0 4.4 250 853 CAA 5 4 22.0 7.6 7.9 8.8 17.5 6.1 6.3 7.0 360 1228 DAA 71/2 5.5 27.0 9.3 9.7 10.8 24.0 8.3 8.7 9.7 425 1449 EAA 10 7.5 37.0 12.8 13.3 14.7 33.0 11.5 11.9 13.3 480 1637 FAA 15 11 47.0 16.3 16.9 18.8 45.0 15.6 16.2 18.1 565 1927 GAA 20 15 62.0 21.5 22.3 24.7 61.0 21.1 22.0 24.6 610 2080 380/415/460V AC, 3Phase, 50/60 Hertz Input Voltage 380VAC 415VAC 460VAC 380VAC 415VAC 460VAC Total Heat Rating Nominal Input Input Input Input Output Output Output Output Dissipated Code HP kW Amps kVA kVA kVA Amps kVA kVA kVA Watts (BTU/hr) AAB 1 .75 3.3 2.2 2.4 2.6 2.1 1.4 1.5 1.7 100 341 YAB 2 1.5 4.5 3.0 3.2 3.6 4.0 2.6 2.9 3.2 170 580 BAB 3 2.2 8.0 5.3 5.8 6.4 6.0 3.9 4.3 4.8 250 853 CAB 5 4 13.0 8.6 9.3 10.4 9.4 6.2 6.8 7.5 370 1262 Derated SinglePhase Data ¶200/208/230V AC, 1Phase, 50 Hertz Input Voltage Input Current, Output Current 200VAC 208VAC 230VAC 200VAC 208VAC 230VAC Total Heat Rating Nominal Input Input Input Input Output Output Output Output Dissipated and kVA Code HP kW Amps kVA kVA kVA Amps kVA kVA kVA Watts (BTU/hr) ZAA 1/2 .37 5.7 1.1 1.2 1.3 2.4 0.8 0.9 1.0 80 273 AAA 3/4 .55 7.7 1.5 1.6 1.8 3.4 1.2 1.2 1.4 100 341 YAA 1 .75 8.8 1.8 1.8 2.0 4.5 1.6 1.6 1.8 170 580 BAA 11/2 1.1 11.9 2.4 2.5 2.7 5.4 1.9 1.9 2.2 250 853 CAA 2 1.5 17.3 3.5 3.6 4.0 7.7 2.7 2.8 3.1 360 1228 DAA 3 2.2 21.4 4.3 4.5 4.9 11.0 3.8 4.0 4.4 425 1449 EAA 5 4 29.1 5.8 6.1 6.7 15.0 5.2 5.4 6.0 480 1637 FAA 71/2 5.5 38.0 7.6 7.9 8.7 21.0 7.3 7.6 8.4 565 1927 GAA 10 7.5 49.3 9.9 10.3 11.3 28.0 9.7 10.1 11.2 610 2080 200/208/230V AC, 1Phase, 60 Hertz Input Voltage 200VAC 208VAC 230VAC 200VAC 208VAC 230VAC Total Heat Rating Nominal Input Input Input Input Output Output Output Output Dissipated Code HP kW Amps kVA kVA kVA Amps kVA kVA kVA Watts (BTU/hr) ZAA 1/2 .37 6.2 1.2 1.3 1.4 2.6 0.9 0.9 1.0 80 273 AAA 3/4 .55 8.6 1.7 1.8 2.0 3.8 1.3 1.4 1.5 100 341 YAA 1 .75 9.5 1.9 2.0 2.2 4.9 1.7 1.8 2.0 170 580 BAA 11/2 1.1 13.0 2.6 2.7 3.0 5.9 2.0 2.1 2.4 250 853 CAA 2 1.5 18.8 3.8 3.9 4.3 8.4 2.9 3.0 3.3 360 1228 DAA 3 2.2 23.4 4.7 4.9 5.8 12.0 4.2 4.3 4.8 425 1449 EAA 5 4 31.1 6.2 6.5 7.1 16.0 5.5 5.8 6.4 480 1637 FAA 71/2 5.5 41.6 8.3 8.7 9.6 23.0 10.0 8.3 9.2 565 1927 GAA 10 7.5 54.6 10.9 11.4 12.6 31.0 10.7 11.2 12.3 610 2080 ¶ .200/208/230VAC units may be derated for single phase input power The single phase will not appear on the shipping carton label or the drive nameplate. 3-2 Chapter 3 Specifications Load Requirements A balanced 3-phase inductive motor load is typical. Other motor loads may require application assistance. Output Power Waveform: Sine coded pulse width modulated waveform. Specifications Voltage: Drive Rating ZAA-GAA 0 to applied input voltage, 200V AC, 208V AC, or 230V AC –– maximum output voltage cannot exceed applied input voltage. Drive Rating AAB-CAB 0 to applied input voltage, 380V AC, 415V AC, or 460V AC –– maximum output voltage cannot exceed applied input voltage. Frequency Programmable Min and Max Limits Range: 0 to 400 Hz remote frequency command. 0.5 to 400 Hz local frequency command. Frequency ± 0.5% of selected maximum output frequency Regulation: –10 to +50°C ambient temperature range. Accel/Decel: Four independently programmable accel times. Four independently programmable decel times. Each time may be programmed over a range from 0.1 to 1600 seconds. If 0 is entered, the drive will default to 40 ms. Accel Stall Protection: 140% of rated current. Decel Stall Protection: 380V DC for 230V AC drive input voltage. 760V DC for 460V AC drive input voltage. Volts-per-Hertz: Selectable constant or square v/Hz curves. DC Boost: 0-40% of maximum output voltage adjustable in 1% increments. 3-3 Chapter 3 Specifications Starting Torque: 150% nominal at 5 Hz. Braking Torque: DC Brake: 20% of rated torque (standard) programmable duration and voltage Heavy Duty Dynamic Brake: 100% of rated torque. Stopping Frequency: 0.5-60 Hz Intermittent Standard: 140% of rated output current for Overload Capability: 1 minute. Inverse Trip: 125% of programmable overload trip level for one minute. Drive Programmable overload trip function set to motor Overload Trip: nameplate value. Ground Fault: Current sensors detect output ground fault at drive output leads. Frequency Control Inputs Digital Input Local Speed Control Frequency 0.01 Hz up to 100 Hz. Resolution: 0.1 Hz over 100 Hz. Analog Input Remote Speed Pot Frequency (Control Terminal Block, Terminals 1, 2 and 3) Resolution: 0.1 Hz up to 100 Hz. 0.2 Hz up to 200 Hz. 0.5 Hz over 200 Hz. 0-5V DC Input (Control Terminal Block, Terminals 3 and 4) 0.1 Hz up to 100 Hz. 0.2 Hz up to 200 Hz. 0.5 Hz over 200 Hz. 0-10V DC Input (Control Terminal Block, Terminals 3 and 4) 0.1 Hz up to 100 Hz. 0.2 Hz up to 200 Hz. 0.5 Hz over 200 Hz. 4-20 mA Input (Control Terminal Block, Terminals 3 and 5) 0.1 Hz up to 100 Hz. 0.2 Hz up to 200 Hz. 0.5 Hz over 200 Hz. 3-4 Chapter 3 Specifications Required Control Inputs As a minimum requirement for drive operation, the following four control inputs must be present to operate the drive: Start A momentary contact closure will start the drive. The drive will continue to run until a stop input is issued or a drive fault occurs. A start input may come from: • Either of the Local Control Panel directional start pushbuttons. • A user supplied N.O. contact or start switch connected to the Control and Signal Wiring Terminal Block. Stop A momentary open contact will stop the drive. A N.C. contact will permit the drive to run or jog. A stop input may come from: • The Local Control Panel stop pushbutton. • A user supplied N.C. contact or stop switch connected to the Control and Signal Wiring Terminal Block. Auxiliary Interlock A maintained closed contact will permit the drive to start, run, or jog. A momentary open contact will disable drive output. An auxiliary input may come from: • The factory installed metal jumper between terminals 16 and 17 of the Control and Signal Wiring Terminal Block. • A user supplied N.C. contact or switch wired to terminals 16 and 17 when the factory supplied jumper is removed. Speed Reference A speed reference sets the drive operating frequency. A speed reference input may come from: • Either of the Local Control Panel directional start pushbuttons. • A user supplied 10kΩ, 2W remote speed potentiometer connected to the Control and Signal Wiring Terminal Block. • A 0-5V DC analog signal connected to the Control and Signal Wiring Terminal Block. • A 0-10V DC analog signal connected to the Control and Signal Wiring Terminal Block. • A 4-20 mA analog signal connected to the Control and Signal Wiring Terminal Block. • 1-3 programmable preset speed switches connected to the Control and Signal Wiring Terminal Block. Through programming, a total of seven preset speeds may be selected. 3-5 Chapter 3 Specifications Optional Remote Control Inputs The following optional inputs may be connected to the Series D Bulletin 1333 drive at the Control and Signal Wiring Terminal Block. Two or Three-Wire Start/Stop Control Forward Reverse Control Jog Three Programmable Preset Speed Select Switches Auxiliary Interlock Contact Outputs The following contact outputs are available as standard. Contacts are isolated from Logic Common and other drive circuitry and have the following ratings. Resistive rating: 120V AC or 30V DC, 1 Amp. Inductive rating: 120V AC or 30V DC, 0.5 Amps. At Speed: 1 N.O. contact, closed when the drive is at or above command speed Run or 1 N.O. contact closed when the drive is running, at Overload: programmed speed, at 140% of rated output current, or over the programmable overload level. No Fault/Fault: 1 set of Form C contacts that change state to indicate that the drive has received a fault or that a fault is present when the drive is powered up. Analog Outputs 0-10V DC or 0-1 mA output programmable from 75-125% of running frequency. Drive Displays Local Displays drive output frequency, equivalent motor Programming speed, drive output amps and drive control source. May be and Display toggled to program and display 62 drive parameters. Panel: Should a fault occur while the drive is running, the panel will display the fault code. Bus Charged: Internal neon display to indicate bus voltage is greater than 50V DC. 3-6 Chapter 4 Installation and Wiring General Input Power Conditioning The Series D 1333 is suitable for direct connection to a correct voltage AC power line. There are however certain power line conditions which may introduce the possibility of drive input power component malfunction. To reduce the possibility of these malfunctions, a line reactor or isolation type transformer may be required. If the use of an input transformer is desired, only an isolation type transformer should be used. The basic rules for determining if a line reactor or isolation type transformer is required are as follows: 1. If the AC line supplying the drive has power factor correction capacitors connected, an AC line reactor or isolation type transformer must be connected between the capacitor bank and the input to the drive. 2. If the AC line frequently experiences transient power interruptions or significant voltage spikes, an AC line reactor or isolation type transformer should be used. ATTENTION: An incorrectly applied or installed system can General Installation result in component damage or reduction in product life. The most Requirements ! common causes are: • Wiring the AC line to the drive output or control terminals. • Improper bypass or output circuits. • Output circuits which do not connect directly to the motor. • Incorrect or inadequate AC supply. • Excessive ambient temperature. Contact Allen–Bradley for assistance with application or wiring. Before actual installation, remove all packing material, wedges or braces from within and around the drive. The 1333 must be installed in an area where the following installation and environmental guidelines are met. • Cabinet mounting must be upright, leaving room for a minimum clearance of 4 inches (102 mm) on the top and bottom and 2 inches (51 mm) on the sides for proper ventilation. • The drive should be easily accessible for maintenance and troubleshooting. • The rated altitude must not exceed 3,300 feet (1,000 meters). • Vibration must be within the ratings outlined in Chapter 3 – Specifications. • The ambient atmosphere must not contain volatile or corrosive gas, vapors or dust. • The relative humidity must not exceed 95% for all drive ratings. • The ambient temperature for the drive must be kept within –10 to +50°C for all ratings. 4-1 Chapter 4 Installation and Wiring ZAACAA 230V Dimensions, Weights and Conduit Entry Locations Nominal Dimensions and Weights in Inches (Millimeters) and Pounds (Kilograms) HP kW Rating Code A B C D E F G H I J K Weight 3/4, 1 .55, .75 ZAA, AAA 8.90 10.04 4.72 8.27 9.45 0.30 0.30 2.48 1.97 2.24 1.26 6.0 (226) (255) (120) (210) (240) (8) (8) (63) (50) (57) (32) (2.7) 2 1.5 YAA 8.90 11.26 5.31 8.27 10.63 0.30 0.30 2.48 1.97 2.83 1.85 8.0 (226) (286) (135) (210) (270) (8) (8) (63) (50) (72) (47) (3.6) 3, 5 2.2, 4 BAA, CAA 10.20 13.54 6.90 9.45 12.80 0.30 0.30 3.13 1.97 4.13 2.80 20.0 (259) (344) (175) (240) (325) (8) (8) (80) (50) (105) (71) (9.1) G 0.25 IN (6.35 MM) DIA. MOUNTING HOLES ADJUSTABLE FREQUENCY AC MOTOR DRIVE Hz F F A LOCK E SELECT ENTER B STOP NO. 03 SHIFT G F D F C A (NEMA Type 1 –– Front) (NEMA Type 1 –– Side) 0.905 IN (23.0 MM) DIA. CONDUIT ENTRY HOLES J K I I H (NEMA Type 1 –– Bottom) 4-2 Chapter 4 Installation and Wiring DAAGAA 230V Dimensions, Weights and Conduit Entry Locations Nominal Dimensions and Weights in Inches (Millimeters) and Pounds (Kilograms) HP kW Rating Code A B C D E F G H I J K Weight 7�1/2, 10 5.5, 7.5 DAA, EAA 10.63 17.72 8.27 7.87 17.13 1.38 0.30 2.76 2.56 6.31 1.38 30.0 (270) (450) (210) (200) (435) (35) (8) (70) (65) (160) (35) (13.6) 15, 20 11, 15 FAA, GAA 10.63 21.65 8.27 7.87 21.06 1.38 0.30 2.76 2.56 6.31 1.72 43.0 (270) (550) (210) (200) (535) (35) (8) (70) (65) (160) (43.8) (19.5) G 0.28 IN (7.0 MM) DIA. MOUNTING HOLES ADJUSTABLE FREQUENCY AC MOTOR DRIVE E B Hz A I 8 0 0 LOCK SELECT ENTER STOP NO. AI. SHIFT G F D F C A (NEMA Type 1 –– Front) (NEMA Type 1 –– Side) K DIA. CONDUIT ENTRY HOLES J I I H (NEMA Type 1 –– Bottom) 4-3 Chapter 4 Installation and Wiring AABCAB 460V Dimensions, Weights and Conduit Entry Locations Nominal Dimensions and Weights in Inches (Millimeters) and Pounds (Kilograms) HP kW Rating Code A B C D E F G H I J K Weight 3/4, 1 .55, .75 AAB 8.90 11.26 5.31 8.27 10.63 0.30 0.30 2.48 1.97 2.83 1.85 9.0 (226) (286) (135) (210) (270) (8) (8) (63) (50) (72) (47) (4.1) 2 1.5 YAB 8.90 11.26 5.31 8.27 10.63 0.30 0.30 2.48 1.97 2.24 1.26 9.0 (226) (286) (135) (210) (270) (8) (8) (63) (50) (57) (32) (4.1) 3, 5 2.2, 4 BAB, CAB 10.20 13.54 6.90 9.45 12.80 0.30 0.30 3.13 1.97 4.13 2.80 20.0 (259) (344) (175) (240) (325) (8) (8) (80) (50) (105) (71) (9.1) G 0.25 IN (6.35 MM) DIA. MOUNTING HOLES ADJUSTABLE FREQUENCY AC MOTOR DRIVE E Hz B 60.00A LOCK SELECT ENTER STOP NO. LL. SHIFT G F D F C A (NEMA Type 1 –– Front) (NEMA Type 1 –– Side) 0.905 IN (23.0 MM) DIA. CONDUIT ENTRY HOLES J K I I H (NEMA Type 1 –– Bottom) 4-4 Chapter 4 Installation and Wiring ATTENTION: Do not proceed without reading the information General Wiring Procedures on this page. Failure to understand procedures and hazards may ! result in personal injury or equipment damage. 1. The National Electrical Code requires that a circuit breaker or fusible disconnect switch be provided in the drive branch circuit. Providing drive input fusing alone is not sufficient to meet NEC guidelines. The 1333 does not provide this requirement. Selection of a branch circuit breaker or fusible disconnect should be based on the drive input current rating. Refer to the 3-Phase and 1-Phase Power Terminal Block Wiring sections in this chapter for mandatory AC input fusing recommendations for drive short circuit protection. 2. The National Electrical Code requires that motor overload protection be provided in the motor branch circuit. Parameter 6 when used with Parameter 7 provides motor overload protection. NEC however, recognizes this protection as being provided by eutectic alloy or bi-metal overload relays. If it necessary to meet NEC motor branch protection approval, eutectic alloy, bi-metal overload relays or an equivalent should be installed. Refer to article 430 of the NEC and any additional codes for specific requirements and additional information. 3. The National Electrical Code and local regulations govern the installation and wiring of the 1333. All input and output power wiring, control wiring and conduit must be brought through the drive conduit entry holes provided on the enclosure. Connections to the drive must be made as shown in the following sections and in accordance with the drive nameplate, National Electrical Code requirements and any additional interconnection diagrams packed with the drive. 4. The voltage on each phase of the incoming line to the drive must match the drive input rating. Verify the drive rating by referring to the input voltage listed on the drive nameplate. If the incoming line voltage is out of this tolerance, equipment may be damaged or fail to operate. 5. If multiple drives are used, do not use common cabling for AC input or output leads. If multiconductor cable is used, separate 3-conductor input and output cable for each drive must be used. 6. All signal wiring must be run separate from power or control wiring. Verify that shielded cable and/or conduit is used if indicated on any interconnection diagrams or in the following sections. If shielded cable is required, shields must be grounded at the drive end only at one of the drive ground lugs provided. 7. Nearby relays, solenoids or brake coils can produce electrical noise transients and cause erratic drive behavior. Transient suppression networks must be added across the coils of these devices. 8. Since most startup difficulties result from incorrect wiring, every precaution should be taken to assure that the wiring is as indicated on the diagrams and information packed with the drive. 4-5 Chapter 4 Installation and Wiring Wire Group Numbers The following chart identifies general wire categories that will be encountered when installing the 1333 and other AC drives. Each category has an associated wire group number that is used in the following sections to identify the wire to be used. Application and signal examples along with the recommended type of cable for each group is provided. A matrix providing the recommended minimum spacing between different wire groups run in the same tray or separate conduit is also provided. For Tray: Recommended minimum spacing between different wire groups in the same tray For Conduit: Wire Wire Signal Application Recommended Cable Different wire groups must be run in separate conduit Group Category Example Inches and (Millimeters) Wire Power Power Control Control Signal Signal Group 1 2 3 4 5 6 3�Conductor Cable In 9.00 9.00 9.00 9.00 Per NEC Tray (228.6) (228.6) (228.6) (228.6) 2.3 kV, 3j AC Power Local Codes 1 AC Lines (> 600 V AC) and Between 3.00 (76.2) Application Requirements Conduit Between Conduit Power Per NEC In 9.00 9.00 6.00 6.00 Local Codes Tray (228.6) (228.6) (152.4) (152.4) AC Power 480V, 3j¶and 2 (to 600 V AC) Application Between 3.00 (76.2) Requirements Conduit Between Conduit Relay Logic Per NEC In 9.00 6.00 9.00 6.00 115V AC or 115V DC PLC I/O Local Codes Tray (228.6) (152.4) (228.6) (152.4) Logic 3 and Application Power Supplies 115V AC Between 3.00 (76.2) Requirements Instruments Power Conduit Between Conduit Control Per NEC In 9.00 6.00 6.00 9.00 Local Codes Tray (228.6) (152.4) (152.4) (228.6) 24V AC or 24V DC and PLC I/O 4 Logic Application Between 3.00 (76.2) Requirements Conduit Between Conduit Analog Signals 5�24V DC Supplies DC Supplies Belden 8760 Belden 8770 5 Belden 9460 Digital Power Supplies All signal wiring must be run in separate steel conduit. (Low Speed) TTL Logic Level A wire tray is not suitable. Signal The minimum spacing between conduit containing different Digital Pulse Train Belden 8760 wire groups is 3.00 inches (78.2 mm). 6 (High Speed) Input Belden 9460 ¶ Refer to precautions in General Wiring Procedures concerning multi�conductor cables. Belden 8760 � 18 AWG, twisted pair, shielded. Belden 8770 � 18 AWG, 3 conductor, shielded. Belden 9460 � 18 AWG, twisted pair, shielded. Note 1 Steel conduit is recommended for all 1333 power or control wiring and required for all 1333 signal wiring. All input and output power wiring, control wiring or conduit should be brought through the drive conduit entry holes provided. Use appropriate connectors to maintain the environmental rating of the enclosure. Note 2 Spacing between wire groups is the recommended minimum for parallel runs of 200 feet or less. Note 3 All shields for shielded cable must be grounded at the drive end only, at one of the ground terminal lugs provided -- The other end must be insulated and remain floating. Shields for cables from one enclosure to another must be grounded only at the enclosure nearest the drive. If splicing of shielded cables is required, the shield must remain continuous and insulated from ground. Note 4 AC and DC circuits must be run in separate conduit or trays. Note 5 A voltage drop in motor leads may adversely affect motor starting and running performance. Installation and application requirements may dictate larger wire sizes than indicated in the NEC guidelines. 4-6 Chapter 4 Installation and Wiring Terminal Block Power Wiring Important: 1. The 1333 does not provide input power short circuit fusing. Specifications for the recommended fuse size and type to provide drive input power protection against short circuits are provided on the following pages. Branch circuit breakers or disconnect switches cannot provide this level of protection for drive components. 2. Each Bulletin 1333 must have its own dedicated input and output power leads. If multiconductor cable is used, separate 3-conductor input and output cable for each drive must be used. 3. For multimotor operation, the combined total of motor full load current must not exceed the rated output current of the drive. 4. Verify that the motor windings are properly connected to receive the full drive output voltage rating. ATTENTION: 1. Any disconnecting means wired to drive output terminals ! U V W / / and / must be capable of stopping the drive if T1, T2 T3 opened during drive operation. If opened during drive operation, the drive will continue to produce output voltage into an open motor circuit causing a potential shock hazard. 2. The start/stop control circuitry in the 1333 includes solid-state components. If hazards due to accidental contact with moving machinery or unintentional flow of liquid, gas or solids exist, an additional hard wired stop circuit is required to remove AC line power to the drive. When AC input power is removed, there will be a loss of inherent regenerative braking effect and the motor will coast to a stop. An auxiliary braking method may be required. The 1333 is intended to be controlled by control input signals that will start and stop the motor. A device that routinely disconnects then reapplies line power to the drive for the purpose of starting and stopping the motor must not be used. After a hard wired stop has been initiated, allow at least five minutes before reapplying input power to the drive. The allowable number of hard wired start/stops are 1 cycle within a 5 minute period. Wait 5 minutes before attempting the next hard wired stop cycle to allow the drive precharge resistors to cool. Refer to codes and standards applicable to your particular system for specific requirements and additional information. 4-7 Chapter 4 Installation and Wiring 3/45HP (.554kW) Input and output power connections are marked on the drive Power Terminal Block Power Wiring Terminal Block. The Power Terminal Block is an eight position terminal block located at the bottom of the Main Control Board. For maintenance and setup procedures, the drive may be operated without a motor connected. Drive Input Terminals T / L3 S / L2 R / L1 Drive Power Terminal Block Drive Ground Terminals Figure 41 -- 3/45HP (.554kW) Terminal Block Power Wiring 4-8 Chapter 4 Installation and Wiring 71/220HP (5.515kW) Input and output power connections are marked on the drive Power Terminal Block Power Wiring Terminal Block. The Power Terminal Block is an eight position terminal block located at the bottom of the drive. For maintenance and setup procedures, the drive may be operated without a motor connected. Drive Output Terminals W / T3 V / T2 U / T1 Drive Power Terminal Block Drive Ground Terminals Figure 42 -- 71/220HP (5.515kW) Terminal Block Power Wiring 4-9 Chapter 4 Installation and Wiring ZAAEAA 3Phase R/ S/ T/ U/ V/ W/ +BUS -BUS L1 L2 L3 T1 T2 T Power Terminal Block Wiring 3 jA jB jC ¶¶¶ 1333 Dynamic Brake Motor • jA jB jC AC Incoming Line Earth Earth Ground Ground ¶ User supplied drive input fuses. • Motor disconnecting means including branch circuit, short circuit, and ground-fault protection. R/ S/ T/ L1, L2, L3 Input AC line Terminals are not phase sensitive. For drives rated ZAA-EAA, nominal 3-phase input voltage is 200/208/230V AC, 50/60 Hz. For drives rated AAB-CAB, nominal 3-phase input voltage is 380/415/460V AC, 50/60 Hz. Branch disconnect and short circuit protection is not part of the standard 1333 and must be supplied by the user. Drive input fuses are required to provide component protection against malfunction of electronic circuits. U/T1, V/T2, W/T3 Connect the motor leads to these terminals. + BUS, - BUS DC bus terminals are reserved for the 1333 dynamic brake option. Refer to the 1333 dynamic brake option instructions for installation and connection details. GND Two ground terminals have been provided in the drive. Either one of these terminals must be connected to earth ground or the ground of the building electrical system. The motor frame must also be connected to earth ground. Refer to the motor manufacturer’s installation instructions for specific details. 4-10 Chapter 4 Installation and Wiring If You Use 200/208/230V AC, 3Phase Input Voltage 230/208VA.C. CAUTION : Input Voltage Only Use 75 Degree C • AWG Copper Wire Torque to ‚ Lb-in (Power Terminal Block Cover) Power Recommended Rating Wire Wire Recommended Code Group ¶Size • Torque ‚ 2 ZAA 2 14 AWG (2.5mm ) 9 Inlbs (1.02Nm) 2 AAA 2 14 AWG (2.5mm ) 9 Inlbs (1.02Nm) 2 YAA 2 14 AWG (2.5mm ) 9 Inlbs (1.02Nm) 2 BAA 2 12 AWG (4.0mm ) 9 Inlbs (1.02Nm) 2 CAA 2 10 AWG (6.0mm ) 9 Inlbs (1.02Nm) 2 DAA 2 8 AWG (10.0mm ) 10 Inlbs (1.13Nm) 2 EAA 2 8 AWG (10.0mm ) 10 Inlbs (1.13Nm) ¶ Wire group number chart, page 46. Select from the following drive input fuses. Drive Rating ZAA Fuse Size 15AFuse Type 600V Class K5 UL Listed or Equivalent Drive Rating AAA Fuse Size 15AFuse Type 600V Class K5 UL Listed or Equivalent Drive Rating YAA Fuse Size 15AFuse Type 600V Class K5 UL Listed or Equivalent Drive Rating BAA Fuse Size 30AFuse Type 600V Class K5 UL Listed or Equivalent Drive Rating CAA Fuse Size 40AFuse Type 600V Class K5 UL Listed or Equivalent Drive Rating DAA Fuse Size 70AFuse Type 600V Class K5 UL Listed or Equivalent Drive Rating EAA Fuse Size 80AFuse Type 600V Class K5 UL Listed or Equivalent If You Use 380/415/460V AC, 3Phase Input Voltage 460/415/380VA.C. CAUTION : Input Voltage Only Use 75 Degree C • AWG Copper Wire Torque to ‚ Lb-in (Power Terminal Block Cover) Power Recommended Rating Wire Wire Recommended Code Group ¶Size •Torque ‚ 2 AAB 2 14 AWG (2.5mm ) 9 In-lbs (1.02N-m) 2 YAB 2 14 AWG (2.5mm ) 9 In-lbs (1.02N-m) 2 BAB 2 14 AWG (2.5mm ) 9 In-lbs (1.02N-m) 2 CAB 2 14 AWG (2.5mm ) 9 In-lbs (1.02N-m) ¶ Wire group number chart, page 4-6. Select from the following drive input fuses. Drive Rating AABFuse Size 15AFuse Type 600V Class K5 UL Listed or Equivalent Drive Rating YABFuse Size 15AFuse Type 600V Class K5 UL Listed or Equivalent Drive Rating BABFuse Size 15AFuse Type 600V Class K5 UL Listed or Equivalent Drive Rating CABFuse Size 20AFuse Type 600V Class K5 UL Listed or Equivalent 4-11 Chapter 4 Installation and Wiring FAA or GAA 3Phase Power Terminal Block Wiring GND R/ S/ T/ U/ V/ W/ GND +BUS -BUS L L L T T T 1 2 3 1 2 3 Earth Earth Ground Ground jA jB jC¶¶¶ 1333 Motor Dynamic Brake • jA jC jB AC Incoming Line ¶ User supplied drive input fuses. ¶ Motor disconnecting means including branch circuit, short circuit, and ground-fault protection. R/ S/ T/ L1, L2, L3 Input AC line Terminals are not phase sensitive. For drives rated FAA or GAA, nominal 3-phase input voltage is 200/208/230V AC, 50/60 Hz. Branch disconnect and short circuit protection is not part of the standard 1333 and must be supplied by the user. Drive input fuses are required to provide component protection against malfunction of electronic circuits. U/ V/ W/ T1, T2, T3 Connect the motor leads to these terminals. + BUS, - BUS DC bus terminals are reserved for the 1333 dynamic brake option. Refer to the 1333 dynamic brake option instructions for installation and connection details. GND Two ground terminals have been provided in the drive. Either one of these terminals must be connected to earth ground or the ground of the building electrical system. The motor frame must also be connected to earth ground. Refer to the motor manufacturer’s installation instructions for specific details. 4-12 Chapter 4 Installation and Wiring If You Use FAA or GAA Units Lugs are required to terminate wires for FAA or GAA units at the Power Terminal Block. 230/208VA.C. CAUTION : Input Voltage Only Use 75 Degree C • AWG Copper Wire Use U.L. Listed Crimp Connectors ‚ (Power Terminal Block Cover) Power Recommended Rating Wire Wire Code Group ¶Size • 2 FAA 2 6 AWG (16.0mm ) 2 GAA 2 3 AWG (30.0mm ) ¶Wire group number chart, page 46. ‚UL Listed crimp connectors are required and must be installed using the proper crimping tool. Crimp connectors must be sized to the wire size chosed. When using crimp connectors on terminal studs that are not isolated from each other, a minimum spacing of 0.4 Inches (10.16mm) is required. Select from the following drive input fuses. Drive Rating FAA Fuse Size 100AFuse Type 600V Class K5 UL Listed or Equivalent Drive Rating GAA Fuse Size 125AFuse Type 600V Class K5 UL Listed or Equivalent 4-13 Chapter 4 Installation and Wiring ZAAEAA 1Phase R/ S/ T/ U/ V/ W/ +BUS -BUS L1 L2 L3 T1 T2 T Power Terminal Block Wiring 3 jA jB jC ¶¶ 1333 Motor Dynamic Brake • AC Incoming Line Earth Earth Ground Ground ¶ User supplied drive input fuses. • Motor disconnecting means including branch circuit, short circuit, and ground-fault protection. S/ and T/ L2 L3 Input AC line Terminals are not phase sensitive. For drives rated ZAA-EAA, nominal 1-phase input voltage is 200/208/230V AC, 50/60 Hz. Branch disconnect and short circuit protection is not part of the standard 1333 and must be supplied by the user. Drive input fuses are required to provide component protection against malfunction of electronic circuits. U/ V/ W/ T1, T2, T3 Connect the motor leads to these terminals. + BUS, - BUS DC bus terminals are reserved for the 1333 Dynamic Brake Option. Refer to the 1333 Dynamic Brake Option instructions for installation and connection details. GND Two ground terminals have been provided in the drive. Either one of these terminals must be connected to earth ground or the ground of the building electrical system. The motor frame must also be connected to earth ground. Refer to the motor installation instructions for specific details. 4-14 Chapter 4 Installation and Wiring If You Use 200/208/230V AC, 1Phase Input Voltage 230/208VA.C. CAUTION : Input Voltage Only Use 75 Degree C • AWG Copper Wire Torque to ‚ Lb-in (Power Terminal Block Cover) Power Recommended Rating Wire Wire Recommended Code Group ¶Size • Torque ‚ 2 ZAA 2 14 AWG (2.5mm ) 9 In-lbs (1.02N-m) 2 AAA 2 14 AWG (2.5mm ) 9 In-lbs (1.02N-m) 2 YAA 2 14 AWG (2.5mm ) 9 In-lbs (1.02N-m) 2 BAA 2 12 AWG (4.0mm ) 9 In-lbs (1.02N-m) 2 CAA 2 10 AWG (6.0mm ) 9 In-lbs (1.02N-m) 2 DAA 2 8 AWG (10.0mm ) 10 In-lbs (1.13N-m) 2 EAA 2 8 AWG (10.0mm ) 10 In-lbs (1.13N-m) • Wire group number chart, page 4-6. Select from the following drive input fuses. Drive Rating ZAA Fuse Size 15AFuse Type 600V Class K5 UL Listed or Equivalent Drive Rating AAA Fuse Size 15AFuse Type 600V Class K5 UL Listed or Equivalent Drive Rating YAA Fuse Size 15AFuse Type 600V Class K5 UL Listed or Equivalent Drive Rating BAA Fuse Size 30AFuse Type 600V Class K5 UL Listed or Equivalent Drive Rating CAA Fuse Size 40AFuse Type 600V Class K5 UL Listed or Equivalent Drive Rating DAA Fuse Size 70AFuse Type 600V Class K5 UL Listed or Equivalent Drive Rating EAA Fuse Size 80AFuse Type 600V Class K5 UL Listed or Equivalent 4-15 Chapter 4 Installation and Wiring FAA or GAA 1Phase Power Terminal Block Wiring GND R/ S/ T/ U/ V/ W/ GND +BUS -BUS L L L T T T 1 2 3 1 2 3 Earth Earth Ground Ground jA jB jC¶¶ 1333 Motor Dynamic Brake• AC Incoming Line ¶ User supplied drive input fuses. • Motor disconnecting means including branch circuit, short circuit, and ground-fault protection. S/ and T/ L2 L3 Input AC line Terminals are not phase sensitive. For drives rated FAA or GAA, nominal 1-phase input voltage is 200/208/230V AC, 50/60 Hz. Branch disconnect and short circuit protection is not part of the standard 1333 and must be supplied by the user. Drive input fuses are required to provide component protection against malfunction of electronic circuits. U/ V/ W/ T1, T2, T3 Connect the motor leads to these terminals. + BUS, - BUS DC bus terminals are reserved for the 1333 Dynamic Brake Option. Refer to the 1333 Dynamic Brake Option instructions for installation and connection details. GND Two ground terminals have been provided in the drive. Either one of these terminals must be connected to earth ground or the ground of the building electrical system. The motor frame must also be connected to earth ground. Refer to the motor installation instructions for specific details. 4-16 Chapter 4 Installation and Wiring If You Use FAA or GAA Units Lugs are required to terminate wires for FAA or GAA units at the Power Terminal Block. 230/208VA.C. CAUTION : Input Voltage Only Use 75 Degree C • AWG Copper Wire Use U.L. Listed Crimp Connectors ‚ (Power Terminal Block Cover) Power Recommended Rating Wire Wire Code Group ¶Size • 2 FAA 2 6 AWG (16.0mm ) 2 GAA 2 3 AWG (30.0mm ) ¶Wire group number chart, page 46. ‚UL Listed crimp connectors are required and must be installed using the proper crimping tool. Crimp connectors must be sized to the wire size chosed. When using crimp connectors on terminal studs that are not isolated from each other, a minimum spacing of 0.4 Inches (10.16mm) is required. Select from the following drive input fuses. Drive Rating FAA Fuse Size 100AFuse Type 600V Class K5 UL Listed or Equivalent Drive Rating GAA Fuse Size 125AFuse Type 600V Class K5 UL Listed or Equivalent 4-17 Chapter 4 Installation and Wiring Control and Signal Wiring The Control and Signal Wiring Terminal Block is located at the bottom of Terminal Block the Control Board. The Control and Signal Wiring Terminal Block is a twenty-four position terminal block with markings of 1 to 24. The drive is capable of operating from the Local Control and Programming Panel without any external control or signal connections provided the factory installed jumper at terminals 16 and 17 is installed. When required, external operator elements may be connected to provide remote control of the drive. Several additional drive control functions and status outputs are also available for use at this terminal block. Drive Control Board Switches SW2 SW1 Drive Control and Signal Wiring Terminal Block Drive Ground Terminals Figure 43 -- 3/45HP (.554kW) Control and Signal Wiring Terminal Block 4-18 Chapter 4 Installation and Wiring Drive Control Board Switches SW2 SW1 Drive Control and Signal Wiring Terminal Block Drive Ground Terminals Figure 44 -- 71/220HP (5.515kW) Control and Signal Wiring Terminal Block 4-19 Chapter 4 Installation and Wiring Figure 45 -- Control and Signal Wiring Terminal Block Interconnection Diagram SW1 SW2 Factory 1mA 4SP Logic Set to Common 4SP CR1 CR2 CR3 CR3 10V 8SP 1 2 3 4 5 6 7 8 9 10 11 1213 141516 1718 19 20 21 22 23 24 Drive Start Stop Rev Jog S1 S2 Factory End Installed Shield Jumper Pot CR1 CR2 CR3 CR3 Pot Wiper Pot Programmable Outputs Fault Contacts High Low Drive Input Power Applied Drive Input Power Applied Start/Stop No Output Signal Present No Fault Present SW2 set to 4SP 3Wire Control Aux Reset - + Interlock Lockout 05V External S1 010V Stop Speed Pot - + Start 4-20mA 2Wire Control S2 + - Analog Meter Earth S3 Ground 1mA Maximum when SW1 set to 1mA 10V Maximum when SW1 set to 10V SW2 set to 8SP Input Signal Recommended Recommended Terminals Input Signal Wire Group ¶Wire Size Torque 2 Terminals 1, 2, 3 External Speed Potentiometer 5 16 AWG (1.5mm ) 7 InLbs (.791 Nm) 2 Terminals 3, 8, 11 and 17 Logic Common 5 16 AWG (1.5mm ) 7 InLbs (.791 Nm) 2 Terminals 4 and 3 05 or 010V DC 5 16 AWG (1.5mm ) 7 InLbs (.791 Nm) 2 Terminals 5 and 3 420mA 5 16 AWG (1.5mm ) 7 InLbs (.791 Nm) 2 Terminals 7 and 8 Start 5 16 AWG (1.5mm ) 7 InLbs (.791 Nm) 2 Terminals 9 and 8 Stop 5 16 AWG (1.5mm ) 7 InLbs (.791 Nm) 2 Terminals 10 and 11 Reverse 5 16 AWG (1.5mm ) 7 InLbs (.791 Nm) 2 Terminals 12 and 11 Jog 5 16 AWG (1.5mm ) 7 InLbs (.791 Nm) 2 Terminals 13 and 14 S1/4SP Position 5 16 AWG (1.5mm ) 7 InLbs (.791 Nm) 2 Terminals 14 and 15 S2/4SP Position 5 16 AWG (1.5mm ) 7 InLbs (.791 Nm) 2 Terminals 11 and 13 S1/8SP Position 5 16 AWG (1.5mm ) 7 InLbs (.791 Nm) 2 Terminals 11 and 14 S2/8SP Position 5 16 AWG (1.5mm ) 7 InLbs (.791 Nm) 2 Terminals 11 and 15 S3/8SP Position 5 16 AWG (1.5mm ) 7 InLbs (.791 Nm) 2 Terminals 16 and 17 Auxiliary Interlock 5 16 AWG (1.5mm ) 7 InLbs (.791 Nm) 2 Terminals 17 and 18 Reset Lockout 5 16 AWG (1.5mm ) 7 InLbs (.791 Nm) Output Signal Recommended Recommended Terminals Output Signal Wire Group ¶Wire Size Torque 2 Terminal 6 and Logic Common 01mA or 010V Meter 5 16 AWG (1.5mm ) 7 InLbs (.791 Nm) 2 Terminals 19 and I20 CR1 Programmable Contact 3 16 AWG (1.5mm ) 7 InLbs (.791 Nm) 2 Terminals 20 and 21 CR2 Programmable Contact 3 16 AWG (1.5mm ) 7 InLbs (.791 Nm) 2 Terminals 22 and 23 CR3 Fault Contact 3 16 AWG (1.5mm ) 7 InLbs (.791 Nm) 2 Terminals 23 and 24 CR3 Fault Contact 3 16 AWG (1.5mm ) 7 InLbs (.791 Nm) ¶ Wire group number chart, page 46. 4-20 Chapter 4 Installation and Wiring Important: Control and signal functions affected by drive parameter selection and programming are indicated on the following pages. Refer to the Programming section in Chapter 5 for detailed parameter operating descriptions. Terminals 1, 2 and 3 These terminals are provided for connecting a remote 10kΩ, 2W potentiometer. To enable a potentiometer to be connected to these terminals, Parameter 9 must be set to 1, 2 or 3. The potentiometer frequency control range is the range between minimum and maximum drive frequency as set by Parameters 15, 16, 50, 51, 53 and/or 54. The frequency resolution is 0.1 Hz up to 100 Hz, 0.2 Hz up to 200 Hz, and 0.5 Hz if over 200 Hz. Terminal 1 Potentiometer High Full CW or high side external potentiometer connection. Terminal 2 Potentiometer Wiper Wiper external potentiometer connection. Terminal 3 Potentiometer Low Full CCW or low side external potentiometer connection. Terminals 3, 8, 11, and 17 Logic Common These terminals are provided to terminate both minus and drive common signals to the Control and Signal Wiring Terminal Block. Terminals 4 and 3 05 or 010VDC This terminal is provided to terminate a 0 to +5 or +10V DC speed reference signal. The minus signal is terminated at Logic Common. Parameter 9 enables the speed reference signal and selects either a 0-5V input signal (when set to 1), or a 0-10V input signal (when set to 2). Parameters 52, 53 and 54 sets the output signal to be either directly or inversely proportional. The input impedance from Terminal 4 to logic common is approximately 40kΩ. The range of frequency control is between the minimum and maximum drive frequency settings or frequency clamps as set by Parameters 15, 16, 50, 51, 53 and/or 54. The frequency resolution is 0.1 Hz up to 100 Hz, 0.2 Hz up to 200 Hz, and 0.5 Hz if over 200 Hz. 4-21 Chapter 4 Installation and Wiring ATTENTION: Unexpected machine acceleration can cause injury or death. ! If Parameter 9 is set to a value other than 0, a loss of the potentiometer low reference signal at terminal 3 of the drive terminal block will allow the drive to immediately accelerate to maximum frequency if the drive is running or a start command has been received. Ensure that remote potentiometer connection integrity is maintained and inspected in accordance with NFPA 70B standards for maintenance of electrical equipment. ATTENTION: Terminals 4, 5 and 6 are internally protected from reverse polarity signals or input signals rising above 120% of the ! maximum input signal. If reverse polarity or levels are maintained above 120%, signals may be degraded and component damage may result. Terminals 5 and 3 420mA Input This terminal is provided to terminate a +4 to 20 mA DC speed reference signal. The minus signal is terminated at Logic Common. Parameter 9 enables and selects the 4-20mA input signal. Parameters 52, 53 and 54 sets the input signal to be either directly or inversely proportional. The input impedance from Terminal 5 to logic common is approximately 390Ω. The range of frequency control is between the minimum and maximum drive frequency settings or frequency clamps. The frequency resolution is 0.1 Hz up to 100 Hz, 0.2 Hz up to 200 Hz, and 0.5 Hz if over 200 Hz. Terminals 6 and 3 Analog Meter Output This terminal provides a 0-1mA or 0-10V DC signal that may be used with a user supplied analog meter. The minus signal is terminated at logic common. Switch SW1, a 1mA/10V switch on the Control Board, sets the output signal to either 0-1mA or 0-10V. For a 0–1mA voltage output, the load impedance of the meter must be 10kΩ or less. For a 0–10V voltage output, the load impedance of the meter must be 300Ω or less. Parameter 55 is used to set the 1mA output signal to equal 75-125% of maximum output frequency while the drive is running. Parameter 56 is used to adjust the 10V to equal 75-125% of maximum output frequency while the drive is running. 4-22 Chapter 4 Installation and Wiring Terminals 7 and 8 Start This remote input will command the drive to start if all hardwired interlocks are closed and Parameter 8 is set to 1 or 3. The drive will continue to run until a stop command is received, an interlock is opened, or a fault is detected. Important: As shown in Figure 4-4, for external two wire start/stop control, terminals 7 and 8 must be jumpered. Terminals 9 and 8 Stop This remote input will command the drive to stop if Parameter 8 is set to 1 or 3. The drive will then either ramp-to-stop or coast-to-stop as selected by Parameter 11. Important: If ramp-to-stop is selected, refer to Parameters 11 and 18 if the drive will be subjected to an overhauling load. If Parameter 18 Decel Frequency Hold is set to 1 (On), an overhauling load may cause the decel ramp to hold at one frequency for an extended period, causing ramp-to-stop commands to appear to be non-functional. Terminals 10 and 8 Reverse This remote input will command the drive to reverse direction if Parameter 8 is set to 1 or 3 and Parameter 10 is set to 0. Both the local and remote reverse will be locked out if Parameter 10 is set to 1. Terminals 12 and 11 Jog This remote input will jog the drive if Parameter 8 is set to 1 or 3. When jogged: –– The drive will jog to the frequency range set by Parameter 26 –– Within the accel time set by Parameter 27 –– In the direction determined by Parameter 10. When the jog pushbutton is released, the drive will decelerate within the time set by Parameter 28. 4-23 Chapter 4 Installation and Wiring Terminals 13 and 14 -- S1/4SP Terminals 15 and 14 -- S2/4SP Switch SW2 on the Control Board is factory set to 4SP. When set to 4SP, two external switches may be connected to the drive as shown in Figure 4-3. In addition to the standard accel and decel rates set by Parameters 1 and 2, these switches may then be used to select; –– Three additional accel rates –– Four preset speeds As programmed by Parameters 19, 29-31 and 36-41. Terminals 13 and 11 -- S1/8SP Terminals 14 and 11 -- S2/8SP Terminals 15 and 11 -- S3/8SP When switch SW2 on the Control Board is set to 8SP, a total of three external switches may be connected to the drive as shown in Figure 4-3. In addition to the standard accel and decel rates set by Parameters 1 and 2, these switches may then be used to select three additional accel rates, three additional decel rates, and seven preset speeds, as programmed by Parameters 19-20 and 29-41. Important: If parameter 20 is set to 1, switch S1 and S2 will select the four preset speeds defined by Parameters 29-31. Switch S3 is reserved for remotely setting a drive fault. Terminals 16 and 17 Auxiliary Interlock These factory jumpered terminals are used to install an auxiliary external interlock when the jumper is removed. The interlock contact must be closed to allow the drive to operate. The contact must be open for a minimum of 100mS to sense an auxiliary fault. Parameter 21 will allow an open contact to generate either: A no-fault coast-to-stop sequence displaying AS –– Auxiliary Stop. A drive fault coast-to-stop sequence displaying AU –– Auxiliary Interlock –– which will cause the CR3 fault contacts to change state. Important: A 5V DC or 5mA signal requires a gold contact relay. 4-24 Chapter 4 Installation and Wiring Terminals 18 and 17 Reset Lockout These terminals may be jumpered or not jumpered to determine how the 1333 is reset after a fault. When the terminals are jumpered, a drive may only be reset and restarted by removing then re-applying input power to the drive. When these terminals are left open, the drive will be reset and restarted as programmed by Parameters 47 and 48. Terminals 19 and 20 Programmable Contact CR1 These terminals allow drive supplied relay contact CR1 to be used in external circuits. When power is applied to the drive, the N.O. contact will remain N.O. until a programmed signal is received. The contact is programmed by Parameters 22 and 24 to signal that the drive is at the programmed set speed or 140% of rated drive current. The contact is isolated from Logic Common and other drive circuitry. CR1 CR1 19 20 19 20 CR1 Out CR1 Out Programmed Signal At Set Speed or Not Present 140% of Rated Drive Current Resistive rating: 120V AC or 30V DC, 1 Amp. Inductive rating: 120V AC or 30V DC, 0.5 Amps. 4-25 Chapter 4 Installation and Wiring Terminals 21 and 20 Programmable Contact CR2 These terminals allow drive supplied relay contact CR2 to be used in external circuits. When power is applied to the drive, the N.O. contact will remain N.O. until a programmed signal is received. The contact is programmed by Parameters 23 and 25 to signal that the drive is at the programmed set speed or 140% of rated drive current. The contact is isolated from Logic Common and other drive circuitry. CR2 CR2 20 21 20 21 CR2 Out CR2 Out Programmed Signal Running, At Set Speed, or Not Present 140% of Rated Drive Current Resistive rating: 120V AC or 30V DC, 1 Amp. Inductive rating: 120V AC or 30V DC, 0.5 Amps. Terminals 22 and 23 Terminals 24 and 23 Fault Contacts -- CR3 These terminals allow drive supplied CR3 relay contacts to be used in external circuits. The contacts are shown with power applied to the drive. When power is first applied to the drive, the contacts will change state –– 22 to 23 will close, 23 to 24 will open. Should a fault occur 22 to 23 will open, 23 to 24 will close. The contacts are isolated from Logic Common and other drive circuitry. CR3 CR3 CR3 CR3 22 23 24 22 23 24 CR3 Out CR3 Out CR3 Out CR3 Out Drive Not Faulted Drive Faulted Resistive rating: 120V AC or 30V DC, 1 Amp. Inductive rating: 120V AC or 30V DC, 0.5 Amps. 4-26 Chapter 5 Operation and Programming Local Control and The Local Control and Programming Panel provides a convenient means to Programming Panel locally control the operating functions of the Series D Bulletin 1333 drive including start/stop, forward/reverse, and speed. The Local Control and Programming Panel also contains two digital displays. A Main Display to show drive running values, codes, and parameter values, and a Mode Display to show the drive mode and control source. Finally, the Local Control and Programming Panel includes the controls necessary to program the various parameters that will define your drive. Figure 51 -- The Bulletin 1333 Series D With two exceptions, the drive must always be stopped to allow drive programming. • A 0-1 mA Analog Output Meter may be calibrated while the drive is running by accessing Parameter 55. • A 0-10V DC Analog Output Meter may be calibrated while the drive is running by accessing Parameters 56. 5-1 Chapter 5 Operation and Programming The Controls The Main Display Hz LED Alternate The Select LED Pushbutton The Lock The Enter Switch Pushbutton The Stop Pushbutton The Directional Start Pushbutons The Mode The The The Shift Display Increment Decrement Pushbutton Pushbutton Pushbutton Figure 52 -- Bulletin 1333 Series D Controls The Select Pushbutton In the Programming Mode is used to toggle between the parameter number and the parameter value. In the Monitoring and Operating Mode is used to select the mode to be monitored. • Drive parameters. • Drive output frequency. • One of three alternate running displays. The Lock Switch is used to switch between the Programming Mode and the Monitoring Mode. 5-2 Chapter 5 Operation and Programming The Directional Start Pushbuttons In the Programming Mode are not functional. In the Monitoring and Operating Mode are used to start or jog the drive whenever drive speed is controlled from the Local Control Panel. The Increment and Decrement Pushbuttons In the Programming Mode are used to select parameters or increase and decrease parameter values. In the Monitoring and Operating Mode are used to increment or decrement drive speed whenever drive speed is controlled from the Local Control Panel. The Shift Pushbutton In the Programming Mode is used to shift between display segments in both the Main and Mode Displays. In the Monitoring and Operating Mode is used to shift between segments in the Main display, or between jog and run in the Mode display when the drive is stopped. The Stop Pushbutton In the Programming Mode is not functional. In the Monitoring and Operating Mode will always stop the drive as described in The Displays section that follows. The Enter Pushbutton In the Programming Mode is used to enter the parameter value. In the Monitoring and Operating Mode is used to enter changes. • Enter changes in drive speed whenever drive speed is controlled from the Local Control Panel. • Enter adjustment values to calibrate a 0-1 mA or 0-10V DC analog output meter. 5-3 Chapter 5 Operation and Programming The Displays The Main Display In the programming mode this display will show the current value of the parameter selected, flash when the value is being changed, and finally remain steady once the new value is entered. Neither the Hz nor Alternate LED will be lit in the programming mode. In the monitoring and operating mode this display can be toggled to show four operational modes. Either the Hz or Alternate LED will be lit or will flash to indicate the monitoring or operational mode. Your are: • Monitoring drive output frequency when the Hz LED is lit. • Changing drive output frequency when the Hz LED is flashing. • Monitoring drive output current or equivalent motor RPM when the Alternate LED is lit. • Monitoring drive output parameters or viewing preset parameter value when no LED is lit. Should a drive operating error occur while the drive is running, OP will be shown. Should the drive receive an auxiliary stop while the drive is running, A5 will be shown. Should a fault occur at any time, the Main Display will shown one of seven faults that can be stored in drive memory. 1. OC A drive overcurrent or ground fault. 2. OL A drive overload fault. 3. OU A drive overvoltage fault. 4. AU A drive auxiliary interlock fault. 5. LU A drive low voltage fault. 6. OH A drive overtemperature fault. 7. CPUAn internal software communications error. 5-4 Chapter 5 Operation and Programming The Mode Display In the programming mode the smaller two-digit display shows the parameter number selected –– 01 to 62. Whenever the drive is in the programming mode, three display items will change. 1. The display will flash. 2. The decimal point normally shown in the lower right hand corner will disappear. 3. Neither the Hz nor Alternate LED in the Main Display will be lit. In the monitoring and operating mode the smaller two-digit display shows the monitoring mode selected –– • 01 62 View drive parameters. • AO Monitor drive output current. • A1 View equivalent motor RPM. • A2 Monitor drive control frequency. • LL, LE, LJ, EE, EL or EJ The local or remote control source currently controlling the drive. LL To indicate: 1. Drive start, jog, speed and forward/reverse is controlled from the Local Control Panel. 2. The Local Control Panel stop pushbutton will stop the drive as programmed by Parameters 11-14. 3. An auxiliary interlock wired to the Control and Signal Wiring Terminal Block will stop the drive and display either AU or A5, as set by Parameter 21. LE To indicate: 1. Drive start, jog and forward/reverse is controlled from the Local Control Panel. 2. The Local Control Panel stop pushbutton will stop the drive as programmed by Parameters 11-14. 3. Drive speed is controlled from a remote reference signal wired to the Control and Signal Wiring Terminal Block. 4. An external stop signal wired to the Control and Signal Wiring Terminal Block will allow the drive to coast-to-stop and display OP. 5-5 Chapter 5 Operation and Programming 5. An auxiliary interlock wired to the Control and Signal Wiring Terminal Block will stop the drive and display either AU or A5, as set by Parameter 21. LJ To indicate the local jog function has been selected. EE To indicate: 1. Drive start, jog, speed and forward/reverse is controlled by external devices or logic wired to the Control and Signal Wiring Terminal Block. 2. An external stop signal wired to the Control and Signal Wiring Terminal Block will stop the drive as programmed by Parameters 11-14. 3. An auxiliary interlock wired to the Control and Signal Wiring Terminal Block will stop the drive and display either AU or A5, as set by Parameter 21. 4. The Local Control Panel stop pushbutton will allow the drive to coast-to-stop and display OP. EL To indicate: 1. Drive start, jog and forward/reverse is controlled by external devices or logic wired to the Control and Signal Wiring Terminal Block. 2. Drive speed is controlled from the Local Control Panel. 3. An external stop signal wired to the Control and Signal Wiring Terminal Block will stop the drive as programmed by Parameters 11-14. 4. The Local Control Panel stop pushbutton will allow the drive to coast-to-stop and display OP. 5. An auxiliary interlock wired to the Control and Signal Wiring Terminal Block will stop the drive and display either AU or A5, as set by Parameter 21. EJ To indicate an external jog signal is being sent. 5-6 Chapter 5 Operation and Programming Programming the Drive 62 parameters are available for adjusting the drive. All Series D 1333 parameters interact with each other to provide optimum drive performance. Some specific parameters however, require that other parameters be set to coordinated values if they are to function. Others require that they be set to specific values to function with Bulletin 1333 options. All parameters along with a detailed explanation are listed in the remaining pages of this chapter. Parameters are grouped under sub-headings by function, such as Accel and Decel Settings or VoltsperHertz Curve Settings. An interactive matrix has been provided in Appendix C to graphically show which parameters must be set to provide coordinated control of the Bulletin 1333. 5-7 Chapter 5 Operation and Programming Accel and Decel Settings Parameter 01 -- Acceleration Time 1 Units = Seconds Range = 0000/1600 Factory Setting = 005.0 This parameter determines the time that it will take the drive to accelerate over a 60 Hz change in frequency. From 0 to 0.5 Hz, the accel rate is effectively zero. From 0.5 Hz to maximum output frequency, the accel rate set by Parameter 1 will remain constant. The total time it will take the drive to accelerate from 0 to maximum drive output frequency is: Total time = (Maximum Drive Output Frequency × Parameter 1) ÷ 60. If set to 0000, the drive will enter 40 ms but display 0000. From 00.10-1000 seconds, this parameter sets the accel time value in 0.1 second increments. From 1000-1600 seconds, this parameter sets the accel time value in 1 second increments. Output Frequency 120 Hz Output Frequency Output Frequency 60 Hz 60 Hz 60 Hz 50 Hz 50 Hz 50 Hz 0.5 0.5 0.5 Parameter 1 Parameter 1 Parameter 1 0 Time 0 Time 0 Time 40mS 40mS 40mS Parameter 3 = 50Hz Parameter 3 = 60Hz Parameter 3 = FF Parameter 15 = 120Hz Accel Settings 5-8 Acceleration Acceleration Acceleration Deceleration Deceleration Deceleration Chapter 5 Operation and Programming Parameter 02 -- Deceleration Time 1 Units = Seconds Range = 0000 to 1600 Factory Setting = 005.0 Important: Parameter 11 must be set to 0 to allow the drive to ramp-to-stop This parameter determines the time that it will take the drive to decelerate and ramp-to-stop over a 60 Hz change in frequency. From 0.5 to 0 Hz, the accel rate is non-linear and set by either DC injection braking or the DC dynamic brake if it is installed. From maximum output frequency to 0.5 Hz, the accel rate set by Parameter 2 will remain constant. The total time it will take the drive to decelerate from maximum drive output frequency to 0.5 Hz is: Total time = (Maximum Drive Output Frequency × Parameter 2) ÷ 60. If set to 0000, the drive will enter 40 ms but display 0000. From 00.10-1000 seconds, this parameter sets the decel time value in 0.1 second increments. From 1000-1600 seconds, this parameter sets the decel time value in 1 second increments. Output Frequency Output Frequency Output Frequency 60 Hz 60 Hz 60 Hz 50 Hz 50 Hz 50 Hz ˚˚˚ 0.5 0.5 0.5 Parameter 2 Parameter 2 Parameter 2 0 Time 0 Time 0 Time 40mS 40mS 40mS Parameter 3 = 50Hz Parameter 3 = 60Hz Parameter 3 = FF Parameter 15 = 120Hz ˚ DC injection braking or DC dynamic braking (if installed). Decel Settings 5-9 Chapter 5 Operation and Programming VoltsperHertz Curve Settings Important: The maximum allowable drive output frequency will be determined by the lowest programmed value of any of the following parameters: • Parameter 3 Frequency Range • Parameter 15 Maximum Frequency • Parameter 51 Upper Frequency Clamp • Parameter 53 Bias Frequency –– If Parameter 53 is Higher Than Parameter 54 • Parameter 54 Gain Frequency –– If Parameter 54 is Higher Than Parameter 53 Parameter 03 -- Frequency Range Units = Code Range = 50, 60 or FF Factory Setting =60 This parameter permits the selection of three linear volts-per-Hertz ramps. The maximum frequency settings of these ramps are 50 Hz, 60 Hz, or FF. If the BCD Interface option is installed, Parameter 3 must be set to match the scaling jumper on the BCD Interface Board –– Either 60 for 60 Hz operation, or FF for 120/200 Hz operation. If set to 50, 50 Hz will be the maximum drive frequency –– The absolute maximum output speed that the drive can reach. If set to 60, 60 Hz will be the maximum drive frequency –– The absolute maximum output speed that the drive can reach. Parameter 15 will have no effect on maximum output speed, but Parameter 51 will. When Parameter 3 is set to 50 or 60, the drive will use the lower of the values set by Parameter 3 and 51. Parameter 16 will have no effect on base speed. If set to FF, the value set by Parameter 15 or 51 will be the maximum drive frequency –– The absolute maximum output speed that the drive can reach. When Parameter 3 is set to FF, the drive will use the lower of the values set by Parameters 15 and 51. The value set by Parameter 16 Base Frequency will be the point where maximum output voltage is applied to the motor. Important: Applications where volts-per-Hertz curves are required to reach maximum voltage other than at 50 or 60 Hz are primarily provisions for operating custom motors. For application assistance in these special ranges, contact your nearest Allen-Bradley representative. 5-10 Chapter 5 Operation and Programming Parameter 04 -- Volts-per-Hertz Curve Units = Code Range = 0/1 Factory Setting =0 This parameter sets the shape of the volts-per-Hertz ramp, either constant or curved. If set to 0, the volts-per-Hertz ramp will be linear producing a constant rate of increase from 0 to base frequency. This setting will be the setting required for most constant torque applications. If set to 1, the volts-per-Hertz ramp will be curved, producing a rate of increase that will gradually curve upward as it increases from 0 to base frequency. This setting will be required for most variable torque applications where full rated motor torque is not required at reduced speeds. Output Voltage Output Voltage 100% 100% Parameter 4 = 0 Parameter 4 = 1 Parameter 5 Parameter 5 DC Boost DC Boost Output Output 0% 0% Frequency Frequency 0 Hertz Parameter 3 0 Hertz Parameter 3 VoltsperHertz Curve Settings + DC Boost Settings DC Boost Settings Parameter 05 -- DC Boost Select Units = % of Output Voltage Range = 00/40 Factory Setting = 00 This parameter adds from 0 to 40% of the drive output voltage to the motor at low drive frequencies in 1% increments, boosting motor torque at startup. DC boost can be added to any volts-per-Hertz curve. The optimum DC boost setting is the lowest level that will permit satisfactory starting torque for the motor and drive. Higher than optimum boost may produce unnecessary motor current at low frequencies and contribute to motor overheating. Excessive boost may even force the drive into an overcurrent condition. 5-11 Chapter 5 Operation and Programming Overload Protection Settings Important: Parameters 6 and 7 are intended for use on single motor applications. For multiple motor applications, Parameter 6 must be set to 0 to help avoid nuisance tripping. Parameter 06 -- Motor Duty Units = Code Range = 0/1/2/3 Factory Setting =2 Parameter 6 provides three thermal overload functions. When used in conjunction with Parameter 7, a thermal overload function that matches the motor nameplate amps can be used. If set to 0, the overload function will not include thermal protection and the drive will trip at its standard setting of 140% of rated drive output current after 60 seconds. If set to 1, 2 or 3, the thermal overload function is enabled and will function as described below. If set to 1, the drive will trip at 115% of the current set in Parameter 7, or 140% of rated drive output current (whichever is lower) after 60 seconds. When set to 1, the thermal overload trip point is constant across the entire speed range of the motor. This performance is typical with A-B Bulletin 1329 10:1 speed range motors. If set to 2, the drive will trip at 115% of the current set in Parameter 7, or 140% of rated drive output current (whichever is lower) after 60 seconds. When set to 2, the thermal overload curve generated is derated below 50 Hz for use with motors having a 4:1 speed range. This performance is typical with A-B Bulletin 1329 4:1 speed range motors. If set to 3, the drive will trip at 115% of the current set in Parameter 7, or 140% of rated drive output current (whichever is lower) after 60 seconds. When set to 3, the thermal overload curve generated is derated below 15 Hz for use with motors having a 4:1 speed range. This performance is typical with A-B Bulletin 1329 4:1 speed range motors. Important: The National Electrical Code requires that motor overload protection be provided in the motor branch circuit. Parameter 6 when used with Parameter 7 provides motor overload protection. NEC however, recognizes this protection as being provided by eutectic alloy or bi-metal overload relays. If it necessary to meet NEC motor branch protection approval, eutectic alloy, bi-metal overload relays or an equivalent should be installed. Refer to article 430 of the NEC and any additional codes for specific requirements and additional information. 5-12 Chapter 5 Operation and Programming % of Current 140% of Rated Drive Output Current 115% of Parameter 7 Overload Protection 0 Hz 0 25 Hz 50 Hz 60 Hz Maximum Frequency Parameter 6 = 1 % of Current 140% of Rated Drive Output Current 115% of Parameter 7 104% of Parameter 7 96% of Rated Drive Output Current 69% of Parameter 7 84% of Rated Drive Output Current Overload Protection 0 Hz 0 25 Hz 50 Hz 60 Hz Maximum Frequency Parameter 6 = 2 % of Current 140% of Rated Drive Output Current 115% of Parameter 7 69% of Parameter 7 84% of Rated Drive Output Current Overload Protection 0 Hz 0 15 Hz 50 Hz 60 Hz Maximum Frequency Parameter 6 = 3 Overload Protection Settings Parameter 07 -- Overload Current Units = Amps Range = 000.1/500.0 Factory Setting = None Parameters 6 and 7 will work in conjunction if Parameter 7 matches the rated amps located on the motor nameplate, and Parameter 6 is set to 1, 2 or 3. When Parameter 6 is set to 0, the setting of Parameter 7 will have no effect on drive operation. The overload current value for Parameter 7 may be set in 0.1A increments. 5-13 Chapter 5 Operation and Programming Local/Remote Control Enable Important: If the Remote Operator Station option is installed, Parameter 8 must be set to 1 or 3 to allow remote control. Parameter 08 -- Local/Remote Control Units = Code Range = 0/1/2/3 Factory Setting = 0 This parameter enables or disables the drive start, jog, and forward/reverse functions as follows. The stop button on the Local Control and Programming Panel will always be functional, but may generate an OP error for certain settings detailed below. If installed at the Control and Signal Wiring Terminal Block, auxiliary input switches S1, S2 and/or S3 will always function as programmed by Parameters 19 and 20 when a valid start command is present. If set to 0, local control has been selected. An L will be the left-hand letter shown in the Mode Display. A maintained start command or jumper is not required at terminals 7 and 8 of the Control and Signal Wiring Terminal Block. • Both directional start pushbuttons on the Local Control and Programming Panel will be functional. • Local jog can be selected by pressing the Shift button. • If Parameter 10 Reverse Lockout is on, only one directional start pushbutton will be available for jogging or running the drive. • The local stop button will stop the drive as programmed by Parameters 11-14. • An auxiliary interlock signal will stop the drive and display either AU or AS as programmed by Parameter 21. If set to 1, external 2-wire control has been selected. An E will be the left-hand letter shown in the Mode Display. • Drive start, jog and forward/reverse is controlled externally through the Control and Signal Wiring Terminal block. Neither directional start pushbutton on the Local Control and Programming Panel will be functional. • An external jog signal will jog the drive and display EJ. Local jog cannot be selected. • If Parameter 10 Reverse Lockout is on, only one direction is available for jogging or running the drive. • The local stop button will allow the drive to coast-to-stop and display OP. 5-14 Chapter 5 Operation and Programming • An auxiliary interlock signal will stop the drive and display either AU or AS as programmed by Parameter 21. If set to 2, local control has been selected, but a maintained stop command or jumper must also be present at terminals 8 and 9 of the Control and Signal Wiring Terminal Block. If not present, all of the following commands will generate an OP error. An L will be the left-hand letter shown in the Mode Display. • Both directional start pushbuttons on the Local Control and Programming Panel will be functional. • Local jog can be selected by pressing the Shift button. • If Parameter 10 Reverse Lockout is on, only one directional start pushbutton will be available for jogging or running the drive. • The local stop button will stop the drive as programmed by Parameters 11-14. • An auxiliary interlock signal will stop the drive and display either AU or AS as programmed by Parameter 21. • An external stop signal at terminals 8 and 9 of the Control and Signal Wiring Terminal Block will allow the drive to coast-to-stop but display an OP error. If set to 3, external 3-wire control has been selected. An E will be the left-hand letter shown in the Mode Display. • Drive start, jog and forward/reverse is controlled externally through the Control and Signal Wiring Terminal block. Neither directional start pushbutton on the Local Control and Programming Panel will be functional and local jog cannot be selected. • An external jog signal will jog the drive and display EJ. Local jog cannot be selected. • If Parameter 10 Reverse Lockout is on, only one direction is available for jogging or running the drive. • The local stop button will allow the drive to coast-to-stop and display OP. • An auxiliary interlock signal will stop the drive and display either AU or AS as programmed by Parameter 21. 5-15 Chapter 5 Operation and Programming Local/Remote Speed Enable Important: If the Remote Operator Station option is installed, Parameter 9 must be set to a value other than 0 to allow remote control. If the BCD Interface option is installed, Parameter 9 must be set to 2 to allow BCD control. Parameter 09 -- Local/Remote Frequency Units = Code Range = 0/1/2/3 Factory Setting =0 Important: If installed at the Control and Signal Wiring Terminal Block, auxiliary input switches S1, S2 and/or S3 will always function as programmed by Parameters 19 and 20 to control drive speed when a valid start command is present. If set to 0, local control has been selected. An L will be the right-hand letter shown in the Mode Display. • Both the increment and decrement pushbuttons on the Local Control and Programming Panel will set drive speed. The select and enter pushbuttons are used to enter the drive set speed. If set to 1, 2 or 3, external control has been selected. An E will be the right-hand letter shown in the Mode Display. If an external speed pot is connected, all other drive speed signals (except from auxiliary switches S1, S2 and/or S3) will be ignored. Both the increment and decrement pushbuttons on the Local Control and Programming Panel will be disabled. The select and enter pushbuttons cannot be used to enter the set drive speed. • If set to 1, drive speed is controlled externally through the Control and Signal Wiring Terminal Block. A 0-5V DC signal connected to the Control and Signal Wiring Terminal Block will control drive speed unless an external speed pot is connected. • If set to 2, drive speed is controlled externally through the Control and Signal Wiring Terminal Block. A 0-10V DC signal connected to the Control and Signal Wiring Terminal Block will control drive speed unless an external speed pot is connected. • If set to 3, drive speed is controlled externally through the Control and Signal Wiring Terminal Block. A 4-20 mA DC signal connected to the Control and Signal Wiring Terminal Block will control drive speed unless an external speed pot is connected. 5-16 Chapter 5 Operation and Programming Reverse Enable Parameter 10 -- Reverse Lockout Units = Off/On Range = 0/1 Factory Setting =0 This parameter enables or disables both local and remote drive direction control. If set to 0, both local and remote direction control is enabled and motor rotation can be selected in either direction. If set to 1, both local and remote direction control is locked out and motor rotation in only one direction can be selected. 5-17 Chapter 5 Operation and Programming Stop Settings Important: If the drive’s internal DC brake is enabled and/or if the Heavy Duty Dynamic Brake option is installed, Parameter 11 must be set to 0. Parameter 11 -- Stop Select Units = Code Range = 0/1 Factory Setting =0 This parameter allows the motor to either ramp-to-stop or coast-to-stop when a stop signal is received either from the Local Control and Programming Panel, or from terminals 8 and 9 at the Control and Signal Wiring Terminal Block. If set to 0, a stop command will ramp the drive to a stop before shutting off output frequency. The ramp followed is set by Parameter 2, Decel Time 1, unless DC braking is used (Parameters 13-15). Important: If ramp-to-stop is selected, refer to Parameter 18 if the drive will be subjected to an overhauling load. If Parameter 18 Decel Frequency Hold is set to 1 (On), an overhauling load may cause the decel ramp to hold at one frequency for an extended period, causing ramp-to-stop commands to appear to be non-functional. If set to 1, a stop command will shut off drive output frequency to the motor and the motor will coast to a stop. ATTENTION: The user has the ultimate responsibility to determine which stopping mode is best suited to the application ! and which stopping mode will meet applicable standards for operator safety on a particular application 5-18 Ramp-to-Stop Chapter 5 Operation and Programming DC Brake Settings Parameters 12, 13 and 14 sets the DC braking action that will occur when the drive is ramped-to-stop or programmed to change direction while the drive is operating for both local and remote control. If DC braking is to be used, Parameter 11 must be set to 0, ramp-to-stop. Parameter 14 Parameter 12 Parameter 13 DC Break Drive Stopped DC Brake Settings Parameter 12 -- DC Hold Frequency Units = Hertz Range = 00.50/60.00 Factory Setting = 00.50 Parameter 12 sets the braking frequency of the internal DC brake in .01 Hz increments. Parameter 13 -- DC Hold Time Units = Seconds Range = 000/10.0 Factory Setting = 000 Parameter 13 will set the braking time of the internal DC brake when used in conjunction with parameters 12 and 14. Parameter 13 will set the hold-at-zero time for changes in direction or stop commands when Parameter 14 is set to 0 (disabled). Parameter 13 may be programmed in 0.1 second increments. Parameter 14 -- DC Hold Volts Units = Code Range = 0/10 Factory Setting =0 If set to 0, the DC brake function will be disabled and Parameters 12 and 14 will have no effect on drive operation. If set to a value of 1-10, the DC brake function will be enabled. Parameters 12 and 13 along with Parameter 14 will then set the DC brake function. The value of Parameter 14 determines the level or strength of the braking that occurs, with 1 being the lowest, 10 the highest. 5-19 Chapter 5 Operation and Programming Max Speed Settings Important: The maximum allowable drive output frequency will be determined by the lowest programmed value of any of the following parameters: • Parameter 3 Frequency Range • Parameter 15 Maximum Frequency • Parameter 51 Upper Frequency Clamp • Parameter 53 Bias Frequency –– If Parameter 53 is Higher Than Parameter 54 • Parameter 54 Gain Frequency –– If Parameter 54 is Higher Than Parameter 53 100% of Output Voltage 0% 0% 100% of Output Frequency Parameter 15 = Parameter 16 100% of Output Voltage 0% 0% Parameter 16 100% of Output Frequency Parameter 15 Max Speed Settings 5-20 Acceleration Acceleration Chapter 5 Operation and Programming Parameter 15 -- Maximum Frequency Units = Hertz Range = 50.00/400.0 Factory Setting = 60.00 If Parameter 3 is set to 50 or 60, the drive will use the lower of the values set by Parameters 3 and 51 as the maximum drive output frequency. Parameter 15 will have no effect on drive operation. If Parameter 3 is set to FF, the drive will use the lower of the values set by Parameters 15 and 51 as the maximum drive output frequency. From 50.00-100.0 Hz, this parameter sets the value of Maximum Frequency in .01 Hz increments. From 100.0-400.0 Hz, this parameter sets the value of Maximum Frequency in 0.1 Hz increments. Parameter 16 -- Base Frequency Units = Hertz Range = 50.00/250.0 Factory Setting = 60.00 The value set by Parameter 16 Base Frequency will be the point where maximum output voltage is applied to the motor when Parameter 3 is set to FF. If Parameter 3 is set to either 50 or 60 Hz, that will be the base frequency that the drive uses. From 50.00-100.0 Hz, this parameter sets the value of Base Frequency in .01 Hz increments. From 100.0-250.0 Hz, this parameter sets the value of Base Frequency in 0.1 Hz increments. 5-21 Deceleration Chapter 5 Operation and Programming Accel and Decel Hold Enable Important: If the Heavy Duty Dynamic Brake option is installed, decel frequency hold must be disabled by setting Parameter 18 to 0. Command Frequency ˚¸ ˚¸ ˚¸ Initial Frequency Parameter 17 = 1 Time 0 ˚ Drive output current = 140% of rated output current. ¸ Drive output current below 140% of rated output current. Initial Frequency ˚¸ ˚¸ ˚¸ Command Frequency Parameter 18 = 1 Time 0 ˚ Drive bus voltage = bus overvoltage trip. ¸ Drive bus voltage below bus overvoltage trip. Accel and Decel Hold Enable 5-22 Acceleration Chapter 5 Operation and Programming Parameter 17 -- Accel Frequency Hold Units = Off/On Range = 0/1 Factory Setting =1 To help avoid drive nuisance trips, this parameter enables or disables drive acceleration during high current conditions. When set to 0, accel stall protection is off. During drive acceleration, should drive output current rise above 140% of rated drive output current, the drive will trip. When set to 1, accel stall protection is on. During acceleration, the drive will hold the accel ramp for 60 seconds should drive output current rise above 140% of rated drive output current. If output current does not fall below 140% after 60 seconds, the drive will trip. Parameter 18 -- Decel Frequency Hold Units = Off/On Range = 0/1 Factory Setting =1 To help avoid drive nuisance trips, this parameter enables or disables drive deceleration during overvoltage conditions. When set to 0, decel stall protection is off. During drive deceleration, should drive bus voltage rise above the Over Voltage values listed below, the drive will trip. Drive Input Voltage Decel Stall Over Voltage Trip 200/208/230V AC 380V DC 430V DC 380/415/460V AC 760V DC 820V DC When set to 1, decel stall protection is on. During deceleration, the drive will hold the decel ramp at one frequency until bus voltage drops below the Decel Stall values listed above. Important: If Parameter 18 Decel Frequency Hold is set to 1 (On), an overhauling load may cause the decel ramp to hold at one frequency for an extended period. This may cause ramp-to-stop commands to appear to be non-functional. 5-23 Chapter 5 Operation and Programming Preset Frequency and Parameter 19 -- Frequency Select Aux Accel/Decel Enable Units = Code Range = 0/1/2 Factory Setting =0 This parameter enables or disables the selection of preset drive frequencies, auxiliary drive preset accel and decel times, or both. To allow drive preset frequencies and/or aux accel and decel times to be selected, external switches must be connected to the Control and Signal Wiring Terminal Block as detailed in Chapter 4. Preset frequencies are set by Parameters 29-35. Auxiliary accel and decel times are set by Parameters 36-41. External switches connected to the Control and Signal Wiring Terminal Block are enabled or disabled as explained below and in the Preset Frequency and Aux Accel/Decel Enable Tables on pages 5-20 –– 5-22. 1. Switch SW2 on the Control Board is factory set to 4SP. When set to 4SP, two external switches may be connected to the drive. In addition to the standard accel and decel rates set by Parameters 1 and 2, switches S1 and S2 may then be used to select three additional accel rates, three additional decel rates, and four preset speeds, as programmed by Parameters 29-31 and 36-41. 2. When switch SW2 on the Control Board is set to 8SP, a total of three external switches may be connected to the drive. In addition to the standard accel and decel rates set by Parameters 1 and 2, switches S1, S2 and S3 may then be used to select three additional accel rates, three additional decel rates, and seven preset speeds, as programmed by Parameters 20 and 29-41. Parameter 19 settings. When set to 0, only the preset frequency function is enabled. External switches connected to the Control and Signal Wiring Terminal Block can only be used to select preset frequencies. When set to 1, only the auxiliary accel and decel function is enabled. External switches connected to the Control and Signal Wiring Terminal Block can only be used to select auxiliary accel and decel times. When set to 2, both the preset frequency function and the auxiliary accel and decel function is enabled. External switches connected to the Control and Signal Wiring Terminal Block can be used to select both preset frequencies and auxiliary accel and decel times. 5-24 Chapter 5 Operation and Programming Parameter 20 -- TB15 Preset/Reset Units = Code Range = 0/1 Factory Setting =0 This parameter selects the control function of switch S3 when three external switches are connected to the Control and Signal Wiring Terminal Block. Parameter 20 settings. When set to 0, external switches S1, S2 and S3 connected to the Control and Signal Wiring Terminal Block can be used to select Preset Frequencies 2-8 and Accel/Decel Times 2-4. When set to 1, external switches S1 and S2 connected to the Control and Signal Wiring Terminal Block can be used to select Preset Frequencies 2-4 and Accel/Decel Times 2-4. If a third switch is installed, switch S3 is used to remotely reset the drive should a drive fault occur. As shown in Figure 4-5 in Chapter 4 –– If Parameter 19 = 0 When and and Control Board External External Switch SW2 Switch S1 Switch S2 is Set to is Set to is Set to The Parameters Selected are 4SP OFF OFF None 4SP ON OFF Preset Frequency 2 4SP OFF ON Preset Frequency 3 4SP ON ON Preset Frequency 4 If Parameter 19 = 1 When and and Control Board External External Switch SW2 Switch S1 Switch S2 is Set to is Set to is Set to The Parameters Selected are 4SP OFF OFF None 4SP ON OFF Accel Time 2 + Decel Time 2 4SP OFF ON Accel Time 3 + Decel Time 3 4SP ON ON Accel Time 4 + Decel Time 4 If Parameter 19 = 2 When and and Control Board External External Switch SW2 Switch S1 Switch S2 is Set to is Set to is Set to The Parameters Selected are 4SP OFF OFF None 4SP ON OFF Preset Frequency 2 + Accel Time 2 + Decel Time 2 4SP OFF ON Preset Frequency 3 + Accel Time 3 + Decel Time 3 4SP ON ON Preset Frequency 4 + Accel Time 4 + Decel Time 4 5-25 Chapter 5 Operation and Programming As shown in Figure 4-5 in Chapter 4 –– If Parameter 19 = 0 and Parameter 20 = 0 When and and and Control Board External External External Switch SW2 Switch S1 Switch S2 Switch S3 is Set to is Set to is Set to is Set to The Parameters Selected are 8SP OFF OFF OFF None 8SP ON OFF OFF Preset Frequency 2 8SP OFF ON OFF Preset Frequency 3 8SP ON ON OFF Preset Frequency 4 8SP OFF OFF ON Preset Frequency 5 8SP ON OFF ON Preset Frequency 6 8SP OFF ON ON Preset Frequency 7 8SP ON ON ON Preset Frequency 8 If Parameter 19 = 1 and Parameter 20 = 0 When and and and Control Board External External External Switch SW2 Switch S1 Switch S2 Switch S3 is Set to is Set to is Set to is Set to The Parameters Selected are 8SP OFF OFF OFF None 8SP ON OFF OFF Accel Time 2 + Decel Time 2 8SP OFF ON OFF Accel Time 3 + Decel Time 3 8SP ON ON OFF Accel Time 4 + Decel Time 4 8SP OFF OFF ON Accel Time 1 + Decel Time 1 8SP ON OFF ON Accel Time 1 + Decel Time 1 8SP OFF ON ON Accel Time 1 + Decel Time 1 8SP ON ON ON Accel Time 1 + Decel Time 1 If Parameter 19 = 2 and Parameter 20 = 0 When and and and Control Board External External External Switch SW2 Switch S1 Switch S2 Switch S3 is Set to is Set to is Set to is Set to The Parameters Selected are 8SP OFF OFF OFF None 8SP ON OFF OFF Preset Frequency 2 + Accel Time 2 + Decel Time 2 8SP OFF ON OFF Preset Frequency 3 + Accel Time 3 + Decel Time 3 8SP ON ON OFF Preset Frequency 4 + Accel Time 4 + Decel Time 4 8SP OFF OFF ON Preset Frequency 5 + Accel Time 1 + Decel Time 1 8SP ON OFF ON Preset Frequency 6 + Accel Time 1 + Decel Time 1 8SP OFF ON ON Preset Frequency 7 + Accel Time 1 + Decel Time 1 8SP ON ON ON Preset Frequency 8 + Accel Time 1 + Decel Time 1 5-26 Chapter 5 Operation and Programming As shown in Figure 4-5 in Chapter 4 –– If Parameter 19 = 0 and Parameter 20 = 1 When and and and Control Board External External External Switch SW2 Switch S1 Switch S2 Switch S3 is Set to is Set to is Set to is Set to The Parameters Selected are 8SP OFF OFF OFF None 8SP ON OFF OFF Preset Frequency 2 8SP OFF ON OFF Preset Frequency 3 8SP ON ON OFF Preset Frequency 4 8SP OFF OFF ON Remote Fault Reset 8SP ON OFF ON Preset Frequency 2 + Remote Fault Reset 8SP OFF ON ON Preset Frequency 3 + Remote Fault Reset 8SP ON ON ON Preset Frequency 4 + Remote Fault Reset If Parameter 19 = 1 and Parameter 20 = 1 When and and and Control Board External External External Switch SW2 Switch S1 Switch S2 Switch S3 is Set to is Set to is Set to is Set to The Parameters Selected are 8SP OFF OFF OFF None 8SP ON OFF OFF Accel Time 2 + Decel Time 2 8SP OFF ON OFF Accel Time 3 + Decel Time 3 8SP ON ON OFF Accel Time 4 + Decel Time 4 8SP OFF OFF ON Remote Fault Reset 8SP ON OFF ON Accel Time 2 + Decel Time 2 + Remote Fault Reset 8SP OFF ON ON Accel Time 3 + Decel Time 3 + Remote Fault Reset 8SP ON ON ON Accel Time 4 + Decel Time 4 + Remote Fault Reset If Parameter 19 = 2 and Parameter 20 = 1 When and and and Control Board External External External Switch SW2 Switch S1 Switch S2 Switch S3 is Set to is Set to is Set to is Set to The Parameters Selected are 8SP OFF OFF OFF None 8SP ON OFF OFF Preset Frequency 2 + Accel Time 2 + Decel Time 2 8SP OFF ON OFF Preset Frequency 3 + Accel Time 3 + Decel Time 3 8SP ON ON OFF Preset Frequency 4 + Accel Time 4 + Decel Time 4 8SP OFF OFF ON Remote Fault Reset 8SP ON OFF ON Preset Frequency 2 + Accel Time 2 + Decel Time 2 + Remote Fault Reset 8SP OFF ON ON Preset Frequency 3 + Accel Time 3 + Decel Time 3 + Remote Fault Reset 8SP ON ON ON Preset Frequency 4 + Accel Time 4 + Decel Time 4 + Remote Fault Reset 5-27 Chapter 5 Operation and Programming Aux Interlock Enable Parameter 21 -- Auxiliary Interlock Units = Code Range = 0/1 Factory Setting =0 To enable drive operation, terminal 16 and logic common at the Control and Signal Wiring Terminal Block must be jumpered. This parameter sets the function of terminal 16 and logic common when a normally closed auxiliary interlock is installed in its place. If set to 0, when the auxiliary contact opens: • The drive will coast-to-stop, display fault AU, and store the fault in Fault Buffer Parameters 59-62. • Fault Contact CR3 on the Control Board will change state to provide a fault signal at terminals 22-24 at the Control and Signal Wiring Terminal Block. If set to 1, when the auxiliary contact opens: • The drive will coast-to-stop and display AS. Since AS is not a fault, it will not be stored in Fault Buffer Parameters 59-62. • Since AS is not a fault, Fault Contact CR3 on the Control Board will not change state to provide a fault signal at terminals 22-24. 5-28 Chapter 5 Operation and Programming Drive Supplied Contact Settings Parameter 22 -- CR1 Select Units = Code Range = 1/2/3 Factory Setting =1 This parameter sets the function of drive supplied contact CR1. CR1 is a normally open contact located at terminals 19 and 20 on the Control and Signal Wiring Terminal Block. If set to 1, the N.O contact will close when the drive is within ± 2 Hz of the run or jog set speed. If set to 2, the N.O contact will close when the drive is at 140% of rated drive output current or 125% of the current set in Parameter 7. If set to 3, the N.O contact will close when the run or jog output frequency is greater than the CR1 Frequency set by Parameter 24. Parameter 23 -- CR2 Select Units = Code Range = 0/1/2/3 Factory Setting =0 This parameter sets the function of drive supplied contact CR2. CR2 is a normally open contact located at terminals 20 and 21 on the Control and Signal Wiring Terminal Block. If set to 0, the N.O contact will close when the drive receives a run or jog start signal. If set to 1, the N.O contact will close when the drive is within ± 2 Hz of run or jog set speed. If set to 2, the N.O contact will close when the drive is at 140% of rated drive output current or 125% of the current set in Parameter 7. If set to 3, the N.O contact will close when the run or jog output frequency is greater than the CR2 Frequency set by Parameter 25. 5-29 Chapter 5 Operation and Programming Parameter 24 -- CR1 Frequency Units = Hertz Range = 00.50/400.0 Factory Setting = 00.50 This parameter sets the frequency that will cause drive supplied contact CR1 to close when Parameter 22 is set to 3. From 00.50-100.0 Hz, this parameter sets the value of CR1 Frequency in .01 Hz increments. From 100.0-400.0 Hz, this parameter sets the value of CR1 Frequency in .1 Hz increments. Parameter 25 -- CR2 Frequency Units = Hertz Range = 00.50/400.0 Factory Setting = 00.50 This parameter sets the frequency that will cause drive supplied contact CR2 to close when Parameter 23 is set to 3. From 00.50-100.0 Hz, this parameter sets the value of CR2 Frequency in .01 Hz increments. From 100.0-400.0 Hz, this parameter sets the value of CR2 Frequency in .1 Hz increments. 5-30 Chapter 5 Operation and Programming Jog Settings Parameter 26 -- Jog Frequency Units = Hertz Range = 00.50/20.00 Factory Setting = 10.00 This parameter sets the jog frequency (speed) that the drive will use when it receives either a local or remote jog command. Jog frequency may be set in .01 Hz increments. Whenever the drive receives a jog command, Accel Frequency Hold, Decel Frequency Hold, and Current Limit functions are disabled. Parameter 27 -- Jog Accel Time Units = Seconds Range = 0000/1600 Factory Setting = 00.50 This parameter sets the time it takes the drive to accelerate to the jog frequency set in Parameter 26. If set to 0000, the drive will enter 40 ms but display 0000. From 000.1-1000 seconds, sets the Jog Accel Time in 0.1 second increments. From 1000-1600 seconds, sets the Jog Accel Time in 1 second increments. Parameter 28 -- Jog Decel Time Units = Seconds Range = 0000/1600 Factory Setting = 00.50 This parameter sets the time it takes the drive to decelerate to 0. If set to 0000, the drive will enter 40 ms but display 0000. From 000.1-1000 seconds, sets the Jog Decel Time in 0.1 second increments. From 1000-1600 seconds, sets the Jog Decel Time in 1 second increments. 5-31 Chapter 5 Operation and Programming Preset Frequency Settings Auxiliary Preset Frequencies are enabled or disabled by Parameters 19 and 20. Individual Preset Frequency settings are selected by setting switches S1, S2 and/or S3 as shown in Parameters 19 and 20. Parameter 29 -- Preset Frequency 2 Units = Hertz Range = 00.50/400.0 Factory Setting = 20.00 From 00.50-100.0 Hz, this parameter sets the value of Preset Frequency 2 in .01 Hz increments. From 100.0-400.0 Hz, this parameter sets the value of Preset Frequency 2 in 0.1 Hz increments. Parameter 30 -- Preset Frequency 3 Units = Hertz Range = 00.50/400.0 Factory Setting = 30.00 From 00.50-100.0 Hz, this parameter sets the value of Preset Frequency 3 in .01 Hz increments. From 100.0-400.0 Hz, this parameter sets the value of Preset Frequency 3 in 0.1 Hz increments. Parameter 31 -- Preset Frequency 4 Units = Hertz Range = 00.50/400.0 Factory Setting = 40.00 From 00.50-100.0 Hz, this parameter sets the value of Preset Frequency 4 in .01 Hz increments. From 100.0-400.0 Hz, this parameter sets the value of Preset Frequency 4 in 0.1 Hz increments. 5-32 Chapter 5 Operation and Programming Parameter 32 -- Preset Frequency 5 Units = Hertz Range = 00.50/400.0 Factory Setting = 15.00 From 00.50-100.0 Hz, this parameter sets the value of Preset Frequency 5 in .01 Hz increments. From 100.0-400.0 Hz, this parameter sets the value of Preset Frequency 5 in 0.1 Hz increments. Parameter 33 -- Preset Frequency 6 Units = Hertz Range = 00.50/400.0 Factory Setting = 25.00 From 00.50-100.0 Hz, this parameter sets the value of Preset Frequency 6 in .01 Hz increments. From 100.0-400.0 Hz, this parameter sets the value of Preset Frequency 6 in 0.1 Hz increments. Parameter 34 -- Preset Frequency 7 Units = Hertz Range = 00.50/400.0 Factory Setting = 35.00 From 00.50-100.0 Hz, this parameter sets the value of Preset Frequency 7 in .01 Hz increments. From 100.0-400.0 Hz, this parameter sets the value of Preset Frequency 7 in 0.1 Hz increments. 5-33 Par 2 Decel 1 Par 41 Decel 4 Par 2 Decel 1 Par 2 Decel 1 Chapter 5 Operation and Programming Parameter 35 -- Preset Frequency 8 Units = Hertz Range = 00.50/400.0 Factory Setting = 45.00 From 00.50-100.0 Hz, this parameter sets the value of Preset Frequency 8 in .01 Hz increments. From 100.0-400.0 Hz, this parameter sets the value of Preset Frequency 8 in 0.1 Hz increments. Typical Remote Command Profile Output Frequency Command Par 29 Par 30 Par 31 Par 32 Par 33 Par 34 Par 35 Frequency Preset 2 Preset 3 Preset 4 Preset 5 Preset 6 Preset 7 Preset 8 Switch SW2 Set to 4SP or 8SP Switch SW2 Set to 8SP Preset Frequency Settings Auxiliary Accel and Decel Settings 5-34 Par 38 Accel 3 Par 38 Accel 1 Par 36 Accel 2 Par 1 Accel 1 Chapter 5 Operation and Programming Auxiliary Accel and Decel Settings Auxiliary Accel and Decel Times are enabled or disabled by Parameters 19 and 20. Individual Accel and Decel Parameter settings are selected by setting switches S1, S2 and/or S3 as shown in Parameters 19 and 20 Parameters 36, 38 and 40 -- Accel Times 2, 3 and 4 Units = Seconds Range = 000.1/1600 Factory Setting = 005.0 Each auxiliary accel time determines a time that it will take the drive to accelerate over a 60 Hz frequency change. From 0 to 0.5 Hz, any auxiliary accel rate set is effectively zero. From 0.5 Hz to maximum output frequency, the accel rate set by each auxiliary accel time will remain constant. For each accel time, the total time it will take the drive to accelerate from an initial frequency to a new command frequency is: Total time = (New Command Frequency – Initial Frequency) × (Accel Time) ÷ 60. From 000.1-1000 seconds, these parameters set the values of Accel Time 2, 3 and 4 in 0.1 second increments. From 1000-1600 seconds, these parameters set the value of Accel Time 2, 3 and 4 in 1 second increments. Parameters 37, 39 and 41 -- Decel Times 2, 3 and 4 Units = Seconds Range = 000.1/1600 Factory Setting = 005.0 Each auxiliary decel time determines a time that it will take the drive to decelerate and ramp-to-stop over a 60 Hz change in frequency. From 0.5 to 0 Hz, the accel rate is non-linear and set by either DC injection braking or the DC dynamic brake if it is installed. From maximum output frequency to 0.5 Hz, the accel rate set by Parameter 2 will remain constant. For each decel time, the total time it will take the drive to decelerate from an initial frequency to a new command frequency is: Total time = (New Command Frequency – Initial Frequency) × (Accel Time) ÷ 60. From 000.1-1000 seconds, these parameters set the values of Decel Time 2, 3 and 4 in 0.1 second increments. From 1000-1600 seconds, these parameters set the value of Decel Time 2, 3 and 4 in 1 second increments. 5-35 Deceleration Chapter 5 Operation and Programming Skip Frequency Settings Parameters 42, 43 and 44 -- Skip Frequencies 1, 2 and 3 Units = Hertz Range = 0000/400.0 Factory Setting = 0000 To help avoid undesirable mechanical resonance, Parameters 42-44 prevents the drive from running at one, two or three specific frequencies. Although the drive will use these frequencies when accelerating or decelerating, they cannot be set as ”running” frequencies by any drive parameter. The drive will stay slightly above or slightly below these frequencies if the frequency values are entered. If a Skip Frequency value of 0000 is selected, the skip frequency function of that parameter is disabled. From 00.50-100.0 Hz, Parameters 42-44 sets the Skip Frequencies in .01 Hz increments. From 100.0-400.0 Hz, Parameters 42-44 sets the Skip Frequencies in 0.1 Hz increments. Parameter 45 Parameter 45 Parameter Parameter Parameter Command Parameter Parameter Parameter Frequency 44 42 43 43 42 44 Skip Frequency Settings 5-36 Acceleration Chapter 5 Operation and Programming Parameter 45 -- Skip Frequency Band Units = Code Range = 0/10 Factory Setting =0 Parameter 45 allows each of the individual Skip Frequencies set in Parameters 42-44 to be expanded into three bands of skip frequencies in 2-20 Hz increments. Setting a Skip Frequency Band value of 0 will disable the Skip Frequency Band function, but not individual Skip Frequency values set by Parameters 42-44. Setting a Skip Frequency Band value other than 0 will enable Skip Frequency values and expand their range by 2 Hz. For example, if Parameter 45 is set to 1, a Skip Frequency value set by Parameter 42, 43 or 44 will expand to a band that includes the Skip Frequency value with an additional 1 Hz band on either side. If set to 10, a Skip Frequency value set by Parameter 42, 43 or 44 will expand to a band that includes the Skip Frequency value with an additional 10 Hz band on either side. Important: 1. If the drive is programmed with a Parameter 3 Frequency Range and/or Parameter 15 Maximum Frequency value that falls within a skip frequency bandwidth, the drive will operate only through the non-skip frequencies below Parameters 3 and 15. 2. If the drive is programmed with a Parameter 51Upper Frequency Clamp value that falls within a skip frequency bandwidth, the drive will operate only through the non-skip frequencies below Parameter 51, then jump to the Parameter 51 value at a maximum speed command. 3. If Parameters 3, 15 and 51 are all within the skip frequency bandwidth, the drive will operate only though the non-skip frequencies below the lowest value set by Parameters 3, 15 and 51. 5-37 Chapter 5 Operation and Programming Current Limit Setting Parameter 46 -- Current Limit Units = Seconds Range = 00/1.5 Factory Setting =00 Should drive current rise above 140% of rated drive output current, the drive will attempt to limit current for one minute. Parameter 46 sets the frequency foldback rate used to decrease current in .1 second increments. Frequency foldback allows the drive to ramp output frequency down far enough to temporarily eliminate an overcurrent condition. When Parameter 46 is set to 00, the Current Limit function set by Parameter 46 is disabled and the drive’s overcurrent feature will trip the drive should current rise above 200%. ¸Drive Output Current¸¸ ˚˚˚ˇ Drive Trips at 200% 200% �˝˛ 140% O O O V V V E E E R R R Drive Drive Drive Drive C C C Operating Operating Operating U Operating U U R R R Range Range Range Range R R R E E E N N N T T T 0 Time ˚ % of Drive Overcurrent ¸ Drive Output Frequency Decel Ramp � Parameter 46 = 0.5 Seconds ˝ Parameter 46 = 1.0 Seconds ˛ Parameter 46 = 1.5 Seconds ˇ Parameter 46 = 0.0 Seconds Current Limit Setting 5-38 Chapter 5 Operation and Programming ATTENTION: Auto restart operation may only be used as Auto Restart Settings outlined in NFPA79, Paragraph 6-14 (exceptions 1-3) for ! specialized applications. Equipment damage and/or personal injury may result if the settings of Parameters 47-49 are used in an inappropriate application. Parameter 47 -- Power Loss Restart Units = Code Range = 0/1/2/3 Factory Setting =1 This parameter selects the drive restart action taken if input power is interrupted and restored within 100 ms –– However –– restart settings 1 and 2 in Parameter 48 will override any settings made in Parameter 47. • When set to 0, the drive will restart and ramp to the last selected speed –– but only for 2-wire external control. • When set to 1, Power Loss Restart is disabled for both 2 and 3-wire control schemes. The drive will not restart until the fault is cleared by first issuing a stop command, then a start command. The drive will then restart and ramp to the last selected speed. • 2 defines the drive restart action for 2-wire external control. Once the drive receives a start command, the drive will start and ramp to the last selected speed but only after the initial waiting time set by Parameter 49. Should an LU fault occur or OP message appear, the drive will restart and ramp to the last selected speed after the initial waiting time set by Parameter 49 without reissuing a start command. • 3 defines the drive restart action for both 2 and 3-wire control. Once the drive receives a start command, the drive will start and ramp to the last selected speed but only after the initial waiting time set by Parameter 49. Should an LU fault occur or OP message appear, the drive will not restart until the fault or message has been cleared by first issuing a stop command, then a start command. Once cleared, the drive will start and ramp to the last selected speed after the initial waiting time set by Parameter 49. 5-39 Chapter 5 Operation and Programming Parameter 48 -- RideThru Restart Units = Code Range = 0/1/2 Factory Setting =0 For all control schemes, this parameter selects the drive restart action taken if input power is interrupted and restored within 100 ms. Restart settings 1 and 2 in Parameter 48 will override any settings made in Parameter 47. • When set to 0, if power is removed for 15 ms, Ride-Thru Restart is disabled and the drive will generate an LU fault. The drive will not restart until the fault is cleared by first issuing a drive stop command, then a start command. The drive will then restart and ramp to the last selected speed. • When set to 1, if power is removed for 15 ms, the drive will generate an LU fault. If power is restored within 100 ms (or longer depending on load), the drive will restart from zero speed, then ramp to the last selected speed after the initial waiting time set by Parameter 49. • When set to 2, if power is removed for 15 ms, the drive will generate an LU fault. If power is restored within 100 ms (or longer depending on load), the drive will continue to operate at the selected speed. If longer than 100 ms, the drive will restart only after the initial waiting time set by Parameter 49. Parameter 49 -- Restart Time Select Units = Seconds Range = 000.1/100.0 Factory Setting = 000.1 This parameter sets the time the drive will wait before acting on a restart command after an LU fault has occurred. The value of Parameter 49 is selectable in 0.1 second increments. 5-40 Chapter 5 Operation and Programming Lower and Upper Important: The maximum allowable drive output frequency will be Frequency Clamp Settings determined by the lowest value programmed into the following parameters: • Parameter 3 Frequency Range • Parameter 15 Maximum Frequency • Parameter 51 Upper Frequency Clamp • Parameter 53 Bias Frequency –– If Parameter 53 is Higher Than Parameter 54 • Parameter 54 Gain Frequency –– If Parameter 54 is Higher Than Parameter 53 Parameter 50 -- Lower Frequency Clamp Units = Hertz Range = 00.50/400.0 Factory Setting = 00.50 This parameter sets the minimum frequency or speed that the drive can be set to by any input control signal. From 00.50-100.0 Hz, Parameter 50 sets the Lower Frequency Clamp in .01 Hz increments. From 100.0-400.0 Hz, Parameter 50 sets the Lower Frequency Clamp in 0.1 Hz increments. Important: If an external potentiometer, a 0-5V DC, a 0-10V DC or a 4-20mA frequency reference is required: • For directly proportional applications, enable Parameter 52 and enter a minimum value of 00.50 for Parameter 53 if the Lower Frequency Clamp is to set the minimum frequency. • For inverse follower applications, enable Parameter 52 and enter a minimum value of 00.50 for Parameter 54 if the Lower Frequency Clamp is to set the minimum frequency. 5-41 Deceleration Chapter 5 Operation and Programming ˚ Maximum Output Frequency Parameter 51 Parameter 50 Minimimum Frequency = 0.5 0 0% 100% of Input Frequency Signal ˚ Maximum Output Frequency Parameter 51 Parameter 50 Minimimum Frequency = 0.5 0 0% 100% of Input Frequency Signal ˚ Maximum Output Frequency = 50 Hz if Parameter 3 = 50 60 Hz if Parameter 3 = 60 Parameter 15 if Parameter 3 = FF Lower and Upper Frequency Clamp Settings Parameter 51 -- Upper Frequency Clamp Units = Hertz Range = 00.50/400.0 Factory Setting = 400.0 This parameter sets the highest frequency or speed that the drive can be set to by any input control signal, unless Parameter 15 (Maximum Frequency) or Parameter 3 (Frequency Range) has been set lower. If set to a value higher than Parameter 3 or 15, the value will be entered, but the drive will default to the lowest value set by Parameter 3 or 15 when operating. From 00.50-100.0 Hz, Parameter 51 sets the Upper Frequency Clamp in .01 Hz increments. From 100.0-400.0 Hz, Parameter 51 sets the Upper Frequency Clamp in 0.1 Hz increments. 5-42 Acceleration Chapter 5 Operation and Programming Bias and Gain Settings Important: The maximum allowable drive output frequency will be determined by the lowest programmed value of any of the following parameters: • Parameter 3 Frequency Range • Parameter 15 Maximum Frequency • Parameter 51 Upper Frequency Clamp • Parameter 53 Bias Frequency –– If Parameter 53 is Higher Than Parameter 54 • Parameter 54 Gain Frequency –– If Parameter 54 is Higher Than Parameter 53 Parameter 52 -- Bias and Gain Enable Units = Code Range = 0/1 Factory Setting =0 This parameter enables or disables both the Bias and Gain Frequencies set by Parameters 53 and 54. Bias and Gain Frequencies allows a remote speed signal to be used within a specific minimum and maximum frequency range. The Bias and Gain Frequencies may be used to provide a directly or inversely proportional 0-5V DC, 0-10V DC, 4-20 mA, or external speed pot signal at the Control and Signal Wiring Terminal Block. If set to 0, the bias and gain function is disabled. If set to 1, the bias and gain function is enabled. If the 1333 is to produce 0 output speed at 0 external input signal: • Parameter 9 Local/Remote Frequency must be set to remote. • Parameter 52 Bias and Gain Enabled must be enabled. • Parameter 53 Bias Frequency must be set to the minimum output frequency required. • Parameter 54 Gain Frequency must be set to the maximum output frequency required. If the 1333 is to produce maximum output speed at 0 external input signal: • Parameter 9 Local/Remote Frequency must be set to remote. • Parameter 52 Bias and Gain Enabled must be enabled. • Parameter 53 Bias Frequency must be set to the maximum output frequency required. • Parameter 54 Gain Frequency must be set to the minimum output frequency required. 5-43 Deceleration Chapter 5 Operation and Programming ˚ 100% of Output Frequency Parameter 54 When Bias Frequency is Less Than Gain a Directly Proportional Input Frequency Signal is Produced Bias Frequency Less Than Gain Parameter 53 = 0% 0% 100% of Input Frequency Signal ˚ 100% of Output Frequency Parameter 53 Parameter 54 When Bias Frequency Bias Frequency Greater Than Gain is Greater Than Gain an Inversely Proportional Input Frequency Signal is Produced 0% 0% 100% of Input Frequency Signal ˚ 100% of Output Frequency = 50 Hz if Parameter 3 = 50 60 Hz if Parameter 3 = 60 Paramer 15 if Parameter 3 = FF Bias and Gain Settings Parameter 53 -- Bias Frequency Units = Hertz Range = 00.00/400.0 Factory Setting = 00.00 From 00.50-400.0 Hz, Parameter 53 sets the Bias Frequency in .01 Hz increments. From 100.0-400.0 Hz, Parameter 53 sets the Bias Frequency in 0.1 Hz increments. Parameter 54 -- Gain Frequency Units = Hertz Range = 00.50/400.0 Factory Setting = 60.00 From 00.50-400.0 Hz, Parameter 54 sets the Gain Frequency in .01 Hz increments. From 100.0-400.0 Hz, Parameter 54 sets the Gain Frequency in 0.1 Hz increments. 5-44 Acceleration Chapter 5 Operation and Programming Output Meter Settings Parameter 55 -- Frequency Output (Amps) Units = % of Maximum Output Signal Range = 075/125 Factory Setting = 100 This parameter is used to calibrate an output frequency ammeter while the drive is running. It may be set from 75-125% of the maximum output signal, 1 mA. The 1 mA signal is selected by setting switch SW1 on the Control Board to the 1 mA position. Parameter 56 -- Frequency Output (Volts) Units = % of Maximum Output Signal Range = 075/125 Factory Setting = 100 This parameter is used to calibrate an output frequency voltmeter while the drive is running. It may be set from 75-125% of the maximum output signal, 10V DC. The 10V DC signal is selected by setting switch SW1 on the Control Board to the 10V DC position. Monitoring Mode Settings Parameter 57 -- Monitor Display Select Units = Code Range = 0/1/2 Factory Setting =0 This parameter sets one of three alternate monitoring modes that may be selected while the drive is running. When set to 0, A0 –– monitor equivalent drive output current. When set to 1, A1 –– monitor equivalent motor RPM. When set to 2, A2 –– monitor drive control frequency. Parameter 58 -- Motor Pole Select Units = Code Range = 2/4/6/8/10 Factory Setting =4 To allow motor RPM to be calculated and displayed when monitoring mode A1 is selected, this parameter is used to enter the number of motor poles. 5-45 Chapter 5 Operation and Programming Drive Fault Memory Parameters 59, 60, 61 and 62 -- Fault Buffer 0, 1, 2, and 3 Units = None Range = None Factory Setting = None Parameters 59-62 will store the last (4) faults that the drive has encountered in a cascading mode. • Fault Buffer 0 will store the new fault. • Fault Buffer 1 will store the fault from Fault Buffer 0. • Fault Buffer 2 will store the fault from Fault Buffer 1. • Fault Buffer 3 will store the fault from Fault Buffer 2. 5-46 Chapter 6 Startup The Startup Process The following startup procedure uses the Local Control and Programming Panel to setup the drive. To guard against damage to equipment caused by incorrect or inappropriate parameter settings, steps 1-28 must be followed in order. Step 29 is provided to allow you to incorporate an external 2 or 3-wire control scheme into your application. ATTENTION: Power must be applied to the drive with the cover removed to perform certain startup procedures. Voltages on many ! components are at incoming line potential or bus voltage. To avoid electric shock hazard or damage to equipment, do not touch any drive component other than those specified in the startup procedure. ATTENTION: Become familiar with the equipment and read through the wiring, speed selection and adjustment sections before ! attempting to perform the startup procedures. Adjustments may be required to meet specific load characteristics or operator preference. Exercise extreme care when performing any task on the drive. Failure to do so may result in electric shock or equipment damage. As shown on the next page, a DC bus neon light at the top of the 1333 has been provided to provide visual indication that bus voltage is present. Bus voltage may be verified by using a voltmeter and measuring the voltage between +BUS and –BUS on the Power Terminal Block. Do not attempt to service the drive until 2 minutes after the neon light has extinguished and bus voltage has discharged to zero volts. 6-1 Chapter 6 Startup Important: 1. Power must be applied to the drive when viewing or changing 1333 parameters. Previous programming may effect the drive status when power is applied. 2. Remote circuits may be connected to the Control and Signal Wiring Terminal Block on the Main Control Board. Confirm that all circuits are in a de-energized state before applying power. 3. User supplied voltages may exist at the Control and Signal Wiring Terminal Block even when power is not applied to the drive. 4. If you cannot complete a procedure, immediately refer to Appendix B — Preventive Maintenance and Troubleshooting Common Drive Problems. Do not proceed. Determine the cause of the problem and correct the problem first, then return to the startup procedure. DC Bus Neon Light Drive Control Board Switches SW2 SW1 Control and Signal Wiring Terminal Block Power Terminal Block Auxiliary Interlock Drive Nameplate Drive Cover Thumbscrews Figure 61 -- 3/45HP (.554kW) Drive 6-2 Chapter 6 Startup DC Bus Neon Light Drive Control Board Switches SW2 SW1 Control and Signal Wiring Terminal Block Power Terminal Block Auxiliary Interlock Drive Cover Thumbscrews Drive Nameplate Figure 62 -- 71/220HP (5.515kW) Drive 1333 parts, switches and terminal blocks shown in Figures 6-1, 6-2 and 6-3 are referenced throughout the Initial Operation, Function Checks, Function and Final Settings Sections of this chapter. 6-3 Chapter 6 Startup Initial Operation Step 1 - Motor Disconnected Verify that AC line power at the disconnect device is within the rated value of the drive nameplate data. Drive nameplate and alternate voltage ratings are explained in Chapter 2 — Drive Identification. Step 2 Remove and lock out all incoming power to the drive. Remove the drive U/ V/ W/ cover and disconnect the motor leads from terminals at T1, T2, T3 the Power Terminal Block. Insulate the exposed wires to prevent accidental contact with other drive components. Step 3 If an auxiliary interlock is not installed at the Control and Signal Wiring Terminal Block, verify that the spare jumper provided with the drive is installed between terminals 16 and 17. Step 4 Replace the drive cover and tighten both thumbscrews. Apply power to the drive and verify that no faults are displayed. • Both the main and mode displays should immediately light. • The main display should read 0000. If the main display indicates OU or LU, an incorrect voltage is being applied to the drive. • The mode display should read LL. to allow control of the drive from the Local Control and Programming Panel. If not, refer to Chapter 5 –– Operation and Programming to change Parameters 8 and 9 to local control. Important: Steps 5-15d are Function Checks based on factory parameter settings. The function groups listed, reference the same parameters as grouped in Chapter 5 and Appendix C. If the drive has been previously commissioned, parameter settings may not be compatible with this startup procedure. Drive status and fault conditions will be unpredictable when power is first applied. To obtain the proper results, initially change all parameter values to the factory settings listed on the drive cover label. If it is required to change a parameter, you will be instructed to do so. 6-4 Chapter 6 Startup The Main Display Function Checks - Motor Disconnected Hz LED Alternate LED The Select Pushbutton The Lock Switch The Enter Pushbutton The Stop Pushbutton The Directional Start Pushbutons The Mode Display The Shift Pushbutton The Increment Pushbutton The Decrement Pushbutton Figure 63 -- 3/420HP (.5515kW) Controls Step 5 -- Local/Remote Control Enable Check Max Speed Settings Check Start the drive by pressing either directional start pushbutton. The pushbutton will light. Press and hold the increment pushbutton and watch the display increase. Release thew pushbutton when the display reaches 60.00 Hz or maximum speed. Step 6 -- Monitor Mode Settings Check Press the select pushbutton once. The main display will flash and show the last manual set speed entered. Press the select pushbutton again. A0. will be shown in the mode display, drive output amps in the main display, as set by Parameter 57. Press the select pushbutton again. The mode display will flash and show 0I. to indicate the parameter being viewed, and the main display will show 005.0, the accel time set by Parameter 1. Press the pushbutton again and 60.00Hz will again be displayed. Step 7 -- Reverse Enable Check Accel and Decel Settings Check Press the other directional start pushbutton. The pushbutton will light and the drive display will ramp down to 0.00 Hz within the decel time set by Parameter 2, then immediately ramp up to 60.00 Hz, the maximum speed presently programmed by Parameter 3, within the accel time set by Parameter 1. Reversing is enabled or disabled by Parameter 10. 6-5 Chapter 6 Startup Function Checks Step 8 -- Local/Remote Speed Enable Check - Motor Disconnected Lower and Upper Frequency Clamp Settings Check Press the select pushbutton once. The main display will again flash and show the last manual set speed entered. Using the increment, decrement and shift pushbuttons, any value between 00.50 (the lower frequency clamp set by Parameter 50), and 60.00 Hz can be selected. Select a value and press the enter key. The drive will either accel within the accel time set by Parameter 1, or decel within the decel time set by Parameter 2, to a value within these limits. Had Parameter 51 been set to a value lower than 60.00 Hz, the upper frequency clamp would be the highest frequency the drive could reach. Step 9 -- Stop Setting Check Press the stop pushbutton to stop the drive. The drive display will ramp down to zero within the decel time set by Parameter 2. Had Parameter 11 been set to 1, the drive would have been set to coast-to-stop and Parameter 2 would have no affect on stopping time. Step 10 -- Jog Settings Check Press the shift pushbutton once and LJ. will be shown in the mode display. Press and hold either directional start pushbutton. The pushbutton will light and the drive display will ramp up to I0.00 Hz, or the maximum jog speed set by Parameter 26, within the jog accel time set by Parameter 27. Release the directional start pushbutton and the drive will ramp back down to 0.00 Hz at the jog decel time set by Parameter 28. Once fully stopped, the drive will display 0000. Step 11 -- Auxiliary Interlock Enable Check Drive Fault Memory Check Start the drive. If an external auxiliary interlock has been installed between terminals 16 and 17 at the Control and Signal Wiring Terminal Block, open the interlock. AU will be shown at the main display, indicating an auxiliary interlock fault. • Press the stop pushbutton to clear the fault. • Press the select pushbutton three times to access the parameter display. • Select Parameter 59. Fault Buffer 0 will display AU, the last fault received by the drive. If Parameter 21 had been set to 1, the drive would have displayed AS at the main display, indicating an auxiliary stop. An AS is not a fault, and therefore not stored in memory. 6-6 Chapter 6 Startup Function Checks Step 12 -- Drive Supplied Contact Settings Check - Motor Disconnected Stop the drive. Remove and lock out all incoming power to the drive, then remove the drive cover. Reapply power and start the drive. N.O. contact CR2 (terms. 20 & 21 on the Control and Signal Wiring Terminal Block) will close as presently programmed by Parameter 23. Once the drive is within ± 2 Hz of set speed, N.O. contact CR1 (terminals 19 & 20 on the Control and Signal Wiring Terminal Block) will close since Parameter 24 is presently set to 1. Step 13a -- Auto Restart Settings Check ATTENTION: Auto restart operation may only be used as outlined in NFPA79, Paragraph 6-14 (exceptions 1-3) for ! specialized applications. Equipment damage and/or personal injury may result if the settings of Parameters 47-49 are used in an inappropriate application. To properly program the drive to restart when required demands that Parameters 47-49 be coordinated correctly. When Parameter 48 is set to 1 or 2, it will override any setting made in Parameter 47. Likewise the restart time set in Parameter 49 will affect the restart actions taken by both Parameters 47 and 48. Step 13b -- Auto Restart Settings Check If Power Loss Restart is required, set Parameters 1 and 3. Stop the drive. • Change Parameter 47 from 1 to 3. • Change Parameter 49 from 000.1 seconds to 10.00 seconds. Press the start pushbutton. The directional start pushbutton LED will immediately light. After 10 seconds the drive will ramp up to 60 Hz and the main display will show 60.00. Remove then reapply incoming power to the drive at the disconnect device within 100 ms. LU will be shown at the main display indicating a power fault. Press the stop pushbutton to clear the fault, then the start pusbutton to start the drive. Since Parameter 49 has been changed, the drive will not restart for 10 seconds. • Had the drive been configured for 2-wire control and Parameter 47 set to 0, without clearing the fault, the drive would have automatically restarted and ramped up to 60 Hz without a waiting time. • Had the drive been configured for 2-wire control and Parameter 47 set to 3, without clearing the fault, the drive would have automatically restarted and ramped up to 60 Hz after 10 seconds. 6-7 Chapter 6 Startup Function Checks Step 13c -- Auto Restart Settings Check - Motor Disconnected If Ride-Thru Restart is required, set Parameters 1 and 3. Stop the drive. • Change Parameter 48 from 0 to 1. Remove then reapply incoming power to the drive at the disconnect device within 100 ms. LU will be shown at the main display indicating a power fault. The directional start pushbutton LED will immediately light. After 10 seconds, the drive will ramp up to 60 Hz and the main display will show 60.00. Stop the drive. • Change Parameter 48 from 1 to 2. Remove then reapply incoming power to the drive at the disconnect device within 100 ms. LU will be shown at the main display indicating a power fault. The directional start pushbutton LED will immediately light. After 10 seconds, the main display will immediately show 60.00. The drive accel ramp has been eliminated and the drive will restart at the last commanded speed, 60 Hz. Stop the drive and return Parameters 47-49 to their factory settings. Step 14 -- Bias and Gain Settings Check If an external 10kΩ, 2W potentiometer, 0-5V DC, 0-10V DC or 4-20 mA signal is connected to the drive, the bias and gain settings should be verified. • Change Parameter 52 from 0 to 1 to enable the bias and gain function. • Change Parameter 53 from 00.50 to 60.00. • Change Parameter 54 from 60.00 to 00.50. With zero speed signal applied to the drive, start the drive. Apply the smallest speed signal possible. The drive display will immediately ramp up to 60.00 Hz. Apply maximum signal to the drive. The drive display will ramp down to 0.50 Hz. This is because an inversely proportional signal has been sent to the drive. Stop the drive and return Parameters 52-54 to their factory settings. 6-8 Chapter 6 Startup Step 15a -- Preset Frequency and Aux Accel/Decel Enable Check If external switches have been connected to the Control and Signal Wiring Terminal Block as detailed in Chapter 5, preset frequencies as well as auxiliary accel and decel times can be checked. Step 15b -- Preset Frequency and Aux Accel/Decel Enable Check Enable Auxiliary Accel/Decel Settings Stop the drive and depress the lock button to allow programming. Set Parameter 19 to 2. By setting Parameter 19 to 2, auxiliary accel/decel times will be enabled and can be checked simultaneously with preset speeds. Step 15c -- Preset Frequency and Aux Accel/Decel Enable Check If two preset speed switches have been installed, verify that switch SW2 is set to 4SP. • Closing switch S1 and opening switch S2 will force the drive to 20.00 Hz, the Preset Frequency 2 value set by Parameter 29, within the 2nd auxiliary accel time set by Parameter 36, or the 2nd auxiliary decel time set by Parameter 37. • Opening switch S1 and closing switch S2 will force the drive to 30.00 Hz, the Preset Frequency 3 value set by Parameter 30, within the 3rd auxiliary accel time set by Parameter 38, or the 3rd auxiliary decel time set by Parameter 39. • Closing switches S1 and S2 will force the drive to 40.00 Hz, the Preset Frequency 4 value set by Parameter 31, within the 4th auxiliary accel time set by Parameter 40, or the 4th auxiliary decel time set by Parameter 41. 6-9 Chapter 6 Startup Function Checks Step 15d -- Preset Frequency and Aux Accel/Decel Enable Check - Motor Disconnected If three preset speed switches have been installed, verify that switch SW2 is set to 8SP. • Closing switch S1 and opening switches S2 and S3 will force the drive to 20.00 Hz, the Preset Frequency 2 value set by Parameter 29, within the 2nd auxiliary accel time set by Parameter 36, or the 2nd auxiliary decel time set by Parameter 37. • Opening switches S1 and S3 and closing switch S2 will force the drive to 30.00 Hz, the Preset Frequency 3 value set by Parameter 30, within the 3rd auxiliary accel time set by Parameter 38, or the 3rd auxiliary decel time set by Parameter 39. • Closing switches S1 and S2 and opening switch S3 will force the drive to 40.00 Hz, the Preset Frequency 4 value set by Parameter 31, within the 4th auxiliary accel time set by Parameter 40, or the 4th auxiliary decel time set by Parameter 41. • Opening switches S1 and S2 and closing switch S3 will force the drive to 15.00 Hz, the Preset Frequency 5 value set by Parameter 32, within the 4th auxiliary accel time set by Parameter 40, or the 4th auxiliary decel time set by Parameter 41. • Opening switch S2 and closing switches S1 and S3 will force the drive to 25.00 Hz, the Preset Frequency 6 value set by Parameter 33, within the 4th auxiliary accel time set by Parameter 40, or the 4th auxiliary decel time set by Parameter 41. • Opening switch S2 and closing switches S1 and S3 will force the drive to 35.00 Hz, the Preset Frequency 7 value set by Parameter 34, within the 4th auxiliary accel time set by Parameter 40, or the 4th auxiliary decel time set by Parameter 41. • Closing switches S1, S2 and S3 will force the drive to 45.00 Hz, the Preset Frequency 8 value set by Parameter 35, within the 4th auxiliary accel time set by Parameter 40, or the 4th auxiliary decel time set by Parameter 41. 6-10 Chapter 6 Startup ATTENTION: The following steps may cause motor rotation in Function Settings an unknown direction. To guard against equipment damage, always ! - Motor Connected disconnect the motor from the load before proceeding. - NoLoad Condition Important: The remaining steps are Function Settings that reference the same parameters as grouped in Chapter 5 –– Operation and Programming. Step 16 Stop the drive and remove and lock out all incoming power to the drive. U Remove the drive cover and reconnect the motor leads at terminals / T1, V W / / at the Power Terminal Block. T2, T3 Step 17 Replace the drive cover and tighten both thumbscrews. Apply power to the drive and verify that no faults are displayed. • Both the main and mode displays should immediately light. • The main display should read 0000. If the main display indicates OU or LU, an incorrect voltage is being applied to the drive. • The mode display should read LL. to allow control of the drive from the Local Control and Programming Panel. If not, refer to Chapter 5 to change Parameters 8 and 9 to local control. Step 18 -- VoltsperHertz Curve Settings Overload Protection Settings Set Parameters 3 and 4 to match your volts-per-Hertz curve and drive frequency range requirements as detailed in Chapter 5. If overload protection is not required, leave Parameter 6 set to 0. If overload protection is required: • Set Parameter 6 to correspond to the motor duty as outlined in Chapter 5. • Set Parameter 7 to correspond to the rated amps on your motor nameplate. 6-11 Chapter 6 Startup Function Settings Step 19 - Motor Connected Press the shift pushbutton once and LJ. will be shown in the mode display. - NoLoad Condition Press and release the directional start pushbutton that will be your forward motor direction. If the direction of motor rotation is incorrect: • Remove input power, wait until the displays are no longer lit, then remove the drive cover. • Verify that the DC bus neon light is no longer lit and that bus voltage at the +Bus and –Bus terminals of the power terminal block is zero. U V • Interchange any two of the three motor leads at terminals / / T1, T2, W / at the Power Terminal Block. T3 • Replace the drive cover and tighten both thumbscrews. Apply power to the drive and verify that no faults are displayed. Step 20 -- Output Meter Settings If an external output ammeter or voltmeter is connected to the Control and Signal Wiring terminal block, the meter should be calibrated and switch SW1 should be set as detailed by Parameters 55 or 56 in Chapter 5. 6-12 Chapter 6 Startup ATTENTION: To avoid hazards of electrical shock or injury Final Settings from moving equipment, product, or process ingredients: ! - Motor Connected • Alert all personnel. - Load Connected • Install all guards. • Check operation of all safety devices. • Be prepared to stop the motor immediately. Step 21 Disconnect and lock-out all power. Connect the motor to the load. Before applying power, review the parameter descriptions in Chapter 5. Each parameter may have a significant effect on fundamental drive and motor operation regardless of the control method used. Apply power. Prepare to operate the drive and motor under actual control and load conditions. It is recommended to begin at low torque and speed. Start the motor and run the machine or process to determine if parameter settings are acceptable for the application. If not, stop the drive and reset parameters. Refer to Chapter 5 to make parameter changes and record the changes in Appendix C. Step 22 If Increased Motor Torque is Required at Startup Increase the value of Parameter 5 in small increments. Parameter 5 adds from 0 to 40% of the drive output voltage to the motor at low drive frequencies, boosting motor torque at startup. DC boost can be added to any volts-per-Hertz curve. The optimum DC boost setting is the lowest level that will permit satisfactory starting torque for the motor and drive. Higher than optimum boost may produce unnecessary motor current at low frequencies and contribute to motor overheating. Excessive boost may even force the drive into an overcurrent condition. Step 23 If DC Braking is Required for Speed Changes, Reversing or to Stop the Motor Set Parameter 14 to 1 first. When Parameter 14 is set to a value of 1-10, the drive’s DC brake function will be enabled. Parameters 12 and 13 along with Parameter 14 will then set the DC brake function. The value of Parameter 14 determines the level or strength of the braking that occurs, with 1 being the lowest, 10 the highest. 6-13 Chapter 6 Startup Final Settings Step 24 - Motor Connected If Heavy Duty Dynamic Braking is to be Installed - Load Connected If Heavy Duty Dynamic braking is required, set Parameters 11 and 14 to 0. Step 25 If Machine Resonance is Encountered Set Parameters 42-45 to skip those frequencies which cause the machine to resonate. Step 26 If Nuisance Tripping is Encountered Enable Parameters 17 and/or 18 to disable drive acceleration or deceleration during high Bus current or voltage conditions. Step 27 If the Connected Load is an Overhauling Load Set Parameter 18 to 0 to disable Decel Frequency Hold. Step 28 If a Different Running Monitor Mode is Required Change Parameter 57 to: • 0 to monitor drive output current. • 1 to monitor equivalent motor RPM. • 2 to monitor drive control frequency. Step 29 If an External 2 or 3-Wire Control Scheme is to be Used • Connect the 2 or 3-wire controls as shown in Figure 4-3 and described in Chapter 4. • Set Parameter 8 to 1 for 2-wire control, 3 for 3-wire control. • Repeat the startup procedure starting from step 1. 6-14 Appendix A Bulletin 1333 Options Using Bulletin 1332 and Bulletin 1332 and 1333 Options can be used with Series D drives. 1333 Options with Point-to-point interconnections and the required Series D parameter Bulletin 1333 Series D Drives settings are detailed below and on the following pages. Refer to the individual option kit instructions for installation procedures and the additional information required to setup each option. Bulletin 1333 Series D 1332MODF 1332MODF Control and Signal Wiring Terminal Block Remote Operator Station Remote Operator Station Term 1 Term 2 Term 3 Term 3 Term 4 Term 5 Term 6 Term 7 Term 7 Term 8 Term 8 Term 3 Term 9 Term 10 Term 11 Term 11 Term 12 Term 13 Start/Stop and Forward/Reverse Control To allow the 1333 Series D to accept 1332-MOD-F start/stop and forward/reverse commands, Parameter 8 Local/Remote Control Enable must be set to 1 or 3. Speed Control To allow the 1333 Series D to accept the 1332-MOD-F speed potentiometer signal, Parameter 9 Local/Remote Speed Enable must be set to 1, 2 or 3. A-1 Appendix A Bulletin 1333 Options 1333MODG4 1333MODG4 Bulletin 1333 Series D BCD Interface Board BCD Interface Control and Signal Wiring Terminal Block Terminal Block TB3 Drive Ratings ZABCAA Customer Supplied Term 1 Components Term 2 Term 3 Term 3 Remote Term 4 Term 4 Manual Speed Pot Term 5 Term 6 Remote Manual Term 7 Direction Switch Term 8 Term 9 Term 10 1333MODG4 Term 11 BCD Interface Board Terminal Block TB2 115V AC Term 1 Supply Signal Term 2 Remote Auto/Man Switch 1333MODG4 BCD Interface Board Jumper J3 set for 230V 1333MODG4 Bulletin 1333 Series D BCD Interface Board Power Terminal Block Terminal Block TB4 Term 1 Term L2/S Term 2 Term L3/T Term 3 VoltsperHertz, Maximum Frequency and Base Frequency The frequency range of the 1333-MOD-G4 BCD Interface Board and the Bulletin 1333 Series D drive must match. Once the scaling jumper on the BCD Interface Board has been set, Parameter 3 Frequency Range must be set to either 60 or FF. If set to FF, both Parameter 15 Maximum Frequency and Parameter 16 Base Frequency must also be set. BCD Interface Scaling Jumper Parameter 3 Parameter 15 Parameter 16 60Hz 60 -- -- 120Hz FF 60Hz 120Hz 200Hz FF 60Hz 200Hz Important: When Parameter 3 is set to FF, the drive volts-per-Hertz output will reach the maximum voltage at the value set by Parameter 16. Applications where volts-per-Hertz curves are required to reach maximum voltage other than at 50 or 60 Hz are primarily provisions for operating custom motors. For application assistance in these special ranges, contact your nearest Allen-Bradley representative. A-2 Appendix A Bulletin 1333 Options 1333MODG4 1333MODG4 Bulletin 1333 Series D BCD Interface Board BCD Interface Control and Signal Wiring Terminal Block Terminal Block TB3 Drive Ratings AABCAB Customer Supplied Term 1 Components Term 2 Term 3 Term 3 Remote Term 4 Term 4 Manual Speed Pot Term 5 Term 6 Remote Manual Term 7 Direction Switch Term 8 Term 9 Term 10 1333MODG4 Term 11 BCD Interface Board Terminal Block TB2 115V AC Term 1 Supply Signal Term 2 Remote Auto/Man Switch 1333MODG4 BCD Interface Board Jumper J3 set for 115V 1333MODG4 BCD Interface Board Terminal Block TB4 Term 1 Remote 115V AC Term 2 1Phase Term 3 AC Supply Speed Control To allow the 1333 Series D to accept the 1333-MOD-G4 0-10V DC speed signal, Parameter 9 Local/Remote Speed Enable must be set to 2. Forward/Reverse Control If the 1333 Series D is to have its forward/reverse operation controlled from the Local Control and Programming Panel, Parameter 8 Local/Remote Control Enable must be set to 0 or 2. If the 1333 Series D is to have its forward/reverse operation controlled by the BCD Interface Board, Parameter 8 Local/Remote Control Enable must be set to 1 or 3. Important: If Parameter 8 is set to 1 or 3, an external means of start/stop control must be connected to the Control and Signal Wiring Terminal Block. Refer to Chapter 4 for additional information. A-3 Appendix A Bulletin 1333 Options Bulletin 1333 Series D 1333MODKA1, KA2, KB1, KB2 Power Terminal Block Heavy Duty Dynamic Braking P Dynamic Term +BUS Brake Term -BUS Unit N Stop Setting If Heavy Duty Dynamic Braking is installed, Parameters 11 and 14 must be set to 0. A-4 Appendix B Preventive Maintenance and Troubleshooting Common Drive Problems Preventive Maintenance The Bulletin 1333 is convection cooled by air flowing through the heat sink slots. The slots must never be allowed to become obstructed with dirt or foreign matter. Periodically check and clean the heat sink slots. Problems with Your Drive? The following descriptions indicate the operation of protective circuitry in Check the Following First the Series D Bulletin 1333. What is thought to be a drive operational problem, may in reality be normal protection circuit operation. Refer to the following precheck procedures and Chapter 5 –– Operation and Programming before attempting to troubleshoot your drive. Precheck Procedures Acceleration Stall Protection -- No Fault is Displayed The Reason During motor acceleration, if current exceeds 140% of rated Drive current or 125% of Parameter 7, the overcurrent stall protection circuit operates. In order to guard against currents in excess of these values and prevent an overcurrent trip, this circuit temporarily stops drive acceleration. When load current is again below these values, the circuit lets the drive continue to accelerate to set frequency. Precheck Procedure If the application does not require this function it can be deactivated by setting Parameter 17 to 0. Deceleration Stall Protection -- No Fault is Displayed The Reason During motor deceleration, if current exceeds 140% of rated Drive current or 125% of Parameter 7, the overcurrent stall protection circuit operates. In order to guard against currents in excess of these values and prevent an overcurrent trip, this circuit temporarily stops drive deceleration. When load current is again below these values, the circuit lets the drive continue to decelerate to set frequency. Precheck Procedure Both Parameters 18 and 46 will protect the drive from nuisance trips during motor deceleration. If the application does not require this function it can be deactivated by setting Parameters 18 and/or 46 to 0. B-1 Appendix B Preventive Maintenance and Troubleshooting Common Drive Problems Over Current Protection -- OC is Displayed The Reason If overcurrent exceeds 200% of rated Drive current or if a ground fault occurs at the drive output leads, this protective circuit will shut off the drive transistors. Precheck Procedure 1. Load inertia is excessively large and programmed acceleration time is extremely short. Setting Parameter 17 to 1 or increasing the value of Parameter 1 will guard against OC nuisance trips. 2. The motor experienced an excessive overload condition. If the drive tripped on acceleration, setting Parameter 7 to a higher current limit setting may avoid OC nuisance trips. If the drive trips only on deceleration, enabling Parameter 46 may avoid OC nuisance trips on deceleration. 3. A short circuit exists in the drive output leads or in the motor windings. 4. A ground fault exists in the drive output leads or in the motor windings. 5. A device in the Drive output inverter section has shorted. Over Load Protection -- OL is Displayed The Reason If Parameter 6 is set to 0 and current exceeds 140% of rated Drive current for 60 seconds, this protective circuit will shut off the drive transistors. If Parameter 6 is set to a value other than 0 and current exceeds 115% of Parameter 7 for 60 seconds, this protective circuit will shut off the drive transistors. Precheck Procedure 1. The starting load is above 140%. The Drive is attempting to start the load, but Parameter 17 is preventing it. Disable Parameter 17. 2. The running load has been above 140% for one minute. The Drive may be in accel frequency hold if below the current limit set by Parameter 7, or in accel frequency hold if at the current limit set by Parameter 7. Check Parameters 17 and 6. If neither accel frequency hold nor overload protection is selected, the Drive has been between 140% and 180% of rated current for one minute, tripped out, and is functioning normally. 3. The running load has been above 115% of Parameter 7 for 60 seconds causing the motor to overheat and the drive to trip. Check Parameters 17 and 7, then check to see if Parameter 6 is set to a value other than 0. B-2 Appendix B Preventive Maintenance and Troubleshooting Common Drive Problems Over Voltage Protection -- OU Displayed The Reason When DC bus voltage rises above a preset level due to high incoming line voltage or excessive regenerative energy, this protective circuit stops transistor operation and annunciates the condition as shown. Precheck Procedure 1. Check and correct the incoming line voltage. Refer to Chapter 3 –– Specifications for acceptable voltage levels. 2. An extremely short deceleration time is the primary cause of excessive regenerative line energy. Setting Parameter 18 to 1 or increasing Parameter 2 will guard against OU nuisance trips. It may also be necessary to add the Heavy Duty Dynamic Braking option. Low Voltage Protection -- LU is Displayed The Reason When incoming line voltage falls below 90% for 15 ms, this protective circuit stops transistor operation to guard against incorrect drive operation. Precheck Procedure If the momentary power failure is less than 15 ms, operation is not interrupted. If more than 15 ms, the drive will trip and line voltage must be restored by cycling power. If automatic restart of the drive is required, set Parameter 48 to 1 or 2 as detailed in Chapter 5. Over Temperature Protection -- OH is Displayed The Reason When heat sink temperature rises above + 50°C, this protective circuit stops transistor operation and annunciates the condition as shown. Precheck Procedure Check the drive ambient temperature. For 7 1/2-20 HP (5.5-15 kW) units, check the cooling fan. B-3 Appendix B Preventive Maintenance and Troubleshooting Common Drive Problems Auxiliary Interlock Trip -- AU is Displayed The Reason It is possible that the drive was stopped by an external interlock. External interlocks (a thermal overload relay or an external sequence circuit for example), are connected to terminals 16 and 17 at the Control and Signal Wiring Terminal Block. Precheck Procedure Refer to Chapter 4 Installation and Wiring for a detailed explanation of external interlocks. Operating Error -- OP is Displayed The Reason The drive must always receive a valid stop command before it can run. This fault will be displayed and the drive will not start if: 1. The local stop pushbutton is pressed to stop the drive and Parameter 8 is set to 1 or 3. 2. A remote stop signal is sent and Parameter 8 is set to 2. 3. Parameter 8 is set to 1 or 3 and an external stop signal is not present when power is applied to the drive. Precheck Procedure 1. Send an external stop signal to clear the fault, then try again. 2. Press the local stop pushbutton to clear the fault, then try again. 3. Ensure that an external stop signal is present before reapplying power to the drive, then try again. Operating Error -- CPU is Displayed The Reason CPU is an internal software communications error. A CPU error will not be stored in the drive fault buffers. Precheck Procedure Clear the fault by removing then reapplying power to the drive. B-4 Appendix B Preventive Maintenance and Troubleshooting Common Drive Problems Troubleshooting Eight common problems that may be experienced when operating the Common Drive Problems Series D Bulletin 1333 and their solutions are listed in the remaining pages of this section. 1. The motor will not run. 2. The motor will not run continuously. 3. The motor generates an excessive amount of heat 4. The drive will not reverse in local control. 5. The drive will not ramp-to-stop. 6. The drive will not accelerate to maximum speed. 7. The drive will not decelerate to minimum speed. 8. An input line fuse has blown. ATTENTION: Power must be applied to the drive with the cover removed to perform certain troubleshooting checks. Voltages on ! many components are at incoming line potential or bus voltage. To avoid electric shock or damage to equipment, do not touch any drive components with power applied. ATTENTION: Become familiar with the equipment and read through the wiring, speed selection and adjustment sections before ! attempting to perform the startup procedures. Adjustments may be required to meet specific load characteristics or operator preference. Exercise extreme care when performing any task on the drive. Failure to do so may result in electric shock or equipment damage. As shown in Figures B-1 and B-2, a DC bus neon light at the top of the 1333 has been provided to provide visual indication that bus voltage is present. Bus voltage may be verified by using a voltmeter and measuring the voltage between +BUS and –BUS on the Power Terminal Block. Do not attempt to service the drive until 2 minutes after the neon light has extinguished and bus voltage has discharged to zero volts. B-5 Appendix B Preventive Maintenance and Troubleshooting Common Drive Problems DC Bus Neon Light Lock Switch Control and Signal Wiring Terminal Block Power Terminal Block Auxiliary Interlock Drive Nameplate Figure B1 -- 3/45HP (.554kW) 1333 parts, switches and terminal blocks shown in Figures B-1 and B-2 are referenced throughout the remainder of this chapter. 1. The motor will not run -- AU is displayed. No Are Terms 16 and 17 at the Control and Signal Wiring Terminal Block Remove the cause of the interlock fault or jumper terminals 16 and 17 if an jumpered? Is an auxiliary interlock installed between Terms 16 and 17? auxiliary interlock is not required. Yes Contact your nearest AB representative for application assistance. B-6 Appendix B Preventive Maintenance and Troubleshooting Common Drive Problems DC Bus Neon Light Lock Switch Control and Signal Wiring Terminal Block Auxiliary Interlock Power Terminal Block Drive Nameplate Figure B2 -- 71/220HP (5.515kW) 1. The motor will not run -- OH is displayed. No Lower the ambient temperature, clean the heat sink, or replace the cooling Is ambient temperature above the rated limit of 505C? Are the cooling fins fan. clogged or is the heat sink dirty? For 71/220HP (5.515kW) units, is the cooling fan rotating? Yes Contact your nearest AB representative for application assistance. B-7 Appendix B Preventive Maintenance and Troubleshooting Common Drive Problems 1. The motor will not run -- No fault is displayed. No R S T Is rated input voltage present at terminals / , / , and / ? Check input side for circuit breaker trip, contactor coil malfunction, blown L1 L2 L3 fuse, etc. Yes No Is the decimal point in the mode display lit? The drive is in the programming mode. Give the drive a valid stop command and press the lock switch. The decimal point in the mode display will light and the local or remote control source currently controlling the drive will be displayed. Yes No Is Parameter 8 set correctly? Parameter 8 settings. 0 = Local start/stop control without maintained external stop. 1 = Remote 2wire start/stop control at the Control and Signal Wiring Terminal Block. 2 = Local start/stop control with maintained external stop. 3 = Remote 3wire start/stop control at the Control and Signal Wiring Yes Terminal Block. No Is Parameter 9 set correctly? Parameter 9 settings. 0 = Local speed control. 1, 2 or 3 = Remote speed control only at the Control and Signal Wiring Terminal Block -- Terms 1, 2 and 3. 1 = External speed pot or 05V DC. 2 = External speed pot or 010V DC. Yes 3 = External speed pot or 420mA. No Are Parameters 6 and 7 set correctly? If Parameter 6 is set to a value other than 0, Parameter 7 is active. Parameter 7 must then be set to the motors nameplate current rating. Yes U V No Are the motor leads securely connected to drive output terminals / , / T1 T2 Verify and change connections if necessary. W and / ? T3 Yes Contact your nearest AB representative for application assistance. B-8 Appendix B Preventive Maintenance and Troubleshooting Common Drive Problems 1. The motor will not run -- OP is displayed. Yes Is Parameter 8 Local/Remote Control set to 1 (external control)? The drive is set for 2wire external control. Check for correct wiring at the Control and Signal Wiring Terminal Block. Reset the drive with an external stop command. No Yes Is Parameter 8 Local/Remote Control set to 2 (local control)? An external maintained stop signal must first be present to start the drive. Check for correct wiring at the Control and Signal Wiring Terminal Block Reset the drive by pressing the local stop button. No Yes Is Parameter 8 Local/Remote Control set to 3 (external control)? The drive is set for 3wire external control. Check for correct wiring at the Control and Signal Wiring Terminal Block. Reset the drive with an external stop command. 2. The motor will not run continuously -- LU is displayed. Yes Has incoming line voltage dropped below 90% of rated voltage? Monitor the incoming line voltage and correct the condition. No Contact your nearest AB representative for application assistance. B-9 Appendix B Preventive Maintenance and Troubleshooting Common Drive Problems 2. The motor will not run continuously -- OC is displayed. Yes Does a short circuit exist in the output leads or motor windings? Remove the cause of the short circuit. No Yes Does a ground fault exist between the drive output leads and the motor or in Remove the cause of the ground fault. the motor windings? No Yes Does the drive trip when the speed reference is below 5.0Hz? Is the application a fan or pump system? No Yes Reduce the boost setting Change the V/Hz ramp to in Parameter 5. variable by setting Parameter 4 to 1, then No reduce the boost level setting in Parameter 5 if required. Yes Is the acceleration time too short? Is Parameter 17, Accel Frequency Hold Increase the value of Accel Time 1 Parameter 1, or set Parameter 17 Accel off? Frequency Hold on. No No Program Parameter 46 Current Limit to eliminate nuisance tripping, lighten Is the load within the rated current of the drive? the load, or resize the drive and motor to meet your application. Yes No Is OC displayed even if the drive output leads are disconnected? Verify motor operation by line operating the motor or repeating the above. Is the motor now operating correctly? Yes Yes No Contact your nearest AB representative for application assistance. B-10 Appendix B Preventive Maintenance and Troubleshooting Common Drive Problems 2. The motor will not run continuously -- OL is displayed. No Is the load current equal to the motor nameplate rating? Is the load current An OL trip occurs when the load current is greater than 140% for one minute. Lighten the load or resize the drive and motor to meet your application. within the rated current of the drive? Yes No Is Parameter 6 set to 1, 2 or 3? When set to 1, 2 or 3, the thermal overload function is enabled. Check for the correct setting as detailed in Chapter 5. Yes Yes Is Parameter 7 set to the rated motor nameplate value? An OL trip occurs when the load current is greater than 125% of the overload current value set in Parameter 7 for one minute. Lighten the load or resize the drive and motor to meet your application. No Set Parameter 7 to the rated motor nameplate value. 2. The motor will not run continuously -- OU is displayed. Yes Is the incoming AC power line high? Monitor and correct the AC line. No Yes Is the deceleration time too short? Is Parameter 18, the Decel Frequency Increase the value of Decel Time 1 Parameter 2, or set Parameter 18 Decel Hold off? Frequency Hold on. No Yes Is an overhauling load present -- Does the load increase the motor speed Increase the value of Parameter 14 DC Hold Volts. Install the Heavy Duty beyond the drive set speed? Dynamic Brake Option. Does the problem still exist? No Yes Contact your nearest AB representative for application assistance. B-11 Appendix B Preventive Maintenance and Troubleshooting Common Drive Problems 3. The motor generates an excessive amount of heat -- No fault is displayed. Yes Is full load demanded continuously at low frequency? An OL trip occurs when the load current is greater than 140% for one minute. Lighten the load or resize the drive and motor to meet your application. No Yes Is the motor operating above the full load current? The load is beyond the motor capacity. Check the mechanical installation. If the motor and drive are undersized, resize them for your application. No Check the motor and wiring connections for an open phase condition. 4. The drive will not reverse in local control -- No fault is displayed. No Has the drive been programmed to lockout reverse operation (Parameter 10 Set Parameter 10 to 0. set to 1)? Yes Contact your nearest AB representative for application assistance. B-12 Appendix B Preventive Maintenance and Troubleshooting Common Drive Problems 5. The drive will not ramptostop -- No fault is displayed. No Is Parameter 11 Stop Select set to ramptostop? Set Parameter 11 to 0. Yes Yes Does Parameter 59 show an OU fault stored? The drive is tripping on overvoltage during decel. Refer to page B3. No No Is the DC Hold Frequency set to high -- Is parameter 12 set to 00.50 Hz? Set Parameter 12 to 00.50 Hz. Yes Yes Is Parameter 18 Decel Frequency Hold on -- Does the motor have an If Parameter 18 Decel Frequency Hold is set to 1 (On), an overhauling load overhauling load? may cause the decel ramp to hold at one frequency for an extended period. This may cause ramptostop commands to appear to be nonfunctional. No Contact your nearest AB representative for application assistance. B-13 Appendix B Preventive Maintenance and Troubleshooting Common Drive Problems 6. The drive will not accelerate to maximum speed -- No fault is displayed. No The maximum allowable drive output frequency will be determined by the Reset Parameters 3 and/or 15. lowest programmed value of any of the following parameters: • Parameter 3 Frequency Range • Parameter 15 Maximum Frequency • Parameter 51 Upper Frequency Clamp • Parameter 53 Bias Frequency -- If Parameter 53 is Higher Than Parameter 54 • Parameter 54 Gain Frequency -- If Parameter 54 is Higher Than Parameter 53 Is Parameters 3 Frequency Range and/or 15 Maximum Frequency set high enough to allow the drive to accelerate to maximum speed? Yes No Is Parameter 51 Upper Frequency Clamp set to a value lower than the Reset Parameter 51 to maximum frequency. required maximum frequency? Yes Yes Is this an inverse speed follower application? To program the drive for an inverse speed follower application, set Parameter 53 to the maximum frequency required and Parameter 54 to the minimum frequency required. Yes Yes Is Parameter 53 Bias Frequency set to a higher value than Parameter 54 Gain If an inverse speed follower is required, reprogram Parameter 53 to maximum Frequency (standard setting for inverse speed follower applications)? frequency. If an inverse follower is not required, reprogram Parameters 53 and 54 as required. No Yes Is Parameter 53 Bias Frequency set to a lower value than the required Reset Parameter 53 to maximum Frequency. maximum frequency? No Yes Reprogram Parameters 42, 43 and/or 44 to a value below the maximum Are Parameters 4245 programmed to exclude maximum frequency? frequency. Reprogram Parameter 45 to a bandwidth that will not include the maximum frequency value. No Contact your nearest AB representative for application assistance. B-14 Appendix B Preventive Maintenance and Troubleshooting Common Drive Problems 7. The drive will not decelerate to minimum speed -- No fault is displayed. No The priority used by the 1333 to limit minimum output frequency is: Reset Parameter 50 to minimum frequency. 1. For local speed control, use Parameter 50. 2 If an external potentiometer, 05VDC, 010VDC or 420mA signal is to control drive speed, use the higher of the values set by Parameters 15 and 51. Is Parameter 50 Lower Frequency Clamp set to a value higher than the required minimum frequency? Yes Yes Is 0 output speed required at a 0 external input signal? To program the drive for a directly proportional input signal, set Parameter 53 to the minimum frequency required and Parameter 54 to the maximum frequency required. No Yes Are Parameters 4244 Skip Frequencies 1, 2 and 3 and/or Parameter 45 Reprogram Parameters 42, 43 and/or 44 to a value above minimum programmed to exclude minimum frequency? frequency. Reprogram Parameter 45 to a bandwidth that will not include the minimum frequency. No Contact your nearest AB representative for application assistance. 8. An input line fuse has blown -- No fault is displayed. No Are the drive input fuses sized in accordance with the values given in Chapter Replace with the correct fuses. 4 Installation and Wiring? Yes No Are the drive input and output terminals wired as shown in Chapter 4 Wire as shown. Do the input fuses still blow? Installation and Wiring. Yes Yes Contact your nearest AB representative for application assistance. B-15 Appendix C Factory and Field Parameter Settings Parameters Grouped by Function The following tables in Appendix C provide parameter data grouped by function. The function groups listed, reference the same parameters as grouped in Chapters 5 and 6 and Appendix B. Factory and Field Parameter Settings -- Pages C2 and C3 The table on the left provides parameter units, min/max values, factory settings and room to record field settings. Coordinated Parameter Settings -- Pages C4 and C5 The table on the right graphically shows which of the remaining parameters must be checked to provide coordinated control of the Bulletin 1333 for each parameter. For each parameter (numbered 0 I – 62 ) in the first column, a n in the remaining columns (numbered 01-62) will indicate parameters that should be checked to provide coordinated drive control. C-1 Appendix C Factory and Field Parameter Settings Factory and Field Parameter Settings -- Parameters 0128 Function Parameter Parameter Factory Field Group Number Name Units Range Setting Setting Accel and Decel 0I ACCEL TIME 1 Seconds 0000/1600 005.0 Settings 02 DECEL TIME 1 Seconds 0000/1600 005.0 VoltsperHertz Curve 03 FREQUENCY RANGE Code 50/60/FF 60 Settings 04 VOLTSPERHERTZ CURVE Code 0/1 0 DC Boost Setting 05 DC BOOST SELECT % of Output Voltage 00/40 00 Overload Protection 06 MOTOR DUTY Code 0/1/2/3 2 Settings 07 OVERLOAD CURRENT Amps 000.1/500.0¶ Local/Remote Control Enable 08 LOCAL/REMOTE CONTROL Code 0/1/2/3 0 Local/Remote Speed Enable 09 LOCAL/REMOTE FREQUENCY Code 0/1/2/3 0 Reverse Enable I0 REVERSE LOCKOUT Off/On 0/1 0 Stop Setting II STOP SELECT Code 0/1 0 DC Brake I2 DC HOLD FREQUENCY Hertz 00.50/60.00 00.50 Settings I3 DC HOLD TIME Seconds 000/10.0 000 I4 DC HOLD VOLTS Code 0/10 0 Max Speed I5 MAXIMUM FREQUENCY Hertz 50.00/400.0 60.00 Settings I6 BASE FREQUENCY Hertz 50.00/250.0 60.00 Accel and Decel Hold I7 ACCEL FREQUENCY HOLD Off/On 0/1 1 Enable I8 DECEL FREQUENCY HOLD Off/On 0/1 1 Preset Frequency and I9 FREQUENCY SELECT Code 0/1/2 0 Aux Accel/Decel Enable 20 TB15 PRESET/RESET Code 0/1 0 Aux Interlock Enable 2I AUXILIARY INTERLOCK Code 0/1 0 Drive Supplied Contact 22 CR1 SELECT Code 1/2/3 1 Settings 23 CR2 SELECT Code 0/1/2/3 0 24 CR1 FREQUENCY Hertz 00.50/400.0 00.50 25 CR2 FREQUENCY Hertz 00.50/400.0 00.50 Jog 26 JOG FREQUENCY Hertz 00.50/20.00 10.00 Settings 27 JOG ACCEL TIME Seconds 0000/1600 005.0 28 JOG DECEL TIME Seconds 0000/1600 005.0 ¶ Factory setting is determined by the output current rating shown on the drive nameplate. C-2 Appendix C Factory and Field Parameter Settings Coordinated Parameter Settings -- Parameters 0128 01 02 03 04 05 06 07 08 09 10 11 12 13 14 15 16 17 18 19 20 21 22 23 24 25 26 27 28 29 30 31 32 33 34 35 36 37 38 39 40 41 42 43 44 45 46 47 48 49 50 51 52 53 54 55 56 57 58 59 60 61 62 0I 02 03 04 05 06 07 08 09 I0 II I2 I3 I4 I5 I6 I7 I8 I9 20 2I 22 23 24 25 26 27 28 C-3 Appendix C Factory and Field Parameter Settings Factory and Field Parameter Settings -- Parameters 2962 Function Parameter Parameter Factory Field Group Number Name Units Range Setting Setting Preset Frequency 29 PRESET FREQUENCY 2 Hertz 00.50/400.0 20.00 Settings 30 PRESET FREQUENCY 3 Hertz 00.50/400.0 30.00 3I PRESET FREQUENCY 4 Hertz 00.50/400.0 40.00 32 PRESET FREQUENCY 5 Hertz 00.50/400.0 15.00 33 PRESET FREQUENCY 6 Hertz 00.50/400.0 25.00 34 PRESET FREQUENCY 7 Hertz 00.50/400.0 35.00 35 PRESET FREQUENCY 8 Hertz 00.50/400.0 45.00 Auxiliary Accel and Decel 36 ACCEL TIME 2 Seconds 000.1/1600 005.0 Settings 37 DECEL TIME 2 Seconds 000.1/1600 005.0 38 ACCEL TIME 3 Seconds 000.1/1600 005.0 39 DECEL TIME 3 Seconds 000.1/1600 005.0 40 ACCEL TIME 4 Seconds 000.1/1600 005.0 4I DECEL TIME 4 Seconds 000.1/1600 005.0 Skip Frequency 42 SKIP FREQUENCY 1 Hertz 0000/400.0 0000 Settings 43 SKIP FREQUENCY 2 Hertz 0000/400.0 0000 44 SKIP FREQUENCY 3 Hertz 0000/400.0 0000 45 SKIP FREQUENCY BAND Hertz 0/10 0 Current Limit Setting 46 CURRENT LIMIT Seconds 00/1.5 00 Auto Restart Settings 47 POWER LOSS RESTART Code 0/1/2/3 1 48 RIDETHRU RESTART Code 0/1/2 0 49 RESTART TIME SELECT Seconds 000.1/100.0 000.1 Lower and Upper 50 LOWER FREQUENCY CLAMP Hertz 00.50/400.0 00.50 Frequency Clamp Settings 5I UPPER FREQUENCY CLAMP Hertz 00.50/400.0 400.0 Bias and Gain 52 BIAS AND GAIN ENABLE Off/On 0/1 0 Settings 53 BIAS FREQUENCY Hertz 00.00/400.0 00.00 54 GAIN FREQUENCY Hertz 00.50/400.0 60.00 Output Meter 55 FREQUENCY OUTPUT (AMPS) % of Max Output Signal 075/125 100 Settings 56 FREQUENCY OUTPUT (VOLTS) % of Max Output Signal 075/125 100 Monitoring Mode 57 MONITOR DISPLAY SELECT Code 0/1/2 0 Settings 58 MOTOR POLE SELECT Units 2/4/6/8/10 4 Drive Fault Memory 59 FAULT BUFFER 0 Code -- -- -- 60 FAULT BUFFER 1 Code -- -- -- 6I FAULT BUFFER 2 Code -- -- -- 62 FAULT BUFFER 3 Code -- -- -- C-4 Appendix C Factory and Field Parameter Settings Coordinated Parameter Settings -- Parameters 2962 01 02 03 04 05 06 07 08 09 10 11 12 13 14 15 16 17 18 19 20 21 22 23 24 25 26 27 28 29 30 31 32 33 34 35 36 37 38 39 40 41 42 43 44 45 46 47 48 49 50 51 52 53 54 55 56 57 58 59 60 61 62 29 30 3I 32 33 34 35 36 37 38 39 40 4I 42 43 44 45 46 47 48 49 50 5I 52 53 54 55 56 57 58 59 60 6I 62 C-5 Appendix D Application Data Important User Information Because of the variety of uses for this equipment and because of the differences between this solid state equipment and electromechanical equipment, the user of and those responsible for applying this equipment must satisfy themselves as to the acceptability of each application and use of the equipment. In no event will Allen-Bradley Company be responsible or legal for indirect or consequential damages resulting form the use or application of this equipment. The illustrations shown are intended solely to illustrate the accompanying text. Because of the many variables and requirements associated with any particular installation, the Allen-Bradley Company cannot assume responsibility or liability for actual use based upon the illustrative uses and applications. Remote Manual and Remote Auto The Bulletin 1333 Series D may use the Directional Pushbuttons on the Speed Reference Switching Local Control and Programming Panel or an external source as its speed reference. The method of speed control that is used is determined by parameter programming as explained in Chapter 5. Four types of signals may be used as the external speed reference. 1. A 10kΩ, 2W potentiometer. 2. A 0-5V DC reference signal. 3. A 0-10V DC reference signal. 4. A 4-20 mA DC reference signal. As explained in the Control and Signal Wiring section of Chapter 4, only one of these signals should be connected to the Control and Signal Wiring Terminal Block at any time. There are times however, when a user may want the option of switching between a remote analog speed reference and a remote manual speed reference. The 1333 Series D normally will require reprogramming and reconnection to accomplish this. This application describes an alternate method of external speed selection. Users must satisfy themselves that this alternate method is safe in their particular application and that its use complies with applicable codes and standards. D-1 Appendix D Application Data The 1333 Series D has the ability to allow a single external 10kΩ, 2W manual speed potentiometer and one other reference signal to be connected to the drive at the same time. The drive may be switched from the manual potentiometer to the alternate reference signal by means of a selector switch. As shown in the Control and Signal Wiring section of Chapter 4, only one of these signals should be connected to the Control and Signal Wiring Terminal Block at any time. Shown below is a method of switching between an external speed pot and one alternate reference signal. Logic Logic Common Common 12 34 1 234 5 or 05V/Speed Pot 420mA/Speed Pot 010V/Speed Pot Drive Drive End End Shield Shield Pot Pot Pot Wiper Pot Pot Wiper Pot High Low High Low - + - + 4-20mA 05V External or External Speed Pot 0-10V Speed Pot Earth Earth Ground Ground The Bulletin 1333 Series D must be programmed for external speed control by setting Parameter 9 to: • 1 if drive speed is to be controlled by a 0-5V DC signal or an external speed pot. • 2 if drive speed is to be controlled by a 0-10V DC signal or an external speed pot. • 3 if drive speed is to be controlled by a 4-20 mA DC signal or an external speed pot. When the selector switch in series with the potentiometer is open, the drive will use the 0-5V DC, 0-10V DC, or 4-20 mA DC signal as the speed reference. When the selector switch is closed, the drive will use the potentiometer signal as the speed reference. If the selector switch is toggled while the drive is running, the drive will accelerate or decelerate to the new speed reference at the programmed accel or decel rate. D-2 Appendix D Application Data Bulletin 1333 The Bulletin 1333 Adjustable Frequency Drive has the ability to let a Heavy Duty Dynamic Braking connected motor generate braking torque. This ability however, is limited to approximately 20% of the drive rated braking torque. The braking torque can be increased by adding one or more Bulletin 1333 heavy duty dynamic braking kits to the drive. Typically the braking torque can be increased to 100% for 20 seconds at a duty cycle of 20%. The following evaluation can help determine if heavy duty dynamic braking may be required for your application. Brake Specifications Braking Torque: 100% Torque for 20 Seconds (typical) Duty Cycle: 20% (typical) Input Power: Power from Drive DC Bus Temperature: –10 to + 50°C (+14 to +122°F). Humidity: 5 to 95% Non-Condensing Atmosphere: No Corrosive Gas or Non-Hazardous Dust Humidity: 3,300 Feet (1,000 Meters) Maximum without Derating Enclosure Type: NEMA Type 1 (IP20) How to Select a Brake To begin selection, the following application information must be obtained. The nameplate horsepower of the motor HP. The nameplate base speed of the motor N in RPM. The speed profile of the motor N 2 RPM N 1 RPM t 2 t 1 where: N = The motor’s minimum speed in RPM. 1 N = The motor’s maximum speed in RPM. 2 t = The motor’s cycle time in seconds. 1 t = The motor’s decel time in seconds. 2 Motor Gear Load The motor inertia, Inertia Ratio Inertia the nameplate gear reduction 2 2 wk GR wk M L Input Output ratio, and the load inertia. RPM RPM D-3 Appendix D Application Data Step 1 -- Determine the Rated Motor Torque TQ = 5250 × HP HP = The nameplate horsepower of the motor M N = The nameplate base speed of the motor N TQ = 5250 × TQ = LBFT M M Step 2 -- Determine the Total Inertia 2 2 2 2 2 wk t = wk + [wk × (GR) ] wk = The motor inertia M L M 2 wk = The load inertia L GR = The total reduction ratio Output RPM Input RPM 2 2 2 2 wk t = + [ × ( ) ] wk t = LBFT Step 3 -- Determine the Required Braking Torque 2 2 TQ = wk t × [N - N ] wk t = The total inertia B 2 1 N = The motor's maximum speed 2 308 × t 2 N = The motor's minimum speed 1 t = The motor's decel time 2 TQ = LBFT TQ = [ ] × [ - ] B B 308 × [ ] Step 4 -- Determine the Required Percent of Braking Torque TQ = TQ × 100 TQ = The required braking torque B % B TQ = The rated motor torque M TQ M TQ = [ ] × 100 TQ = % % % [ ] If TQ is less than 20%, heavy duty dynamic braking is not required. The % inherent braking of the drive should be sufficient to handle the application requirements. If TQ is 20% or more, a heavy duty braking kit is required. Continue to % Step 5. D-4 Appendix D Application Data Step 5 -- Determine the Maximum Generated Braking Torque Three factors limit the application of Heavy Duty Dynamic Braking. The first is the brake assembly rating P –– The peak power the brake T assembly can absorb at any instant regardless of the time limit. The second is the average power that the break assembly can absorb during one braking duty cycle –– P . A The third is the duty cycle or the number of times the brake assembly can be operated over a given period of time –– DC. TQ = The required braking torque P = TQ × N B M B 2 N = The motor's maximum speed 2 7,000 P = [ ] × [ ] P = kW M M 7,000 P must be less than or equal to the Brake Assembly Rating listed in table 1. M If P exceeds the P value shown, the corresponding drive/brake M T configuration will not be able to produce the braking torque required for your application, and the drive will trip on an overvoltage fault. Increasing 2 the decel time t , reducing the load inertia wk L, or doing both will lower 2 TQ and P . B M table 1 Nominal To provide the maximum To provide a Drive HP amount of braking torque use brake assembly rating (PT) of 3/4 (1) KA1 for a 208/230VAC Unit 1.2kW (1) KB1 for a 460VAC Unit 1 (1) KA1 for a 208/230VAC Unit 1.2kW (1) KB1 for a 460VAC Unit 2 (1) KA2 for a 208/230VAC Unit 2.4kW (1) KB2 for a 460VAC Unit 3 (1) KA3 for a 208/230VAC Unit 6kW (1) KB3 for a 460VAC Unit 5 (1) KA3 for a 208/230VAC Unit 6kW (1) KB3 for a 460VAC Unit 71/2 (1) KA4 12kW 10 (1) KA4 12kW 15 (1) KA5 24kW 20 (1) KA5 24kW D-5 Appendix D Application Data Step 6 -- Determine the Average Power Generated in One Cycle TQ = The required braking torque P = TQ × [N + N ] B A B 1 2 N = The motor's minimum speed 1 14,000 N = The motor's maximum speed 2 P = kW A P = [ ] × [ + ] A 14,000 Step 7 -- Determine the Ratio of the Average Power to the Brake Assembly Rating P = P P = The average power generated in one cycle A % A P = The brake assembly rating from table 1 T P T P = [ ] P = % % % [ ] Find the intersection of P and the motor’s decel time t in the chart below. % 2 If the point of intersection is below the curve, the average power of one cycle is within the brake’s limits. If the point is above the curve, the average power is beyond the brake’s limits but may be reduced by 2 increasing the motor’s decel time t , reducing the load inertia wk , or 2 L doing both. P% 100 95 90 85 80 75 70 65 60 55 50 45 40 35 30 25 20 15 10 5 0 0 10 20 30 40 50 60 70 80 90 100 Decel Time t in Seconds 2 D-6 Appendix D Application Data Step 8 -- Determine if the Duty Cycle is within the Brake's Capability DC = t × 100 T = The motor's cycle time 1 2 T = The motor's decel time 2 t 1 DC = [ ] × 100 DC = % [ ] Find the intersection of P and the motor’s decel time DC in the chart % below. If the point of intersection is below the curve, the duty cycle is within the brake’s limits. If the point is above the curve, the duty cycle is beyond the brake’s limits but may be modified by increasing the motor’s cycle time t . 1 P% 100 95 90 85 80 75 70 65 60 55 50 45 40 35 30 25 20 15 10 5 0 051 105 202530 3540 45 50 Duty Cycle DC in % D-7 Appendix D Application Data Notes D-8 We Want Our Manuals to be the Best! You can help! Our manuals must meet the needs of you, the user. This is your opportunity to make sure they do just that. By filling out this form you can help us provide the most useful, thorough, and accurate manuals available. Please take a few minutes to tell us what you think. Then mail this form, FAX it, or send comments via E-Mail. FAX: to your local Allen-Bradley Sales Office or 414/242-8201 E-Mail: via Internet to “SEPATTER@ABPOST.remnet.ab.com” PUBLICATION NAME PUBLICATION NUMBER, DATE AND PART NUMBER (IF PRESENT) 3 CHECK THE FUNCTION THAT MOST CLEARLY DESCRIBES YOUR JOB. o SUGGEST / RESPONSIBLE FOR THE PURCHASE OF EQUIPMENT o MAINTAIN / OPERATE PROGRAMMABLE MACHINERY o DESIGN / IMPLEMENT ELECTRICAL SYSTEMS o TRAIN / EDUCATE MACHINE USERS o SUPERVISE FLOOR OPERATIONS 3 WHAT LEVEL OF EXPERIENCE DO YOU HAVE WITH EACH OF THE FOLLOWING PRODUCTS? NONE LITTLE MODERATE EXTENSIVE PROGRAMMABLE CONTROL ooo o AC / DC DRIVES ooo o PERSONAL COMPUTERS ooo o NC / CNC CONTROLS ooo o DATA COMMUNICATIONS / LAN ooo o 3 RATE THE OVERALL QUALITY OF THIS MANUAL BY CIRCLING YOUR RESPONSE BELOW. (1) = POOR (5) = EX- CELLENT HELPFULNESS OF INDEX / TABLE OF CONTENTS 1 2 3 4 5 CLARITY 1 2 3 4 5 EASE OF USE 1 2 3 4 5 ACCURACY AND COMPLETENESS 1 2 3 4 5 QUALITY COMPARED TO OTHER COMPANIES’ MANUALS 1 2 3 4 5 QUALITY COMPARED TO OTHER ALLEN-BRADLEY MANUALS 1 2 3 4 5 3 WHAT DID YOU LIKE MOST ABOUT THIS MANUAL? 3 WHAT DID YOU LIKE LEAST ABOUT THIS MANUAL? 3 PLEASE LIST ANY ERRORS YOU FOUND IN THIS MANUAL (REFERENCE PAGE, TABLE, OR FIGURE NUMBERS). ! 3 DO YOU HAVE ANY ADDITIONAL COMMENTS? 3 COMPLETE THE FOLLOWING. NAME COMPANY TITLE DEPARTMENT STREET CITY STATE ZIP TELEPHONE DATE CUT ALONG DOTTED LINE FOLD HERE FOLD HERE NO POSTAGE NECESSARY IF MAILED IN THE UNITED STATES BUSINESS REPLY MAIL FIRST CLASS PERMIT NO. 413 MEQUON, WI POSTAGE WILL BE PAID BY ADDRESSEE ALLEN-BRADLEY Attn: Marketing Communications P.O. Box 760 Mequon, WI 53092-9907 Publication 1333-5.2 July 1994 P/N 152783 Supersedes February 1994 and 1333-5.2DU1�DU2 � April 1994 Copyright 1994, Allen�Bradley Company, Inc. Printed in USA
Frequently asked questions
How does Industrial Trading differ from its competitors?

Is there a warranty for the 1333AAA?

Which carrier will Industrial Trading use to ship my parts?

Can I buy parts from Industrial Trading if I am outside the USA?

Which payment methods does Industrial Trading accept?

What they say about us
FANTASTIC RESOURCE
One of our top priorities is maintaining our business with precision, and we are constantly looking for affiliates that can help us achieve our goal. With the aid of GID Industrial, our obsolete product management has never been more efficient. They have been a great resource to our company, and have quickly become a go-to supplier on our list!
Bucher Emhart Glass
EXCELLENT SERVICE
With our strict fundamentals and high expectations, we were surprised when we came across GID Industrial and their competitive pricing. When we approached them with our issue, they were incredibly confident in being able to provide us with a seamless solution at the best price for us. GID Industrial quickly understood our needs and provided us with excellent service, as well as fully tested product to ensure what we received would be the right fit for our company.
Fuji
HARD TO FIND A BETTER PROVIDER
Our company provides services to aid in the manufacture of technological products, such as semiconductors and flat panel displays, and often searching for distributors of obsolete product we require can waste time and money. Finding GID Industrial proved to be a great asset to our company, with cost effective solutions and superior knowledge on all of their materials, it’d be hard to find a better provider of obsolete or hard to find products.
Applied Materials
CONSISTENTLY DELIVERS QUALITY SOLUTIONS
Over the years, the equipment used in our company becomes discontinued, but they’re still of great use to us and our customers. Once these products are no longer available through the manufacturer, finding a reliable, quick supplier is a necessity, and luckily for us, GID Industrial has provided the most trustworthy, quality solutions to our obsolete component needs.
Nidec Vamco
TERRIFIC RESOURCE
This company has been a terrific help to us (I work for Trican Well Service) in sourcing the Micron Ram Memory we needed for our Siemens computers. Great service! And great pricing! I know when the product is shipping and when it will arrive, all the way through the ordering process.
Trican Well Service
GO TO SOURCE
When I can't find an obsolete part, I first call GID and they'll come up with my parts every time. Great customer service and follow up as well. Scott emails me from time to time to touch base and see if we're having trouble finding something.....which is often with our 25 yr old equipment.
ConAgra Foods